Introduction
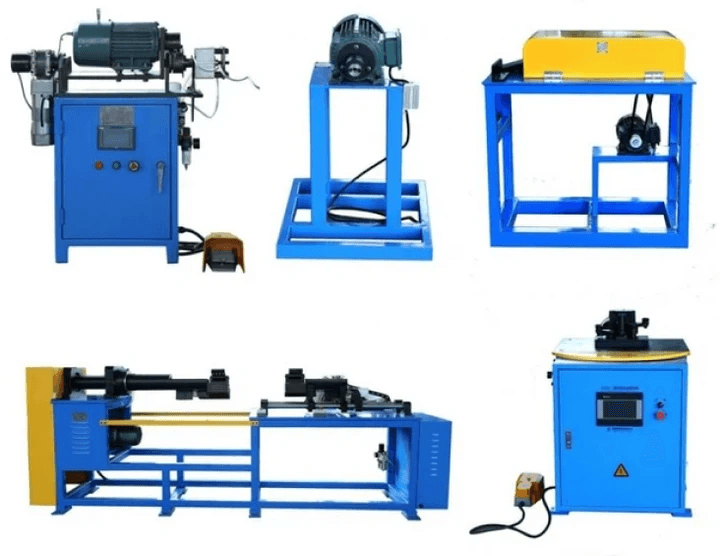
In the fast-paced world of manufacturing, the evolution of technology has led to remarkable advancements in wire forming techniques. The wire end forming machine stands at the forefront of this transformation, enabling manufacturers to achieve precision and efficiency previously thought unattainable. As industries continue to demand higher quality and faster production rates, understanding the benefits of these machines becomes essential for any modern production line.
The Evolution of Wire End Forming
Wire end forming has come a long way since its inception, transitioning from manual processes to sophisticated automated systems. Early methods relied heavily on skilled labor and rudimentary tools, which often resulted in inconsistencies and inefficiencies. Today, with innovations like CNC tube forming and advanced bending machines, manufacturers can create complex shapes with remarkable accuracy while minimizing waste.
Why Choose a Wire End Forming Machine
Investing in a wire end forming machine offers numerous advantages that can significantly enhance production capabilities. These machines are designed for versatility, allowing for a wide range of applications across various industries—from automotive components to electronic devices. By automating the wire forming process, businesses can reduce labor costs and improve turnaround times while maintaining high-quality standards.
Key Benefits for Modern Production
The key benefits of incorporating a wire end forming machine into your production line are hard to ignore. Firstly, they provide exceptional precision in shaping wire for bending applications, ensuring that each piece meets stringent specifications consistently. Secondly, their integration with cutting wire machines enhances overall productivity by streamlining operations and reducing manual handling—resulting in faster cycle times and increased output.
Understanding Wire End Forming Machines
Wire end forming machines are essential tools in modern manufacturing, designed to shape the ends of wire for various applications. These machines utilize advanced technology to create precise bends and forms that are critical for ensuring product reliability and performance. By streamlining the wire forming process, they significantly enhance productivity and reduce waste.
What is Wire End Forming
At its core, wire end forming is a specialized technique used to manipulate the ends of wires into specific shapes or configurations. This process can involve bending, twisting, or cutting wire to meet particular design specifications required in various industries. A wire end forming machine automates this procedure, providing consistent results that manual processes simply cannot match.
The Mechanism Behind the Process
The mechanism of a wire end forming machine typically involves several coordinated movements that allow for precision shaping of the wire. Initially, a cutting wire machine may trim the raw material before it enters the forming stage, ensuring optimal lengths are achieved for bending operations. Following this, specialized bending machines take over to create intricate designs through controlled movements that adapt based on programming inputs—often powered by CNC tube forming technology for enhanced accuracy.
Applications Across Various Industries
Wire end forming machines find their niche across numerous sectors such as automotive, aerospace, electronics, and construction. In automotive manufacturing, they produce components like clips and brackets that must fit precisely within tight tolerances; similarly in aerospace where safety is paramount and parts must endure rigorous conditions. Additionally, these machines facilitate innovative designs in consumer electronics by enabling complex wiring solutions essential for modern gadgets—showcasing just how versatile and vital wire forming processes have become.
