Introduction
In the world of manufacturing and engineering, understanding formed wire is essential for a variety of applications. Formed wire encompasses a range of products created through the intricate process known as wire forming, which transforms raw materials into specialized shapes and configurations. Whether you're asking What is wire forming? or delving into the specifics of how copper wire is formed, grasping these concepts can significantly impact your project's success.
Understanding Formed Wire Basics
Formed wire refers to any metal wire that has been shaped or altered to meet specific requirements for various applications. This includes custom wire forming techniques that allow manufacturers to create unique designs tailored to client specifications, such as wire fasteners used in construction or electrical projects. By understanding the fundamentals of formed wire, you can better appreciate its versatility in diverse industries.
The Importance of Quality Wire Forming
Quality in wire forming cannot be overstated; it directly affects the durability and functionality of the final product. Poorly formed wires can lead to failures in critical applications, resulting in costly downtime and repairs. Therefore, when exploring how copper wire is formed or considering what are the two basic types of wire—solid and stranded—it's crucial to prioritize quality at every stage of production.
Choosing the Right Manufacturer
Selecting a reliable manufacturer is vital when seeking a formed wire dead end manufacturer and supplier for your projects. Not all manufacturers are created equal; evaluating their credentials and experience ensures that you receive high-quality products that meet your specifications. Companies like Spark Fittings stand out due to their expertise in producing equipment for preformed armor rods and cable accessories, guaranteeing that you receive top-notch formed wires tailored for your needs.
What is Wire Forming?
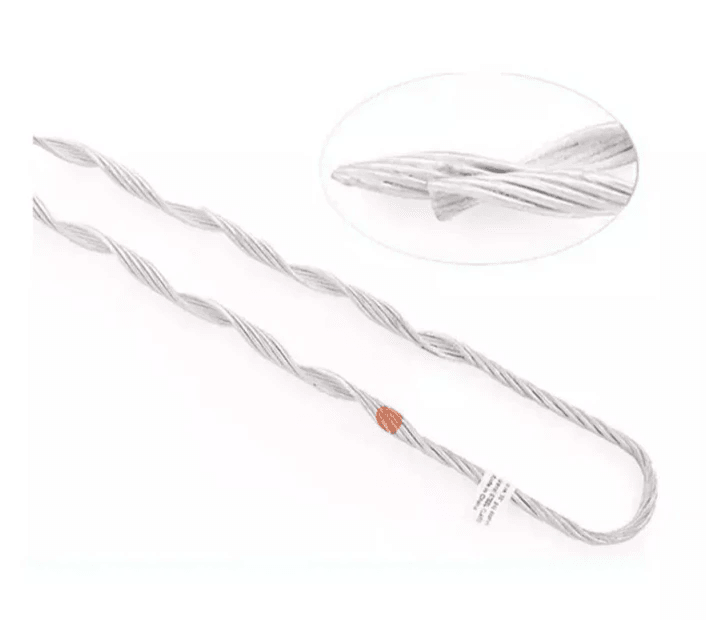
Wire forming is a fascinating process that transforms raw wire into complex shapes and structures tailored for specific applications. This technique plays a crucial role in various industries, from automotive to aerospace, ensuring that components meet precise specifications. Understanding wire forming is essential for anyone looking to utilize formed wire effectively in their projects.
Definition and Process of Wire Forming
Wire forming refers to the method of bending, twisting, and shaping wire into desired configurations using specialized machinery or manual techniques. The process begins with selecting the appropriate type of wire—often copper or steel—followed by feeding it through machines that apply controlled pressure and heat to achieve the desired shape. This results in custom wire forming products like brackets, clips, and fasteners that are integral to many applications.
The beauty of wire forming lies in its versatility; it can produce both simple shapes and intricate designs with precision. Whether you're asking What is wire forming? for a project or exploring how it's done, it's important to note that the outcome relies heavily on the techniques employed during production. Manufacturers often utilize advanced technologies such as CNC machines to ensure accuracy and efficiency in creating formed wire products.
Applications in Various Industries
Formed wire finds its way into numerous sectors, demonstrating its adaptability across different fields. In the automotive industry, custom wire forming is used for components like springs and brackets essential for vehicle assembly. Similarly, aerospace applications require high-strength formed wires for safety-critical systems where reliability cannot be compromised.
