Introduction
In the world of manufacturing, wire forming machines play a crucial role in shaping metal wire into functional forms. These machines are the backbone of industries that rely on precision and custom solutions, leading to the increasing significance of custom wire forms. Understanding what wire forms are and how they fit into various applications is essential for grasping their impact on different sectors.
Understanding Wire Forming Machines
Wire forming machines are specialized equipment designed to manipulate metal wire into specific shapes and configurations. The process involves bending, twisting, and cutting wire to create components that serve various functions across multiple industries. These machines come in various types, each tailored for different manufacturing needs, making them indispensable for wire form companies.
The Importance of Custom Wire Forms
Custom wire forming & wire fasteners are vital in meeting unique project specifications that off-the-shelf solutions simply can't provide. Tailored designs ensure that products fit perfectly within their intended applications, enhancing functionality and performance. This customization is not just a trend; it's a necessity that drives innovation within the industry.
An Overview of Wire Form Companies
Wire form companies specialize in producing these intricate shapes using advanced techniques and high-quality materials. With numerous suppliers available, it’s essential to evaluate each company based on their capabilities and innovations. By comparing different wire forms suppliers, businesses can find the perfect partner to fulfill their specific needs while ensuring quality and reliability.
What Are Wire Forms?
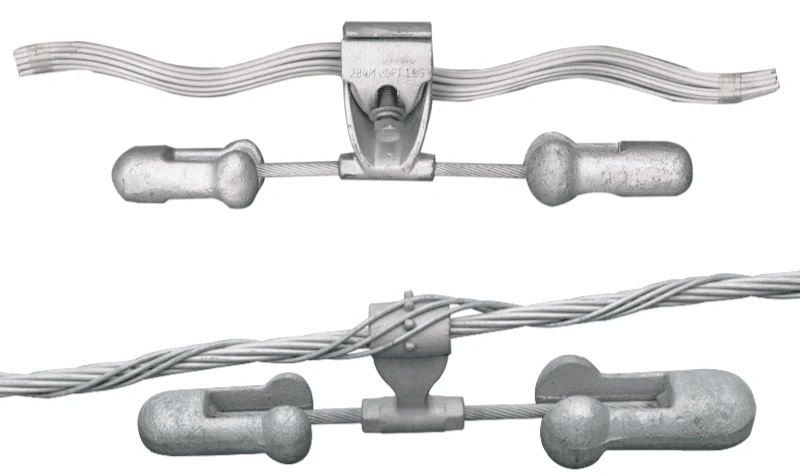
Wire forms are versatile components crafted from metal wire, designed for various applications across multiple industries. These forms can be customized to meet specific needs, making them essential in sectors ranging from automotive to electronics. Understanding what wire forms are and how they function is crucial for anyone looking into the offerings of wire form companies.
Definition and Applications
So, what are wire forms? Essentially, they are shapes or structures made from bent or shaped wire, often used as fasteners, supports, or structural elements in various products. The applications of these wire forms are vast; they can serve as clips, brackets, or even intricate designs in consumer goods. Custom Wire Forming & Wire Fasteners allow manufacturers to create specialized solutions tailored to their unique requirements.
Variety in Designs and Uses
The beauty of wire forms lies in their diversity—there's practically no limit to the designs that can be created! From simple loops and hooks to complex assemblies that integrate with other components, the variety is staggering. This flexibility means that businesses can find solutions suited precisely to their needs when sourcing from reliable Wire Forms Suppliers.
Key Industries Utilizing Wire Forms
Wire forms play a pivotal role across numerous industries, each leveraging their unique properties for different applications. For instance, the automotive industry uses these components for everything from securing parts to enhancing safety features. Similarly, electronics manufacturers rely on custom wire forming techniques for connectors and supports that ensure device functionality—showcasing just how integral these items are within today's manufacturing landscape.
The Process of Making Wire
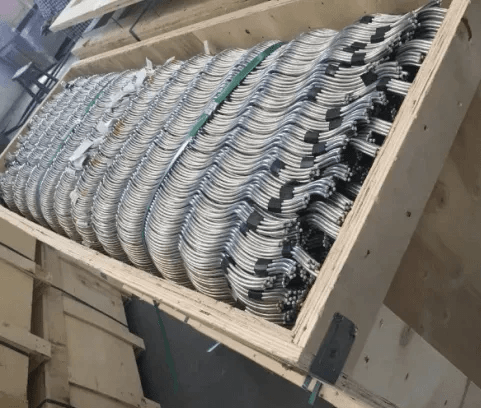
Creating wire forms is an intricate process that involves a blend of artistry and engineering. Wire forming companies utilize a variety of techniques to shape metal into the desired configurations, ensuring that each custom wire form meets specific requirements. Understanding what the process of making wire entails can provide insights into the quality and functionality of the final product.
