Introduction
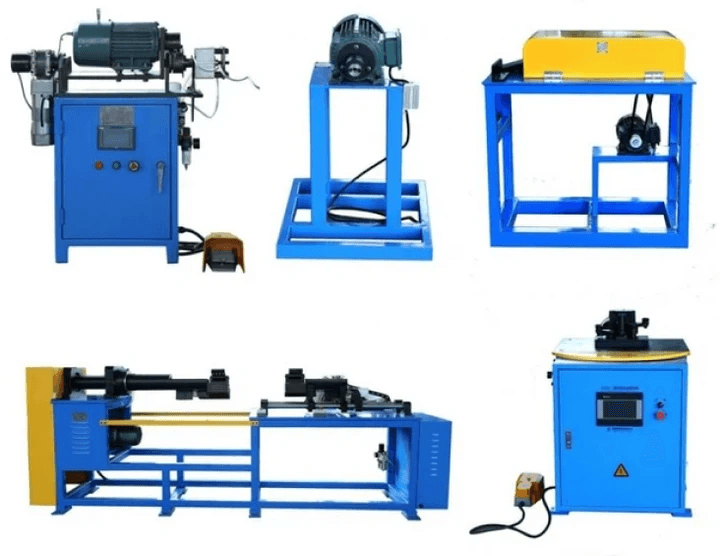
In the world of manufacturing and metal fabrication, wire bending machines play a pivotal role in shaping and forming materials with precision. These machines are essential for producing intricate designs, whether in automotive components or decorative items. Understanding the nuances of wire bending machines can significantly enhance productivity and quality in various industries.
Understanding Wire Bending Machines
Wire bending machines are specialized tools designed to manipulate wire into specific shapes and forms, catering to a wide array of applications. From simple bends to complex configurations, these machines can handle different types of wires, making them versatile assets on the production floor. CNC wire bending machines take this versatility a step further by offering automated processes that ensure consistent results with minimal human intervention.
Importance of Choosing the Right Machine
Selecting the right wire bender is crucial for optimizing operational efficiency and achieving desired outcomes in any project. The wrong machine can lead to increased waste, slower production times, and ultimately higher costs—nobody wants that! By understanding your specific needs and comparing various options like CNC coiling and bending machines, you can make an informed investment that pays dividends in quality and speed.
Types of Wire Bending Machines Available
When it comes to wire bending technology, there’s no shortage of options available on the market today. You’ll find everything from manual models for smaller operations to advanced CNC wire bending machines capable of handling large-scale production with ease. Each type has its unique features tailored for different applications, ensuring there's a perfect fit for every business need.
Key Features of Wire Bending Machines
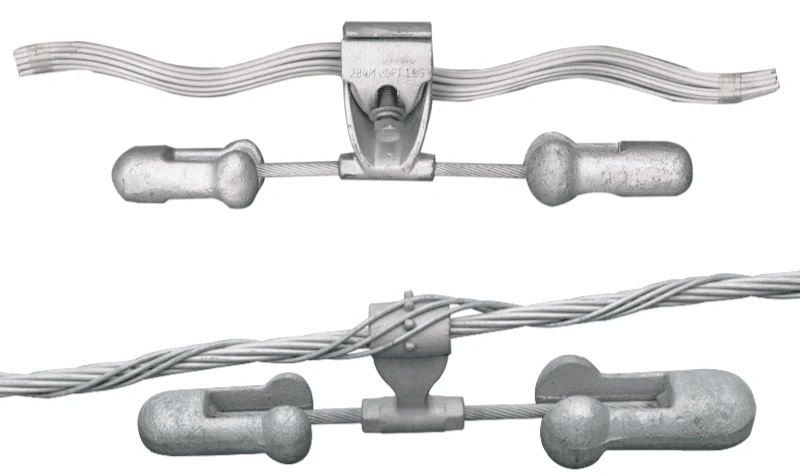
Precision and Accuracy in Bending
Precision is paramount when it comes to wire bending machines, especially for industries requiring tight tolerances. CNC wire bending machines are designed to deliver exceptional accuracy, ensuring that every bend is consistent and meets exact specifications. This level of precision minimizes waste and rework, ultimately saving both time and money in production.