The Role of Bending Machines
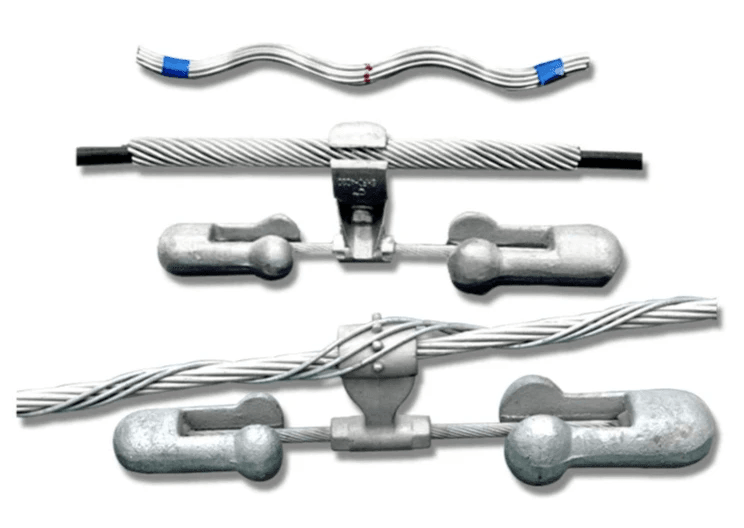
How Bending Machines Work
Bending machines operate by applying force to a specific section of wire, allowing it to bend at predetermined angles without compromising its structural integrity. The process typically involves clamping the wire securely while a bending arm or die applies pressure to create the desired shape. With various types of bending machines available—such as hydraulic and electric models—manufacturers can choose the right equipment that best suits their needs for wire end forming.
Benefits of Precision in Bending Wire
Precision is crucial when it comes to bending wire; even minor inaccuracies can lead to significant issues down the line in production processes. Accurate bends ensure that components fit together seamlessly, reducing waste and rework costs associated with misaligned parts. Moreover, using a high-quality bending machine allows for repeatable results, which is essential for maintaining consistency across large production runs.
Enhancing Productivity with Bending Machines
The introduction of modern bending machines has revolutionized how manufacturers approach productivity in their operations. By automating the bending process, these machines significantly reduce labor costs while increasing output rates—a win-win scenario for any factory floor! Additionally, when combined with cutting wire machines and other technologies like CNC tube forming systems, they streamline workflows and minimize downtime between processes.
The Cutting Wire Machine Advantage
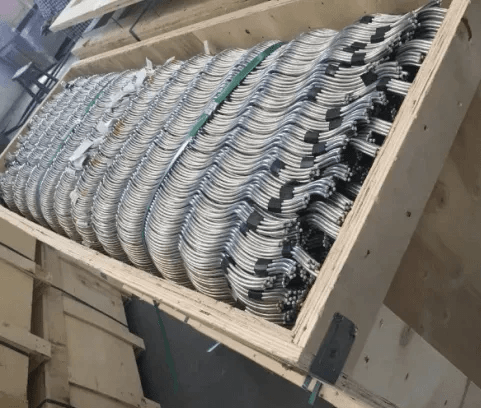
In the world of wire forming, cutting wire machines play a pivotal role in ensuring precision and efficiency. These machines are not just about slicing through metal; they are integral to the production process, impacting everything from quality control to workflow optimization. By utilizing advanced technology, manufacturers can achieve consistent results that elevate their products and streamline operations.
Importance of Wire Cutting in Production
Wire cutting is more than a mere step in the manufacturing process; it’s crucial for achieving the desired specifications in wire end forming and bending applications. A well-executed cut ensures that the wire for bending fits perfectly into subsequent processes, reducing waste and enhancing overall productivity. Moreover, precise cuts lead to better assembly and fitting in final products, which is essential across various industries.
Choosing the Right Wire Cutting Machine
Selecting the right cutting wire machine can be a game-changer for manufacturers looking to optimize their production line. Factors such as cutting speed, accuracy, and compatibility with other machinery—like bending machines—should be considered when making this decision. Investing in a high-quality wire cutting machine tailored to specific needs will ultimately enhance efficiency and reduce downtime during production.