Overview of Wire Forming Techniques
Wire forming techniques vary widely among wire form companies, each employing methods tailored to their production needs. Common techniques include bending, coiling, and twisting, allowing for a diverse range of designs and applications. Whether it’s for automotive parts or decorative elements, these techniques are essential in crafting custom wire forming & wire fasteners that stand up to rigorous demands.
Steps in Custom Wire Forming
The journey from raw material to finished product in custom wire forming involves several key steps. Initially, designers create precise specifications based on client needs; this stage is crucial for ensuring that what are wire forms will meet expectations. Next comes the actual shaping process where machines manipulate the metal using various methods like CNC machining or manual bending—each step meticulously monitored by skilled technicians from leading wire forming companies.
Materials Used in Wire Production
The choice of materials plays a critical role in determining the quality and durability of wire forms. Common materials include stainless steel, copper, and aluminum; each offers unique properties suitable for different applications across industries. Wire Forms suppliers often source high-grade materials to ensure their products not only meet industry standards but also provide longevity and reliability in use.
Spotlight on Wire Form Companies
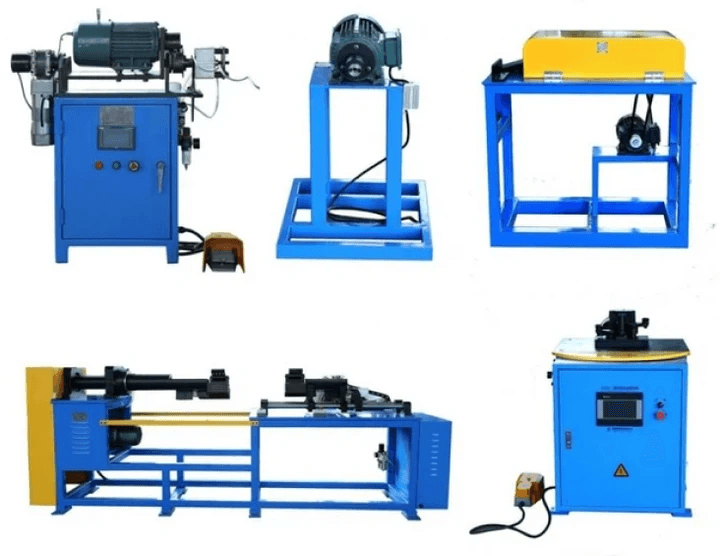
When it comes to wire form companies, the industry is filled with a diverse range of players, each offering unique capabilities and specialties. From small shops that focus on niche markets to large manufacturers that serve global needs, the landscape is anything but boring. Understanding the leading players in this sector can provide valuable insights into what custom wire forming & wire fasteners can offer.
Innovations from Spark Fittings
Spark Fittings has made waves in the wire form industry by pioneering innovative techniques that streamline production and enhance product quality. Their commitment to research and development has led to breakthroughs in materials used for custom wire forms, making them lighter yet stronger than ever before. This innovation not only answers What is the process of making wire called? but also elevates standards across the board.
One notable advancement from Spark Fittings includes their use of eco-friendly materials that reduce environmental impact without compromising performance. This aligns with growing trends toward sustainability within manufacturing sectors, reflecting how modern wire form companies are adapting to consumer demands for greener solutions. As a result, clients benefit from both cutting-edge technology and responsible practices.
Comparing Wire Forms Suppliers
When it comes time for businesses to choose between various wire forms suppliers, careful comparison becomes essential for success. Factors such as lead times, pricing structures, customization options, and customer service play critical roles in decision-making processes. By evaluating these aspects among different custom wire forming & wire fasteners providers, companies can identify which supplier aligns best with their specific needs.
Additionally, potential clients should consider each supplier's reputation within key industries utilizing wire forms; this often serves as an indicator of reliability and quality assurance measures practiced by these firms. Conducting thorough research on past performance through case studies or testimonials can offer further clarity on what each company brings to the table regarding What are wire forms? Ultimately, selecting the right partner can significantly impact a business's operational efficiency and overall success.
