Introduction
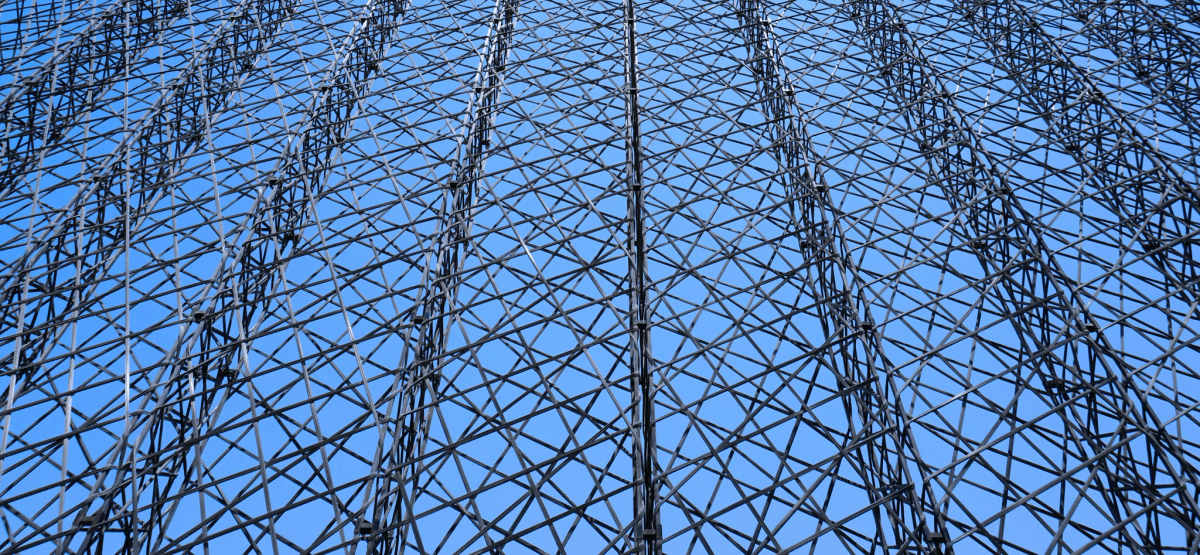
In the world of manufacturing, precision wire forms play a crucial role in various applications, from automotive to aerospace. These specialized components are crafted to meet specific requirements, ensuring optimal performance in their designated roles. Understanding the intricacies of custom wire forming and the contributions of wire form manufacturers is essential for anyone looking to leverage these versatile products.
Understanding Precision Wire Forms
Precision wire forms are tailored metal components made from high-quality wire, designed for specific functions across multiple industries. They can take on various shapes and sizes, depending on their intended use, making them highly versatile in applications such as electronics and construction. By exploring how to form metal wire into intricate designs, we can appreciate the skill and technology involved in creating these essential products.
The Role of Wire Form Manufacturers
Wire form manufacturers serve as the backbone of this industry, providing expertise in custom wire forming that meets stringent quality standards. These manufacturers utilize advanced techniques and equipment to produce precision wire forms that cater to diverse client needs while ensuring durability and reliability. Their role extends beyond mere production; they also collaborate with clients to develop tailored solutions that enhance product functionality.
Benefits of Custom Wire Forming
Custom wire forming offers numerous advantages over off-the-shelf alternatives, allowing businesses to optimize their designs for specific applications. By working closely with a skilled wire form manufacturer, companies can achieve precise dimensions and specifications that enhance performance and reduce waste. Additionally, utilizing custom wire fasteners ensures compatibility with existing systems while providing improved strength and longevity—key factors for any successful project.
What Are Precision Wire Forms?
Precision wire forms are essential components in various industries, designed to meet specific requirements for functionality and performance. These wireforms can take on numerous shapes and sizes, serving diverse applications ranging from automotive parts to electronic devices. Understanding the intricacies of these forms helps businesses choose the right wire form manufacturer for their needs.
Defining Wire Forms and Their Uses
Wire forms are created by bending and shaping metal wire into desired configurations, often tailored for specific functions. They can be found in everyday items such as hangers, clips, or brackets, but their applications extend far beyond that into critical areas like aerospace and medical devices. The versatility of precision wire forms makes them invaluable; they provide unique solutions where standard components may fall short.
Overview of Types of Wire Forms
Common categories include hooks, brackets, springs, and custom wire fasteners that cater to specialized needs across different sectors. Understanding these types allows companies to select the most suitable precision wire for their particular project requirements.