Integration with Wire Forming Processes
The integration of cutting wire machines with other equipment like CNC tube forming systems is vital for seamless production workflows. When these machines work together harmoniously, they create an efficient line where each component complements the others—from initial cuts to final bends using a wire end forming machine or bending machine. This synergy not only boosts productivity but also allows for greater customization options, catering to diverse client demands while maintaining high standards of quality.
Innovations in CNC Tube Forming
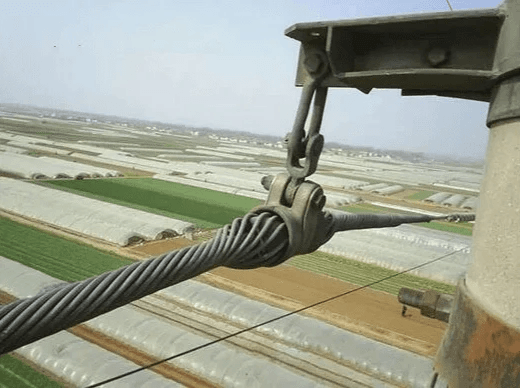
CNC tube forming represents a significant leap forward in the world of wire forming, combining precision engineering with advanced technology. This innovative process allows for the creation of complex shapes and designs that were previously difficult or impossible to achieve with traditional methods. By utilizing computer numerical control (CNC), manufacturers can now streamline their production processes, ensuring consistency and accuracy across each piece produced.
What Makes CNC Tube Forming Unique
What sets CNC tube forming apart is its ability to automate intricate bending and shaping tasks that require high levels of precision. Unlike conventional methods where human error can creep in, a wire end forming machine equipped with CNC technology operates based on programmed specifications, reducing variability significantly. This unique capability not only enhances product quality but also minimizes waste, making it an eco-friendlier option for manufacturers focusing on sustainability.
Advantages of CNC Technology in Wire Forming
The advantages of employing CNC technology in wire forming are numerous and compelling. First and foremost, it dramatically increases efficiency by allowing for rapid changes in design without the need for extensive retooling—a boon for companies that require flexibility in production runs. Moreover, the precision offered by CNC systems means that even complex wire bending tasks can be executed flawlessly every time, which is essential when producing components that must fit together perfectly.
Real-World Applications and Success Stories
Real-world applications of CNC tube forming illustrate its transformative impact across various industries. For example, automotive manufacturers have successfully integrated cutting wire machines into their assembly lines to produce lightweight yet durable components quickly and efficiently. Similarly, aerospace companies have reported improved performance metrics after adopting these technologies, showcasing how innovations like the wire end forming machine can lead to substantial gains in productivity and quality.
Spark Fittings and Twisted Wire Solutions
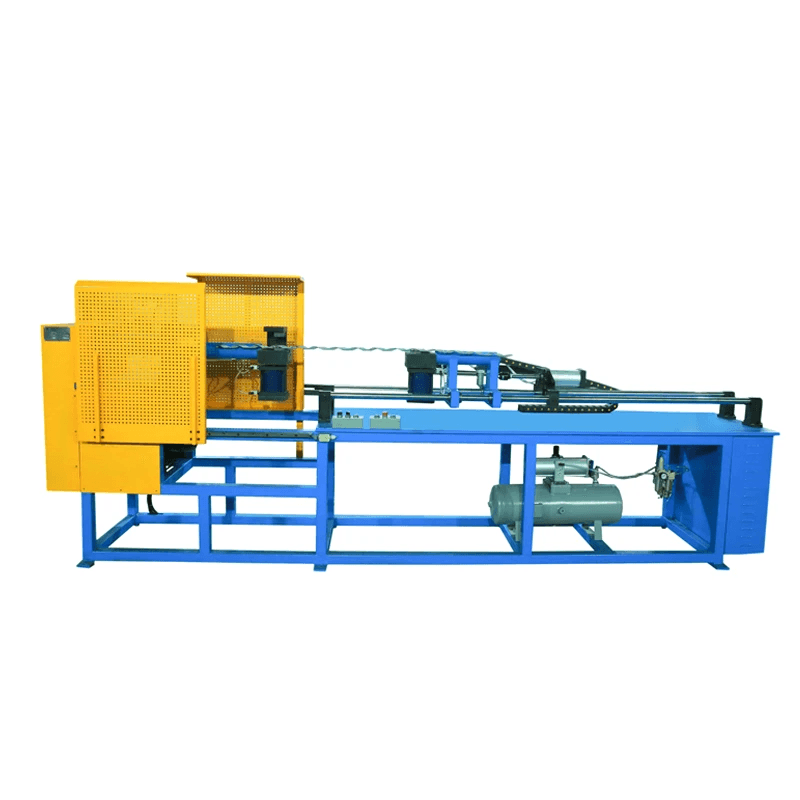
In the world of wire forming, spark fittings and twisted wire solutions play a crucial role in ensuring secure and reliable applications. The integration of twisted wire not only enhances the strength and durability of connections but also allows for greater flexibility in design. By utilizing a wire end forming machine, manufacturers can achieve precise twists that meet stringent industry standards.