Custom Wire Forming & Wire Fasteners
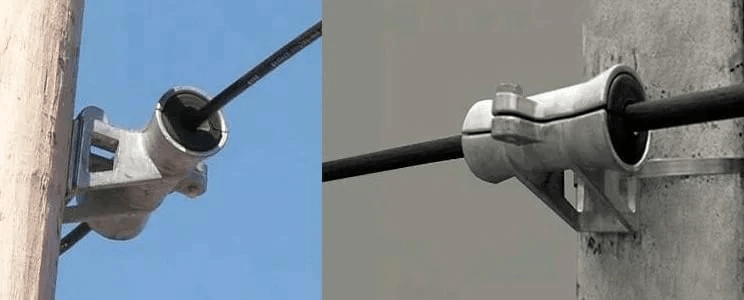
Custom wire forming and wire fasteners play a crucial role in various industries, providing tailored solutions that meet specific needs. The importance of customization cannot be overstated, as it allows businesses to create unique wire forms that enhance functionality and performance. With the growing demand for specialized products, wire form companies are stepping up their game to offer innovative designs and solutions.
Importance of Customization
Customization is key in the world of wire forms; it enables companies to adapt their products to fit precise requirements. Whether it's for intricate machinery or everyday items, custom wire forming allows manufacturers to design components that optimize efficiency and usability. By working closely with clients, wire forming companies can ensure that each custom piece meets exact specifications while also considering factors like durability and cost-effectiveness.
The process of making wire called custom wire forming involves several stages where adjustments can be made based on customer feedback or evolving industry standards. This adaptability not only improves product quality but also fosters strong relationships between manufacturers and clients. Ultimately, the ability to customize enhances competitiveness among wire forms suppliers, driving innovation across the sector.
Applications of Wire Fasteners
Wire fasteners are essential components in numerous applications across various industries, from construction to electronics. These versatile tools are used to secure items together, providing stability and support where needed most. In sectors such as automotive manufacturing or aerospace engineering, reliable fastening solutions are critical for safety and performance.
Among the many applications of custom wire forming & wire fasteners are cable management systems that organize and protect electrical wiring in buildings or vehicles. Additionally, they play a significant role in creating fixtures for lighting installations or supporting structures in furniture design. As industries continue to evolve, so too do the demands for innovative fastening solutions offered by leading wire form companies.
With advancements in technology and materials used in production processes, there’s a growing opportunity for new applications of these essential tools. Innovative designs can lead to more efficient installations while reducing overall costs associated with maintenance or replacement parts. Thus, understanding what are wire forms becomes increasingly important for businesses looking to stay ahead in their respective markets.
Case Studies of Successful Custom Wire Forms
To illustrate the impact of customizations within this field, let’s explore some case studies from prominent players among wire form companies that have excelled through bespoke designs. One notable example is an automotive manufacturer who required specialized clips for securing wiring harnesses within their vehicles; traditional options fell short due to space constraints imposed by modern vehicle designs.
By collaborating with a skilled team at a leading supplier specializing in custom wire forming & fasteners, they developed streamlined clips tailored specifically for their needs—resulting not only improved assembly times but also enhanced reliability during operation! This partnership exemplifies how effective communication between clients and suppliers can yield remarkable outcomes when addressing unique challenges faced by industries today.
Another successful case involved a medical device company seeking lightweight yet robust supports designed specifically around delicate instruments used during surgical procedures—this required precision engineering coupled with stringent quality control measures adhered by established wire forming companies known for excellence within medical applications! Thanks largely due diligence taken throughout every stage—from concept through production—the end result was both functional AND aesthetically pleasing!
Quality Control in Wire Form Manufacturing
In the world of wire forming, quality control is paramount for ensuring that products meet industry standards and customer expectations. Wire form companies must adhere to strict guidelines and regulations to maintain their reputation and deliver reliable products. This section delves into the standards, testing methods, and the overall importance of quality assurance in custom wire forming and wire fasteners.
Standards and Certifications
Wire forming companies often operate under a set of established standards that dictate how products should be manufactured and tested. These standards include ISO certifications, which ensure consistency in quality management systems across various production processes. By adhering to such certifications, wire forms suppliers can demonstrate their commitment to producing high-quality custom wire forms that are safe for use in various applications.
Additionally, compliance with industry-specific standards—such as ASTM or ANSI—further solidifies a company's credibility among clients seeking reliable wire fasteners. These certifications not only enhance customer trust but also facilitate smoother transactions within competitive markets. Ultimately, maintaining these standards is crucial for any wire form company aiming to thrive in an ever-evolving industry landscape.
Testing Methods Used
To ensure the integrity of their products, wire form companies employ a variety of testing methods throughout the manufacturing process. Common tests include tensile strength evaluations, fatigue testing, and dimensional inspections—all designed to verify that the custom wire forms meet specified requirements. By utilizing advanced technology such as computer-aided design (CAD) simulations during these tests, manufacturers can predict performance issues before they arise.