Importance of Customization in Wire Forms
Customization is key when it comes to precision wire forms; it ensures that each product meets specific criteria regarding size, shape, and function. A skilled wire form manufacturer can create bespoke designs that align perfectly with client specifications while optimizing performance and efficiency. Custom wire forming not only enhances product quality but also contributes significantly to overall project success by providing tailored solutions.
The Process of Custom Wire Forming
Custom wire forming is an intricate process that transforms raw materials into high-quality precision wire forms tailored for various applications. Understanding the steps involved, the techniques employed by wire form manufacturers, and how to efficiently form metal wire is essential for anyone looking to delve into this fascinating field. Let’s break it down.
Steps Involved in Wire Forming
The journey of custom wire forming begins with selecting the right type of wire based on the specific requirements of the project. Once a suitable material is chosen, it undergoes a series of processes including cutting, bending, and shaping to create precise wireforms that meet stringent specifications. After initial shaping, these forms are often subjected to finishing processes such as polishing or coating to enhance durability and appearance.
Next comes the critical phase of quality assurance where each piece is meticulously inspected for defects or inconsistencies. This step ensures that only top-notch products make it out of the factory doors—a hallmark of reputable wire form manufacturers. Finally, once everything checks out, these custom wire fasteners are packaged and prepared for delivery, ready to be utilized in various industries.
Techniques for Precision Wire Manufacturing
Wire form manufacturers employ a variety of advanced techniques to ensure precision in their products. Some popular methods include CNC (Computer Numerical Control) machining and laser cutting which allow for intricate designs with minimal human error. Additionally, processes like coiling and bending use specialized machinery that can replicate complex shapes consistently across large production runs.
Another noteworthy technique involves spring-making machinery which produces high-tension components used extensively in automotive applications among others. These techniques not only improve efficiency but also maintain consistency across batches—essential for industries relying on precision wire forms for safety-critical applications. Moreover, combining traditional craftsmanship with modern technology enables manufacturers to push boundaries further than ever before.
How to Form Metal Wire Efficiently
When considering how to form metal wire efficiently, one must look at both equipment capabilities and process optimization strategies employed by leading manufacturers in custom wire forming & wire fasteners production. Utilizing automated systems can significantly reduce labor costs while increasing output rates—allowing companies to meet demand without compromising quality standards associated with precision wires.
Furthermore, adopting lean manufacturing principles helps streamline operations by minimizing waste at every stage—from raw material handling through production all the way to packaging and shipping processes. Investing in training employees on best practices also plays a crucial role; skilled workers can identify bottlenecks early on and implement solutions swiftly.
In conclusion, mastering the art of forming metal wires efficiently not only enhances productivity but also solidifies a manufacturer’s reputation within competitive markets where quality cannot be overlooked.
Quality Standards in Wire Form Manufacturing
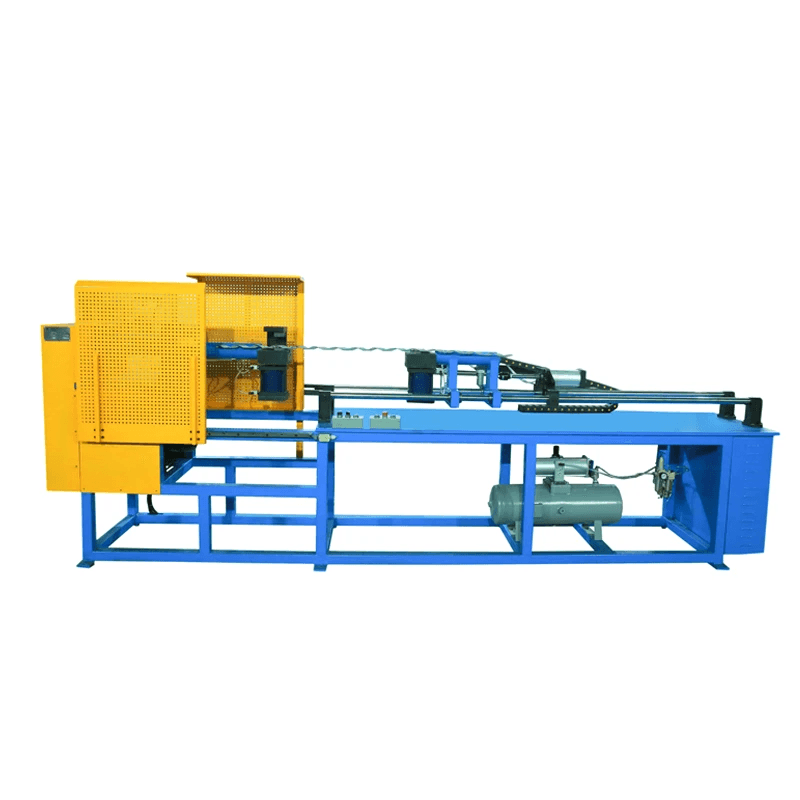
When it comes to precision wire forms, quality is paramount. Wire form manufacturers must adhere to strict quality standards to ensure that their products meet the specific needs of various industries. From automotive to aerospace, the performance of wireforms can significantly impact the overall functionality and safety of end products.