Twisted Wire Integration for Secure Applications
Twisted wire has become a go-to solution for applications requiring enhanced security and stability. When using a bending machine alongside twisted wire, the resulting structures offer improved resistance to stress and strain, making them ideal for demanding environments. This integration is particularly beneficial in sectors like automotive and aerospace, where safety is paramount.
Moreover, the use of twisted wires in conjunction with cutting wire machines ensures that each piece is tailored to specific requirements without compromising on quality or strength. The combination of these technologies allows for innovative designs that can withstand harsh conditions while maintaining functionality. With advancements in CNC tube forming, manufacturers can now produce complex shapes that were previously unimaginable.
The Folding Mechanism for Efficient Labeling
Efficiency is key when it comes to labeling products, and the folding mechanism integrated into many modern wire forming machines streamlines this process significantly. By folding wires into predetermined shapes, businesses can create labels quickly without sacrificing accuracy or quality. This feature is especially advantageous when using a cutting wire machine to prepare materials ahead of time.
The ability to fold wires effectively reduces production time while enhancing overall productivity across various industries. Furthermore, this mechanism works seamlessly with bending machines to ensure that each label fits perfectly within its designated space—no more awkwardly shaped tags! As companies strive for efficiency, incorporating advanced folding mechanisms into their processes becomes increasingly vital.
High-Speed Operations and Customizable Options
High-speed operations are essential in today's fast-paced manufacturing landscape, where every second counts toward meeting deadlines and customer demands. With innovations in technology enabling faster processing times on wire end forming machines, businesses can ramp up production without sacrificing quality or precision. Additionally, customizable options allow operators to tailor their setups according to specific project needs.
Using a bending machine equipped with programmable features enhances flexibility even further; operators can switch between tasks seamlessly while maintaining high output levels. This adaptability makes it easier than ever for companies to respond quickly to market changes or unique client requests—an invaluable asset in competitive industries! Ultimately, embracing high-speed operations combined with customizable options positions manufacturers at the forefront of innovation.
Conclusion
In the ever-evolving landscape of manufacturing, wire end forming machines stand out as essential tools for maximizing efficiency and precision. These machines not only streamline the wire forming process but also integrate seamlessly with other equipment like bending machines and cutting wire machines. By investing in advanced technologies, manufacturers can enhance their production capabilities and keep pace with industry demands.
Maximizing Efficiency with Wire End Forming Machines
Wire end forming machines are game changers in the production line, allowing for rapid and accurate shaping of wire ends to meet specific needs. The automation offered by these machines reduces manual labor and minimizes errors, resulting in a more efficient workflow. With features that cater specifically to wire for bending applications, these machines ensure that every piece is crafted to perfection.
Enhancing Production with Advanced Technology
The integration of advanced technology into bending machines and cutting wire machines has revolutionized the way manufacturers operate. CNC tube forming techniques have introduced unparalleled precision in shaping metal tubes and wires, enabling complex designs that were once thought impossible. As industries continue to adopt these sophisticated methods, productivity levels soar, paving the way for innovative products that meet consumer demands.
Future Trends in Wire Forming and Cutting Machines
Looking ahead, we can expect exciting developments in the realm of wire forming and cutting machines driven by technological advancements such as artificial intelligence and smart manufacturing systems. These innovations will likely enhance the capabilities of existing machinery like wire end forming machines, making them even more efficient and user-friendly. As manufacturers embrace these trends, they will not only improve their processes but also set new standards for quality in the industry.