Moreover, non-destructive testing techniques are often employed to examine materials without compromising their usability. This proactive approach helps identify potential flaws early on in what is the process of making wire called? By ensuring each product undergoes rigorous testing procedures, suppliers can confidently deliver high-quality solutions tailored to client needs.
Importance of Quality Assurance
Quality assurance is not just a checkbox on a manufacturing list; it’s an ongoing commitment that influences every aspect of production for wire form companies. A robust quality assurance program ensures consistency across all stages—from raw material selection through final assembly—resulting in superior custom wire forms that perform reliably under stress. Without this level of diligence, even minor defects could lead to significant failures down the line.
Furthermore, investing in quality assurance fosters long-term relationships between suppliers and customers by building trust through consistent product performance and reliability. As demand grows for specialized applications like custom wire fasteners across diverse industries, maintaining high-quality standards becomes essential for remaining competitive among leading wire forms suppliers. In conclusion, effective quality control measures are vital for sustaining excellence within the dynamic world of custom wire forming.
Conclusion
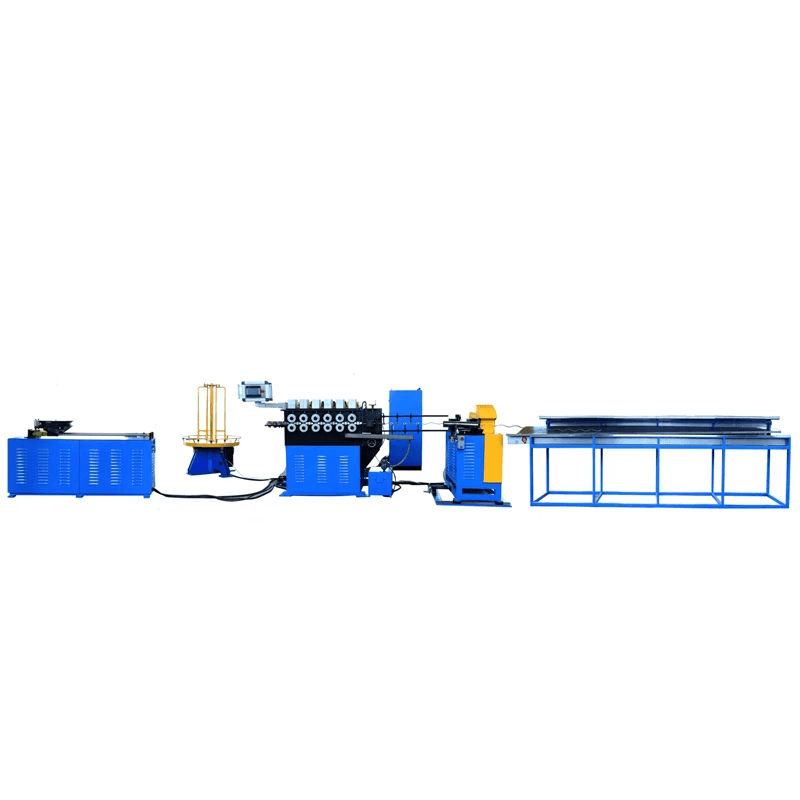
The world of wire forms is both intricate and essential, offering solutions across a myriad of industries. Understanding what wire forms are and recognizing the importance of custom wire forming & wire fasteners can significantly enhance product functionality and sustainability. As we conclude this exploration, it’s clear that the collaboration between clients and wire form companies is vital in creating tailored solutions that meet specific needs.
Key Takeaways on Wire Forms
Wire forms are versatile components that serve various applications, from automotive to aerospace. They come in diverse designs, showcasing how customization plays a crucial role in meeting industry demands. Moreover, knowing what the process of making wire is called helps appreciate the craftsmanship involved in producing high-quality wire forms.
The Growing Demand for Custom Wire Solutions
In today's fast-paced market, the demand for custom solutions provided by wire forming companies is on the rise. Industries are increasingly seeking unique designs that enhance efficiency and performance while minimizing waste. This trend underscores an important shift towards innovation, where custom wire forming & wire fasteners become integral to product development.
Future Trends in Wire Forming Industry
Looking ahead, several trends are shaping the future of the wire forming industry. Technological advancements will likely streamline production processes and improve precision in creating complex designs, thus benefiting both manufacturers and clients alike. Furthermore, with an increased focus on sustainability, many wire form companies will adopt eco-friendly materials and practices to meet consumer expectations.