Key Quality Metrics for Wireforms
Key quality metrics for wireforms include tensile strength, dimensional accuracy, and surface finish. These metrics help assess the performance characteristics of precision wire forms under different conditions, ensuring they can withstand operational stresses without failure. Additionally, consistency in these metrics across batches is crucial; it reflects a reliable custom wire forming process that meets customer expectations.
Another important metric is fatigue resistance, which evaluates how well a wire form can endure repeated stress cycles over time. This aspect is particularly vital for applications in demanding environments such as automotive parts or industrial machinery where durability is non-negotiable. For wire form manufacturers, maintaining these quality metrics not only enhances product reliability but also builds trust with clients who rely on high-performance wire fasteners.
Certifications and Compliance in the Industry
Certifications play a significant role in establishing credibility among wire form manufacturers. Adhering to industry standards such as ISO 9001 or AS9100 demonstrates a commitment to quality management systems and continuous improvement processes within custom wire forming operations. Compliance with these certifications ensures that precision wire forms are produced consistently and meet regulatory requirements across various industries.
Moreover, specific sectors like aerospace require compliance with stringent guidelines set by organizations such as the FAA or EASA for safety-critical components. By obtaining relevant certifications, manufacturers signal their capability to deliver reliable products while minimizing risks associated with non-compliance or subpar materials. Thus, certifications are not just badges; they represent a manufacturer's dedication to excellence in producing high-quality wireforms.
The Role of Quality Control Systems
Quality control systems are integral to ensuring that every step of the custom wire forming process meets established standards. These systems typically involve regular inspections and testing at various stages—from raw material selection through final product evaluation—to identify any discrepancies early on. Effective quality control helps reduce waste and rework costs while enhancing overall efficiency within manufacturing operations.
Incorporating advanced technologies such as automated inspection tools further elevates the reliability of these systems by providing real-time data on production quality metrics like dimensional accuracy and surface finish consistency for precision wires. Additionally, continuous feedback loops allow for quick adjustments during production runs based on inspection findings—ensuring that every batch maintains high-quality standards expected from reputable wire form manufacturers.
Ultimately, investing in robust quality control systems fosters a culture of excellence within organizations focused on custom wire forming & wire fasteners—guaranteeing customers receive only top-notch products tailored precisely to their needs.
Innovations in Wire Form Technology
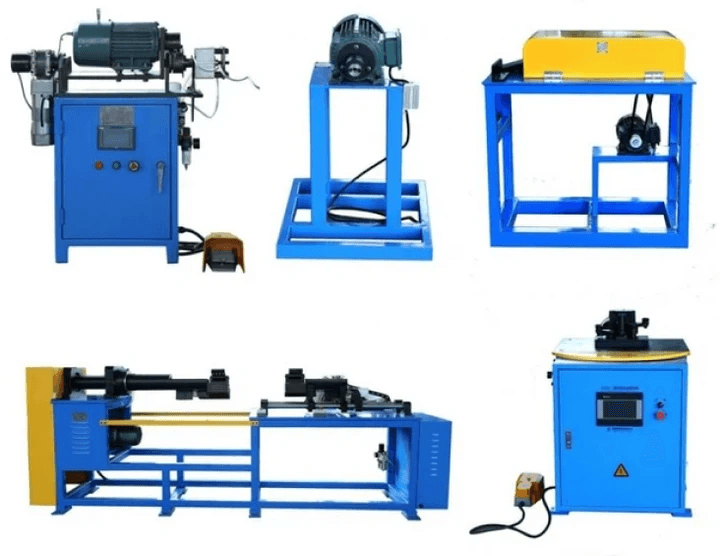
The world of wire forms is undergoing a transformation driven by innovative techniques and advanced technologies. Wire form manufacturers are continually seeking ways to enhance the efficiency and precision of their production processes. Custom wire forming has never been more sophisticated, leading to the creation of intricate designs that meet specific industry demands.