Beyond transportation, formed wires are prevalent in construction as well; they serve as critical elements in structural frameworks or electrical installations where durability is key. Additionally, many household items—from kitchen utensils to furniture—utilize custom wire forms as they provide strength without adding excessive weight. The broad range of applications showcases why understanding how formed wires are created can be beneficial.
Benefits of Custom Wire Forming
Custom wire forming offers several advantages that make it an appealing choice for manufacturers and engineers alike. One primary benefit is the ability to create tailored solutions that meet specific design requirements; this ensures functionality while adhering closely to project specifications. Moreover, using custom processes can lead to cost savings by minimizing waste material during production—a win-win situation!
Another significant advantage lies in the enhanced durability provided by formed wires compared to traditional solid alternatives; this makes them ideal for demanding environments where performance matters most. Customization also allows businesses to innovate more freely since they can design unique components without being restricted by pre-existing products on the market.
Lastly, partnering with a reputable formed wire dead end manufacturer and supplier like Spark Fittings guarantees access to high-quality materials and expert craftsmanship essential for producing reliable components across various industries—from electrified railways to energy transmission systems.
How is Copper Wire Formed?
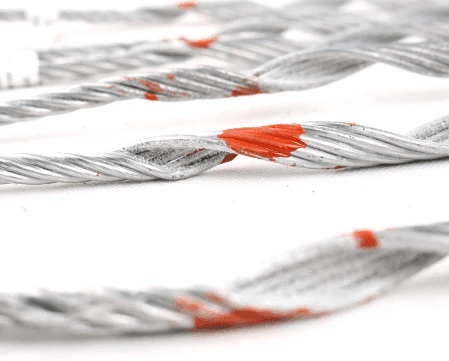
Copper wire forming is a fascinating process that combines artistry and engineering to create essential components for various applications. Understanding how copper wire is formed can help you appreciate its role in everything from electrical systems to structural projects. In this section, we will explore the manufacturing process, advantages of copper, and key techniques involved in producing high-quality formed wire.
The Manufacturing Process Explained
The manufacturing process of copper wire begins with the extraction of pure copper from its ore, followed by refining it to achieve the desired conductivity and malleability. Once refined, the copper undergoes drawing—a technique where it is pulled through progressively smaller dies to reduce its diameter while increasing its length. This method not only shapes the wire but also enhances its strength and flexibility, making it suitable for various applications in custom wire forming.
After drawing, additional processes such as annealing may be employed to relieve stress in the metal and improve ductility. The final stages involve cutting the wire into specific lengths or coiling it for easy handling. Understanding how copper wire is formed provides insight into why it's favored for applications requiring high conductivity and durability.
Advantages of Copper in Wire Forming
Copper stands out as a premier choice in wire forming due to its excellent electrical conductivity—second only to silver—making it ideal for electrical applications. Additionally, copper's resistance to corrosion ensures longevity and reliability when used in outdoor or harsh environments; this quality makes it indispensable in industries ranging from telecommunications to construction. Moreover, thanks to its malleability and ductility, custom wire forming with copper allows manufacturers to create intricate designs without compromising strength.
Another advantage lies in copper's thermal conductivity; wires made from this metal can efficiently dissipate heat generated during electrical transmission. This characteristic reduces risks associated with overheating and improves overall system performance—critical factors when considering what are the two basic types of wire? Copper excels here as a material choice compared to alternatives like aluminum or steel.
Key Techniques in Copper Wire Production
Several key techniques are employed during the production of formed wire that ensure high-quality outcomes tailored for specific needs. One such technique is extrusion, where heated billets of copper are forced through a die under pressure—this method produces complex shapes that are often required for specialized applications like cable fasteners or connectors used extensively across industries.
Another important technique involves stranding—the process where multiple strands of thinner wires are twisted together to form a single larger conductor known as stranding wire; this enhances flexibility while maintaining strength—a crucial aspect when asking what is the meaning of stranding wire? Stranded wires are particularly advantageous for installations requiring movement or bending without breaking.
Finally, quality control plays an essential role throughout every stage of production; rigorous testing ensures each batch meets industry standards before reaching customers like those seeking a formed wire dead end manufacturer and supplier capable of delivering reliable products consistently.
What is the Meaning of Stranding Wire?