Accurate bends are not just a luxury; they are a necessity in applications such as automotive parts or medical devices where even a slight deviation can lead to significant issues. With advanced technology embedded in modern CNC coiling and bending machines, users can expect flawless performance with each operation. Investing in a high-quality wire bender guarantees that your products will have the reliability and durability needed for various applications.
Speed and Efficiency in Operations
In today’s fast-paced manufacturing environment, speed is often as important as precision. Wire bending machines equipped with CNC technology can operate at remarkable speeds without sacrificing quality, allowing businesses to ramp up production efficiently. The ability to process multiple bends quickly means you can fulfill larger orders without delays.
Moreover, efficient operations translate into lower operational costs over time. By choosing a high-speed wire bending machine, manufacturers can optimize their workflows while maintaining high standards of output quality. This balance between speed and efficiency not only enhances productivity but also gives companies a competitive edge in the market.
Customization Options for Different Tasks
Every project has its unique requirements, which is why customization options are vital when selecting a wire bending machine. Many modern CNC coiling and bending machines offer versatile programming capabilities that allow operators to tailor bends according to specific project needs or materials used. This flexibility ensures that no matter how complex the task may be, your wire bender can handle it with ease.
Additionally, customization extends beyond programming; many machines come equipped with interchangeable tooling options for various tasks or materials like stainless steel or aluminum wires. This adaptability makes it easy for manufacturers to pivot between different projects without needing extensive downtime or additional equipment investments. In short, having a customizable wire bending machine opens up new possibilities for innovation while maximizing resource utilization.
Comparing CNC Wire Bending Machines
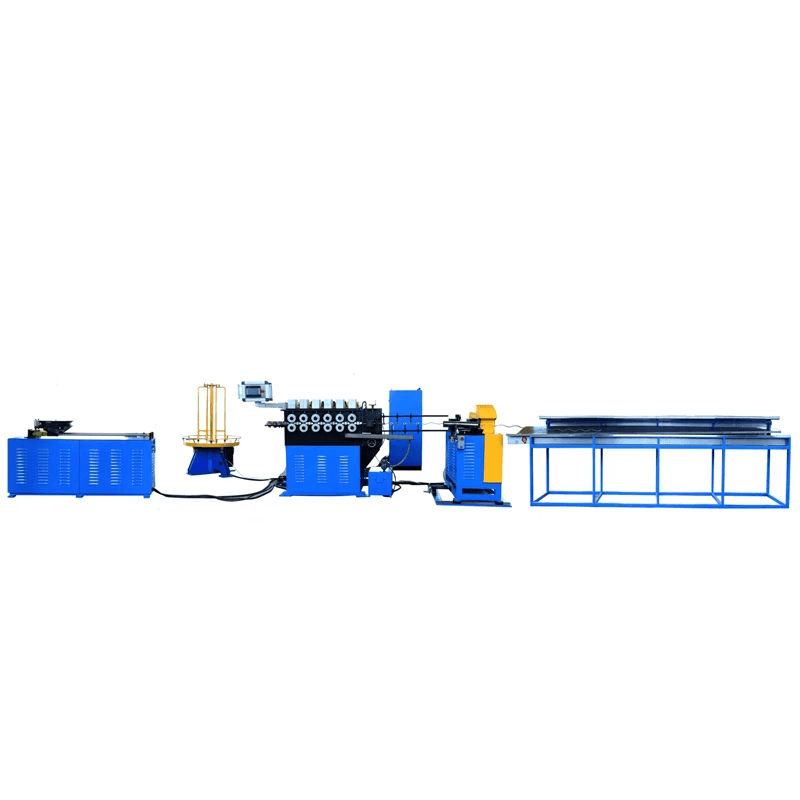
Advantages of CNC Technology
CNC technology offers remarkable advantages for wire bending machines that traditional models simply can’t compete with. First and foremost, the precision of CNC coiling and bending machines ensures that each bend is executed flawlessly, reducing waste and enhancing overall product quality. Additionally, these machines can handle complex designs with ease, allowing for greater creativity in projects while maintaining speed and efficiency.