Advances in Wire Forming Techniques
In recent years, advances in wire forming techniques have revolutionized how precision wire forms are manufactured. Techniques such as CNC machining and laser cutting allow for intricate designs and tighter tolerances that were previously unattainable. These innovations enable wire form manufacturers to produce complex shapes with exceptional accuracy, resulting in high-quality wireforms that cater to diverse applications.
Moreover, new materials and coatings are being introduced into the manufacturing process, enhancing the durability and functionality of custom wire fasteners. The ability to work with various metals and alloys allows for greater customization based on specific performance requirements. This evolution not only improves product quality but also expands the range of applications for precision wire forms.
The Impact of Automation on Production
Automation has become a game-changer in the realm of custom wire forming, significantly impacting production speed and consistency. By integrating automated systems into their operations, wire form manufacturers can streamline processes that were once labor-intensive and time-consuming. This shift not only reduces human error but also enhances overall productivity, allowing companies to meet increasing market demands efficiently.
Robotic systems equipped with advanced sensors can monitor production lines in real-time, ensuring that each phase adheres to strict quality standards. As a result, manufacturers can focus on refining their designs while automation handles repetitive tasks effectively. This synergy between human expertise and machine precision is paving the way for higher-quality products at lower costs.
16A Pre-Twisted Wire Automatic Forming Production Line
One standout innovation is the 16A pre-twisted wire automatic forming production line, which epitomizes modern advancements in this sector. This specialized line allows for rapid production of twisted wires with minimal manual intervention while maintaining high levels of accuracy and consistency across batches. By automating this process, custom wire forming becomes more efficient, enabling manufacturers to respond swiftly to customer needs without compromising quality.
The 16A system exemplifies how technology can enhance traditional manufacturing methods—providing flexibility while ensuring that every piece meets stringent specifications required by various industries like automotive or aerospace manufacturing. As demand grows for tailored solutions such as custom wire fasteners or precision components, innovations like these will be crucial for staying competitive in an ever-evolving market landscape.
Applications of Wire Forms in Various Industries
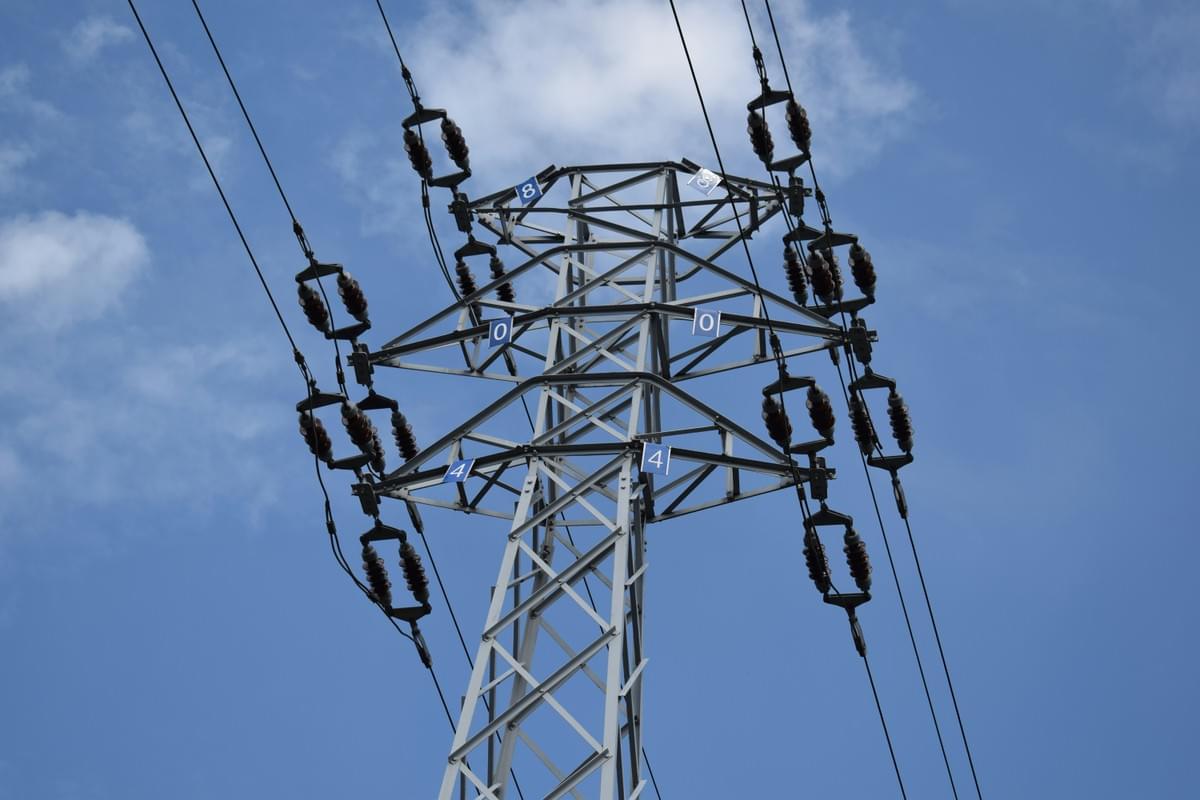
Precision wire forms are indispensable across various sectors, serving as fundamental components that enhance functionality and efficiency. From automotive manufacturing to aerospace applications, the versatility of wireforms allows them to meet specific needs in diverse environments. Understanding these applications can illuminate the importance of choosing the right wire form manufacturer for custom wire forming projects.