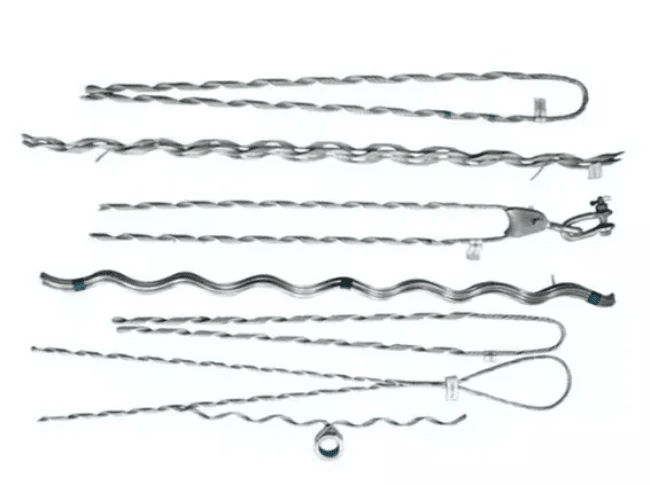
Stranding wire is a specific type of wire that consists of multiple smaller wires twisted together to form a single, cohesive unit. This method enhances flexibility and conductivity, making stranding wire an essential component in various applications. Understanding its characteristics can help you choose the right formed wire for your projects.
Definition and Uses of Stranding Wire
Stranding wire refers to a configuration where several individual wires are braided or twisted together, creating a more flexible and robust product compared to solid wire. This design allows for easier handling and installation, particularly in tight spaces or complex configurations. Common uses include electrical wiring, cable assemblies, and various forms of custom wire forming where flexibility is paramount.
Difference Between Stranding and Solid Wire
The primary distinction between stranding and solid wire lies in their construction; stranding involves multiple wires twisted together whereas solid wire consists of a single piece of metal. This difference results in varied mechanical properties: stranding offers greater flexibility while solid wire provides higher tensile strength. When choosing between these two types, consider factors such as application requirements, environmental conditions, and desired performance outcomes.
Applications in Electrical and Structural Projects
Stranding wire finds extensive applications across electrical and structural projects due to its versatility. In electrical systems, it is commonly used for power transmission lines, allowing for efficient energy transfer without sacrificing flexibility or durability. Additionally, it plays a crucial role in structural applications like bridges or buildings where high-strength cables are required; this ensures safety while maintaining the integrity of the overall design.
Understanding Wire Types
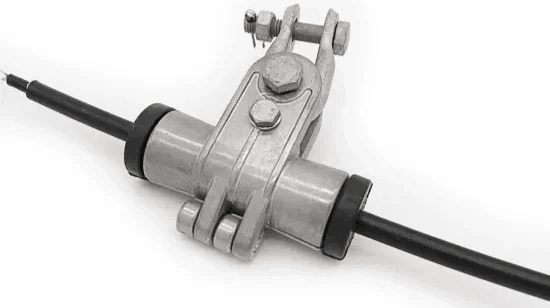
When it comes to wire, understanding the different types available is crucial for any project involving formed wire, custom wire forming, or wire fasteners. The choice of wire can significantly impact the durability and effectiveness of your applications. Therefore, knowing what are the two basic types of wire is essential for making informed decisions.
The Two Basic Types of Wire
The two fundamental categories of wire are solid wire and stranded wire. Solid wire consists of a single conductor that provides excellent conductivity and strength but lacks flexibility. On the other hand, stranded wire is made up of multiple smaller wires twisted together, offering greater flexibility and ease in installation, which is particularly beneficial in environments requiring movement or vibration.
Characteristics of Each Type
Solid wire boasts a straightforward construction that makes it ideal for applications where rigidity and minimal movement are required—think electrical connections or permanent installations. Its smooth surface also allows for efficient current flow, making it a popular choice in many electrical projects. Conversely, stranded wire excels in situations demanding flexibility; its construction allows it to bend without breaking, making it perfect for dynamic applications like robotics or automotive wiring systems.
Selecting the Right Wire for Your Needs
Choosing between solid and stranded wires depends on your specific requirements; consider factors such as flexibility, installation space, and electrical load when deciding. If you're working on a project that involves tight spaces or requires frequent movement—like cable assemblies—a custom approach with stranded wires may be more suitable. For applications needing robust connections with limited movement—such as those using formed wire dead end manufacturer and supplier products—solid wires might be your best bet.