Moreover, the automation aspect of CNC wire bending machines minimizes human error and streamlines production processes significantly. Operators can program intricate tasks into the machine with just a few clicks, saving time on setup and execution. This level of efficiency not only increases output but also allows businesses to take on more diverse projects without needing extensive manual labor.
Lastly, modern CNC wire benders often come equipped with user-friendly interfaces that simplify operation further. With intuitive controls and programming capabilities, even those new to wire bending can quickly learn how to use these advanced tools effectively. In short, investing in a CNC wire bending machine means investing in improved accuracy, versatility, and operational efficiency.
Top Brands in CNC Wire Bending Machines
When considering a new wire bender for your operations, knowing which brands stand out in the market is crucial for informed decision-making. Some leading names include WAFIOS, BLM Group, and KUKA; each renowned for their innovative approaches to CNC technology in wire bending machines. These brands consistently deliver high-quality products that cater to various industrial needs.
WAFIOS is particularly noted for its robust construction and reliability; their line of CNC coiling and bending machines is well-regarded across multiple sectors including automotive and aerospace industries. Meanwhile, BLM Group offers flexibility with their advanced software solutions that allow users to create complex geometries effortlessly—ideal if you’re tackling intricate designs or custom orders.
KUKA also deserves mention due to its focus on automation; their systems integrate seamlessly into existing workflows while providing exceptional performance metrics. Investing in a top-tier brand not only guarantees superior machine quality but often includes access to ongoing support services ensuring your operations run smoothly long-term.
Cost Considerations and Budgeting
Budgeting for a new wire bending machine requires careful consideration beyond just the initial purchase price; understanding total cost ownership is essential for making sound financial decisions. While upfront costs may vary significantly based on brand reputation and features offered by different models of CNC wire bending machines, it's vital to factor in maintenance expenses as well as potential downtime during repairs or replacements.
Additionally, consider how much operational efficiency you expect from your investment: higher-quality models may come with a steeper price tag but could lead to substantial savings over time through reduced waste or increased throughput rates within your production line. Therefore analyzing your specific production requirements will help determine what level of investment aligns best with your business goals.
Finally—don’t forget about financing options! Many manufacturers offer leasing arrangements or financing plans which can ease cash flow concerns while still allowing you access to cutting-edge technology like modern wire benders tailored specifically for today’s manufacturing challenges.
Applications of Wire Bending Machines