Wire Forms in Automotive Manufacturing
In the automotive industry, precision wire forms play a pivotal role in ensuring safety and performance. Custom wire forming is utilized to create essential components such as clips, brackets, and support structures that hold various parts together securely. A reliable wire form manufacturer can provide tailored solutions that enhance vehicle durability while meeting stringent industry standards.
Moreover, automotive manufacturers often seek innovative designs that can withstand extreme conditions without compromising quality or performance. This is where precision wire comes into play; it allows for designs that are not only functional but also lightweight and resilient. By partnering with experienced wire form manufacturers, companies can ensure they receive high-quality products designed specifically for their unique requirements.
Uses in Electronics and Aerospace
The electronics sector relies heavily on precision wire forms for a myriad of applications, including connectors, switches, and circuit board supports. These components must meet exacting specifications to ensure reliability and efficiency in electronic devices. Custom wire forming enables manufacturers to produce intricate shapes tailored to fit specific electronic designs seamlessly.
Similarly, the aerospace industry demands unparalleled precision due to the critical nature of its components—think wiring harnesses or structural supports for aircraft interiors. Here again, custom solutions from skilled wire form manufacturers become crucial; they understand how to form metal wire into complex configurations that meet rigorous safety standards while minimizing weight. The ability to customize these forms ensures optimal performance under challenging conditions.
Custom Wire Fasteners for Construction and Fabrication
In construction and fabrication industries, custom wire fasteners are essential for creating strong connections between materials while allowing flexibility during assembly processes. These fasteners come in various shapes and sizes depending on their intended use—from simple hooks to more complex fastening systems designed for heavy-duty applications. By employing a specialized wire form manufacturer adept at custom wire forming techniques, businesses can achieve superior results tailored precisely to their projects' needs.
Additionally, using precision wire forms helps streamline construction processes by reducing installation time through efficient fastening solutions—saving both time and labor costs on-site! The ability of these fasteners to adapt easily makes them invaluable in fabrication settings where modifications may be frequently required due to design changes or unforeseen challenges during production phases. Ultimately, investing in quality custom solutions ensures long-lasting results that stand up against environmental stresses over time.
Conclusion
In the world of manufacturing, precision wire forms are becoming increasingly essential across various industries. As technology advances, the demand for custom wire forming solutions continues to rise, leading to innovative techniques and applications that enhance product performance. The future of this field looks bright, with wire form manufacturers poised to meet evolving customer needs through tailored solutions.
The Future of Precision Wire Forms
The future of precision wire forms is characterized by ongoing advancements in manufacturing techniques and materials. Innovations such as automation and smart technologies are setting new benchmarks for efficiency and quality in custom wire forming processes. As industries evolve, the ability to produce high-quality wireforms with rapid turnaround times will be a significant competitive advantage for wire form manufacturers.
Choosing the Right Wire Form Manufacturer
Selecting the right wire form manufacturer can be a daunting task given the plethora of options available today. It’s crucial to consider factors like experience, quality standards, and customization capabilities when making your choice. A reliable partner not only understands how to form metal wire efficiently but also prioritizes customer service and support throughout your project.
Final Thoughts on Custom Wire Forming Options
Custom wire forming offers an array of possibilities that cater to specific industry needs while enhancing product reliability and performance. By leveraging precision wire forms from skilled manufacturers, businesses can achieve greater operational efficiency and innovation in their products. Ultimately, investing in high-quality custom wire fasteners is an investment in the future success of any manufacturing endeavor.