Importance of Quality Suppliers
When it comes to formed wire, the quality of your supplier can make all the difference in your project’s success. A reliable manufacturer ensures that your custom wire forming needs are met with precision and care, resulting in durable wire fasteners that perform as expected. Finding a formed wire dead end manufacturer and supplier who prioritizes quality can save you time, money, and headaches down the road.
Finding a Formed Wire Dead End Manufacturer and Supplier
The search for a reputable formed wire dead end manufacturer and supplier begins with understanding your specific requirements. You need to consider factors such as the types of wire you need, whether it's solid or stranding wire, and how they will be applied in your projects. Researching potential suppliers online, reading reviews, and asking for recommendations from industry peers can help you compile a list of candidates.
Once you've narrowed down your options, it's essential to evaluate their capabilities in custom wire forming. Look for manufacturers who offer a range of services tailored to various applications across different industries. This versatility is crucial because it indicates that they are equipped to handle unique specifications while maintaining high-quality standards.
Evaluating Manufacturer Credentials
Evaluating manufacturer credentials is vital when choosing a partner for your formed wire needs. Start by checking if they have relevant certifications that affirm their commitment to quality control processes in manufacturing—this is particularly important when considering how copper wire is formed or what techniques are used in production. Additionally, inquire about their experience within the industry; seasoned manufacturers often have valuable insights into best practices.
Don't forget about customer service! A good supplier should be responsive and willing to address any questions or concerns about their products or processes—especially regarding complex topics like what is wire forming? If they can explain things clearly, it shows confidence in their expertise. Furthermore, ask for samples or references from previous clients; this will give you an idea of their reliability and product quality.
Why Spark Fittings Stands Out
When looking at potential suppliers for formed wire products, Spark Fittings consistently stands out as a leading choice within the industry. Specializing in manufacturing equipment for preformed armor rods, tension clamps, and cable accessories for ADSS and OPGW applications means they have honed their processes around producing high-quality items tailored specifically for electrical transmission systems. This focus on excellence ensures that customers receive custom solutions aligned with their exact needs.
Spark Fittings not only excels at providing top-notch products but also offers exceptional customer support throughout every stage of your project—from initial inquiry through delivery of finished goods. Their expertise extends beyond just what is the meaning of stranding wire; they understand how different types interact within various applications seamlessly. If you're seeking a trusted partner who prioritizes quality manufacturing while delivering superior service every step of the way, look no further than Spark Fittings.
Conclusion
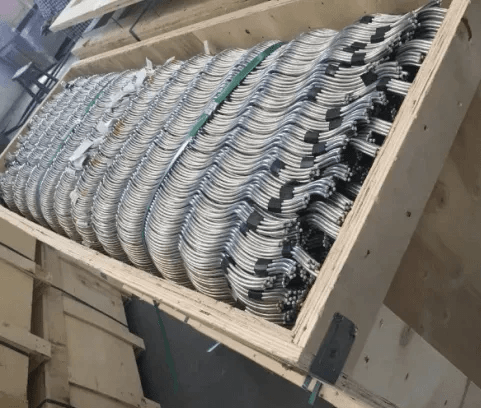
In the world of formed wire, understanding the nuances of wire forming processes and materials is crucial for making informed decisions. Whether you're exploring custom wire forming or seeking reliable wire fasteners, the right choices can significantly impact your projects. By grasping concepts like how copper wire is formed and what stranding wire means, you equip yourself with knowledge that enhances both efficiency and quality.
Key Takeaways on Formed Wire Selection
When selecting formed wire, it’s essential to consider the specific applications and industry standards that apply to your project. Understanding what is wire forming? provides a solid foundation for evaluating different types of wires available in the market. Additionally, remember that there are two basic types of wire: solid and stranded, each offering unique benefits tailored to various needs.
Best Practices for Wire Forming Projects
To ensure success in your custom wire forming projects, always prioritize quality suppliers who understand the intricacies involved in producing formed wires. Establishing a partnership with a reputable formed wire dead end manufacturer and supplier can streamline production while maintaining high standards. Moreover, leveraging advanced techniques in copper wire production will enhance durability and performance across all applications.
Final Thoughts on Working with Manufacturers
Collaborating with manufacturers like Spark Fittings can elevate your projects through their specialized equipment designed for preformed armor rods and tension clamps. Their expertise in manufacturing high-quality products ensures that your formed wires meet rigorous industry demands without compromising quality or performance. Ultimately, investing time in selecting the right manufacturer will yield significant dividends in terms of reliability and long-term satisfaction.