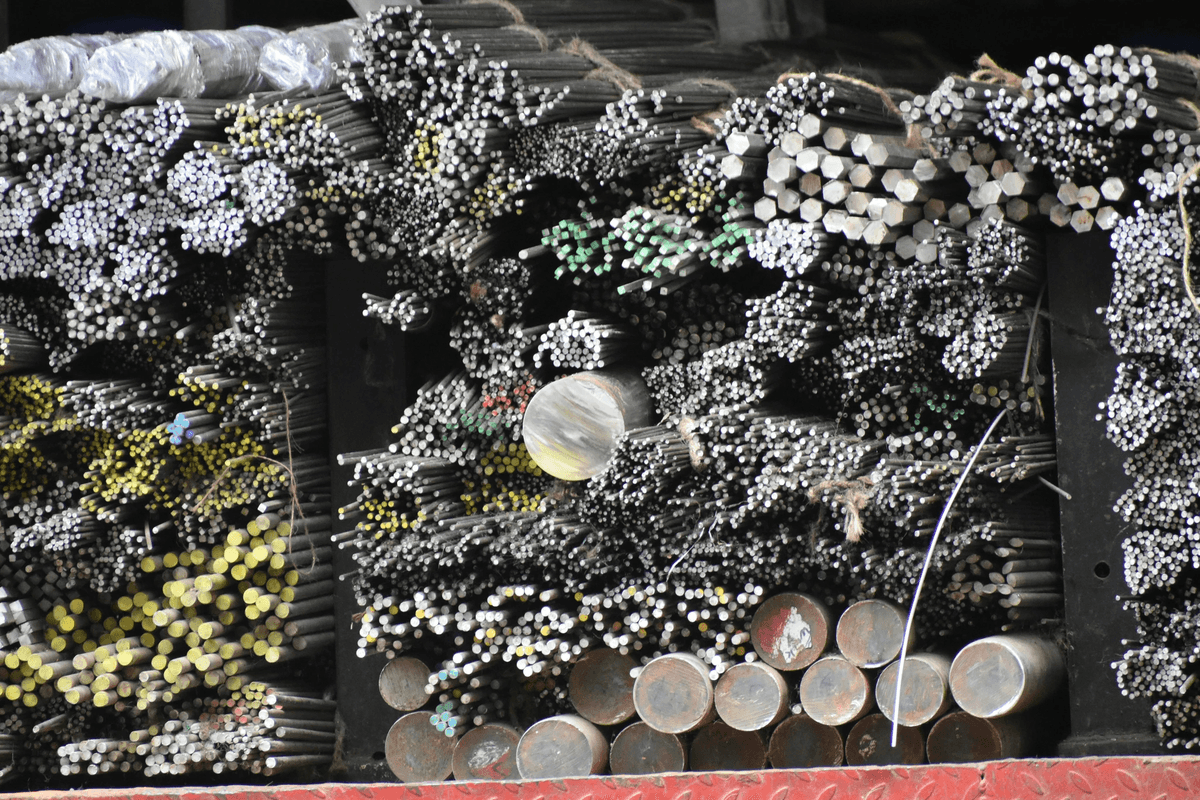
Wire bending machines have become indispensable tools across various industries, revolutionizing how products are manufactured. From automotive to construction, these machines streamline processes and enhance productivity. Understanding the wide-ranging applications can help businesses leverage the capabilities of CNC wire bending machines effectively.
Industries That Benefit from Wire Benders
Several industries find immense value in wire bending technology, with each sector utilizing these machines for specific needs. The automotive industry relies heavily on wire benders for creating components like brackets and supports that require precision and durability. Additionally, the furniture industry uses wire bending machines to produce intricate designs in metal furniture, while the electronics sector benefits from CNC coiling and bending machines for creating complex wiring harnesses.
Moreover, the construction industry also sees significant advantages from using a wire bender to fabricate rebar ties and other structural elements efficiently. These diverse applications highlight how a well-chosen wire bending machine can cater to various production requirements across multiple sectors.
Common Projects Utilizing Wire Bending Technology
Wire bending technology is employed in numerous projects that necessitate intricate shapes and forms made from metal wires. One common project involves manufacturing custom metal frames for various appliances or machinery, where precision is paramount. Another frequent application includes producing decorative items such as garden trellises or artistic sculptures that require unique designs achievable only through advanced CNC wire bending machines.
Additionally, many manufacturers use these machines to create safety barriers or fencing systems tailored to specific dimensions and configurations needed on job sites. The versatility of a quality wire bending machine allows businesses to tackle an array of projects efficiently while maintaining high standards of quality.
Case Studies Showcasing Successful Use
Examining real-world examples reveals just how impactful wire bending technology can be in enhancing operational efficiency and product quality. For instance, a leading automotive manufacturer integrated CNC coiling and bending machines into their assembly line, reducing production time by 30% while improving accuracy in component fabrication significantly. This move not only led to cost savings but also boosted overall output without compromising on quality.
Another case study involved a boutique furniture maker that utilized advanced wire benders to create custom pieces that stood out in a competitive market. By leveraging innovative designs facilitated by their new equipment, they increased sales by 25% within six months of implementation—demonstrating how investing in the right equipment pays off handsomely.
In summary, whether it's through improved precision in automotive parts or unique decorative elements in furniture design, the applications of wire bending machines are vast and varied—each showcasing the transformative potential of this technology across different sectors.
Selecting the Right Wire Bender for Your Needs
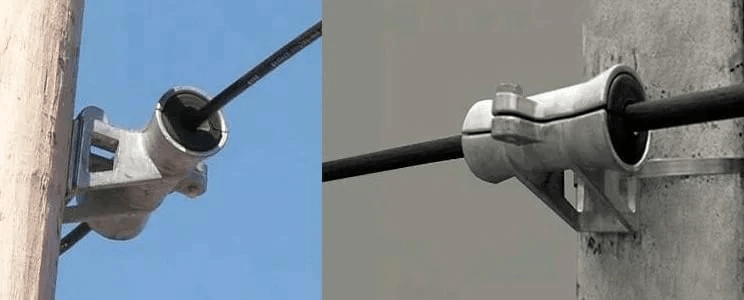
Choosing the right wire bending machine can feel like trying to find a needle in a haystack, especially with so many options on the market. Whether you're eyeing CNC wire bending machines or traditional models, understanding your specific production needs is crucial. This section will guide you through assessing your requirements, considering size and capacity, and ensuring you have reliable maintenance support.
Assessing Your Production Requirements
Before diving into the world of wire bending machines, take a moment to evaluate what you really need. Are you producing small batches of intricate designs or large volumes of standard parts? Knowing your production requirements will help you determine whether a CNC coiling and bending machine or a simpler wire bender is more suitable for your operations.
Another factor to consider is the complexity of your projects; some applications may require advanced features that only certain models can provide. If precision and customization are key for your tasks, investing in high-quality CNC wire bending machines might be worth it in the long run. Ultimately, aligning your production goals with the capabilities of different wire bending machines will set you on the path to success.
Size and Capacity Considerations
Once you've assessed your production needs, it's time to think about size and capacity when selecting a wire bending machine. The dimensions of your workspace will play a significant role in determining which model fits best without cramping your style—or workflow! Additionally, consider how much volume you'll be producing; larger projects may necessitate more robust machines capable of handling greater loads.
Capacity isn't just about physical size; it also refers to how efficiently a machine can operate under pressure. CNC coiling and bending machines often have higher throughput rates compared to manual models, making them ideal for businesses aiming for efficiency without sacrificing quality. Balancing these factors ensures that you'll choose a wire bender that complements both space constraints and productivity goals.
Maintenance and Support Services
Investing in a wire bending machine is only part of the equation; ongoing maintenance and support services are essential for keeping operations running smoothly. Before making any decisions, inquire about warranty options as well as available service contracts from manufacturers or suppliers of CNC wire bending machines. A reliable support system can save you from costly downtime when issues arise unexpectedly.
Moreover, consider whether spare parts are readily available for the specific model you're interested in; this can significantly affect repair times should something go awry down the line. Regular maintenance checks should also be part of your plan—after all, an ounce of prevention is worth a pound of cure! By prioritizing maintenance and support services along with selecting an appropriate wire bender, you'll ensure longevity and reliability in your investment.
Innovative Features of Modern Wire Bending Machines
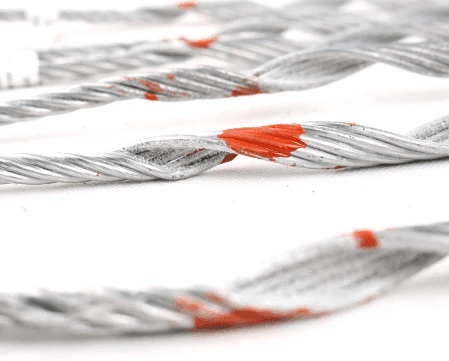
In the fast-paced world of manufacturing, the wire bending machine has evolved significantly, embracing innovative features that enhance productivity and precision. Among these advancements, automation and smart technology stand out as game-changers. By integrating these technologies into CNC wire bending machines, manufacturers can achieve higher efficiency and reduce human error in the bending process.
Automation and Smart Technology
Automation is revolutionizing how we approach wire bending tasks. With CNC coiling and bending machines equipped with intelligent systems, operators can set parameters for various projects with just a few clicks. This not only streamlines operations but also allows for real-time adjustments based on production needs, ensuring that each wire bender operates at peak performance.
Smart technology also plays a crucial role in predictive maintenance for wire bending machines. By utilizing sensors and data analytics, manufacturers can monitor machine health continuously, predicting potential issues before they become costly breakdowns. This proactive approach minimizes downtime and maximizes productivity—essential elements in today’s competitive market.
The Role of Touchscreen Controls
Gone are the days of complicated dials and buttons; modern wire bending machines feature intuitive touchscreen controls that simplify operation significantly. These user-friendly interfaces allow operators to easily navigate through settings, select programs, or adjust parameters without needing extensive training or technical know-how. The combination of visual feedback and straightforward commands makes it easier to manipulate complex designs on CNC wire bending machines.
Moreover, touchscreen controls facilitate quick programming changes between projects—a vital feature when dealing with custom orders or varying specifications. Operators can save time by accessing pre-set configurations for different tasks at their fingertips instead of manually reprogramming each detail on traditional models. This efficiency ultimately leads to faster turnaround times without sacrificing quality.
Spark Fittings' Twisted Wire Folding Labeling Machine
One standout example in the realm of modern wire bending technology is Spark Fittings' twisted wire folding labeling machine—a true innovation in this field! This specialized equipment not only bends wires but also integrates labeling capabilities seamlessly into the production line. It showcases how advanced features are being combined to create multifunctional solutions that cater to diverse manufacturing needs.
The twisted wire folding aspect allows for intricate designs while maintaining structural integrity—perfect for industries requiring precision components such as automotive or aerospace sectors where every detail matters immensely! Plus, its ability to label during the process eliminates additional steps post-bending; saving time and reducing labor costs associated with manual labeling efforts typically required after production runs.
Conclusion
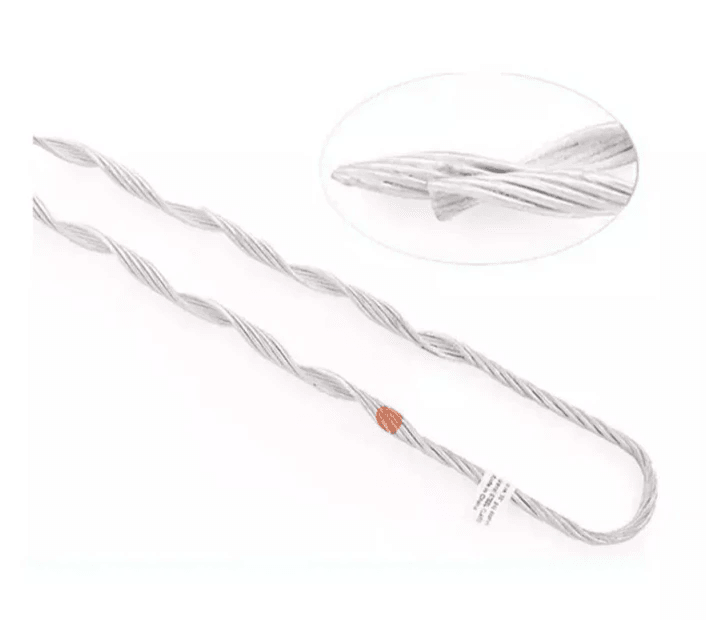
Making an Informed Decision on Investment
Investing in a wire bending machine is not just about choosing the most advanced technology; it's about finding the right fit for your production requirements. Consider factors such as the volume of work, types of materials used, and desired output quality when selecting a Wire Bender. A well-researched decision can lead to increased efficiency and reduced operational costs in the long run.
The Future of Wire Bending Technology
The future of wire bending technology looks promising with advancements in automation and smart features that enhance productivity and precision. CNC coiling and bending machines are leading this charge, integrating AI to optimize operations further. As these technologies evolve, we can expect even greater capabilities that will redefine how industries approach wire fabrication.
Final Tips for Choosing Your Wire Bending Machine
When choosing your wire bending machine, prioritize understanding your unique production needs before diving into options. Look for CNC wire bending machines that offer versatility in design while ensuring ease of use with intuitive controls. Don’t forget to consider after-sales support; a reliable maintenance plan can save you from unexpected downtimes.