Introduction
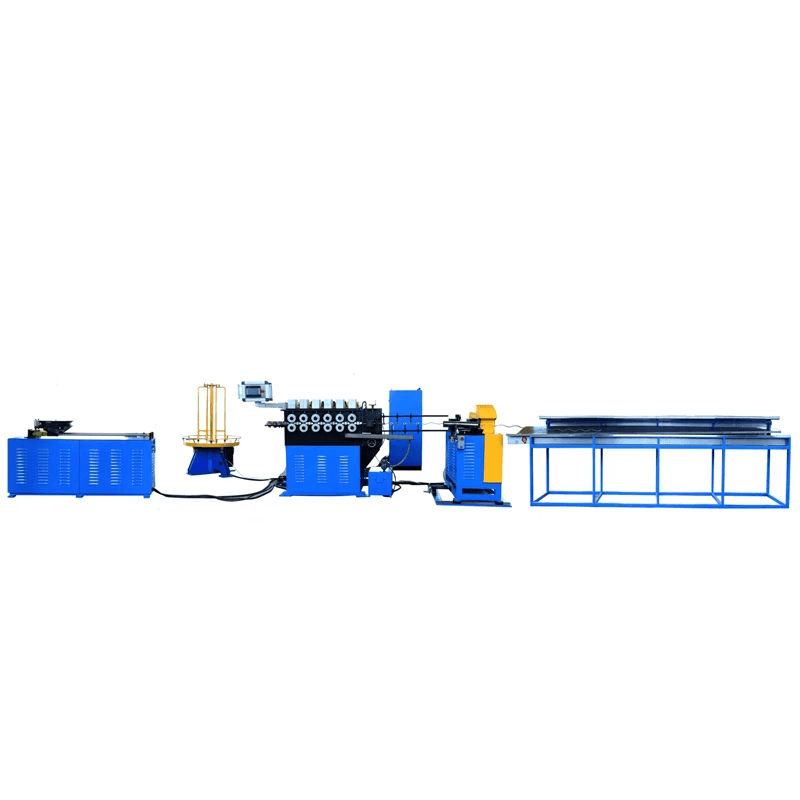
The wire forming industry plays a pivotal role in various sectors, from automotive to telecommunications, where precision and customization are paramount. As businesses increasingly seek tailored solutions to meet their unique needs, the demand for custom wire forming services has surged. Leading wire forming manufacturers are stepping up to the plate, providing innovative products that cater to diverse applications.
Overview of Wire Forming Industry
Wire forming is an essential process that involves shaping metal wire into specific forms and configurations for various industrial applications. This industry is characterized by its adaptability and innovation, as manufacturers continuously develop new techniques and technologies to enhance production efficiency and product quality. Key players in the market are committed to pushing the boundaries of what is possible in wire forming, ensuring that they remain competitive in an ever-evolving landscape.
Importance of Custom Solutions
Custom solutions in wire forming are crucial because they allow businesses to obtain products that perfectly fit their specifications and requirements. Off-the-shelf items often fall short when it comes to meeting unique design needs or performance standards; hence, companies turn to custom wire forming & bending services for a more personalized approach. By working closely with leading wire forming manufacturers, clients can achieve significant improvements in functionality and efficiency.
Key Players in Wire Forming
Among the key players in the wire forming industry is Spark Electronic Technology Wuxi Co., Ltd., renowned for its advanced manufacturing equipment designed for preformed armor rods and cable accessories used in electricity transmission systems. Other notable companies include Jabil Inc., known for its extensive capabilities across multiple sectors, and Precision Wire Components, which specializes in high-quality custom solutions tailored for specific applications. These leading wire forming manufacturers exemplify excellence through their commitment to innovation and customer satisfaction.
What is Wire Forming?
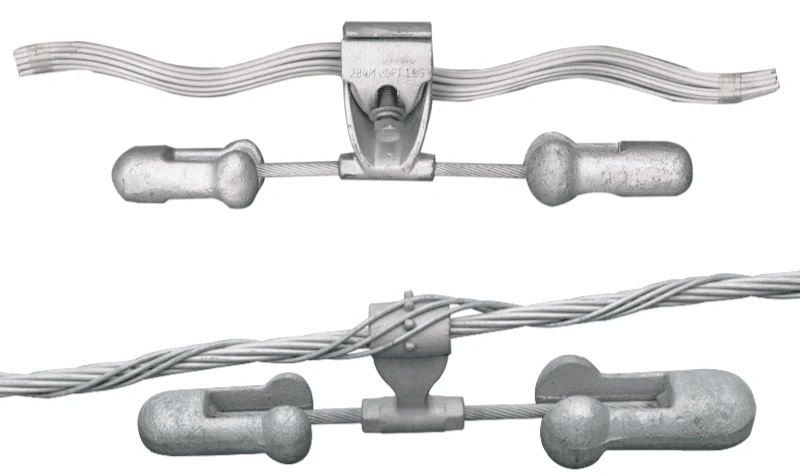
Wire forming is a specialized manufacturing process that involves bending, shaping, and assembling wire into various configurations for a wide array of applications. This technique is crucial in industries such as automotive, aerospace, electronics, and construction, where precision and customization are paramount. So when you ask, What is wire forming? think of it as the art of transforming simple wire into complex components that meet specific industry needs.
Definition and Applications
At its core, wire forming refers to the process of manipulating wire into desired shapes or structures through techniques like bending, coiling, or twisting. This versatile method finds applications in creating everything from intricate brackets and clips to robust frames and supports used in machinery. Leading wire forming manufacturers leverage advanced technology to produce custom wire forming services tailored to meet the unique requirements of their clients.
Common Materials Used
When it comes to materials for wire forming, steel is often the go-to choice due to its strength and durability; however, other materials like aluminum and stainless steel are also popular depending on the application. Each material offers unique properties—steel provides high tensile strength while aluminum offers lightweight flexibility. Custom wire forming & bending services can utilize these materials effectively to create components that not only function well but also withstand environmental challenges.
The Importance of Precision
Precision in wire forming cannot be overstated; even minor discrepancies can lead to significant failures in applications where safety or functionality is critical. Wire forming manufacturers invest heavily in state-of-the-art equipment and skilled labor to ensure that every bend or twist meets exact specifications. The importance of precision extends beyond aesthetics; it affects performance metrics such as load-bearing capacity and fatigue resistance—essential factors for any successful project involving custom wire forms.
Leading Wire Forming Manufacturers
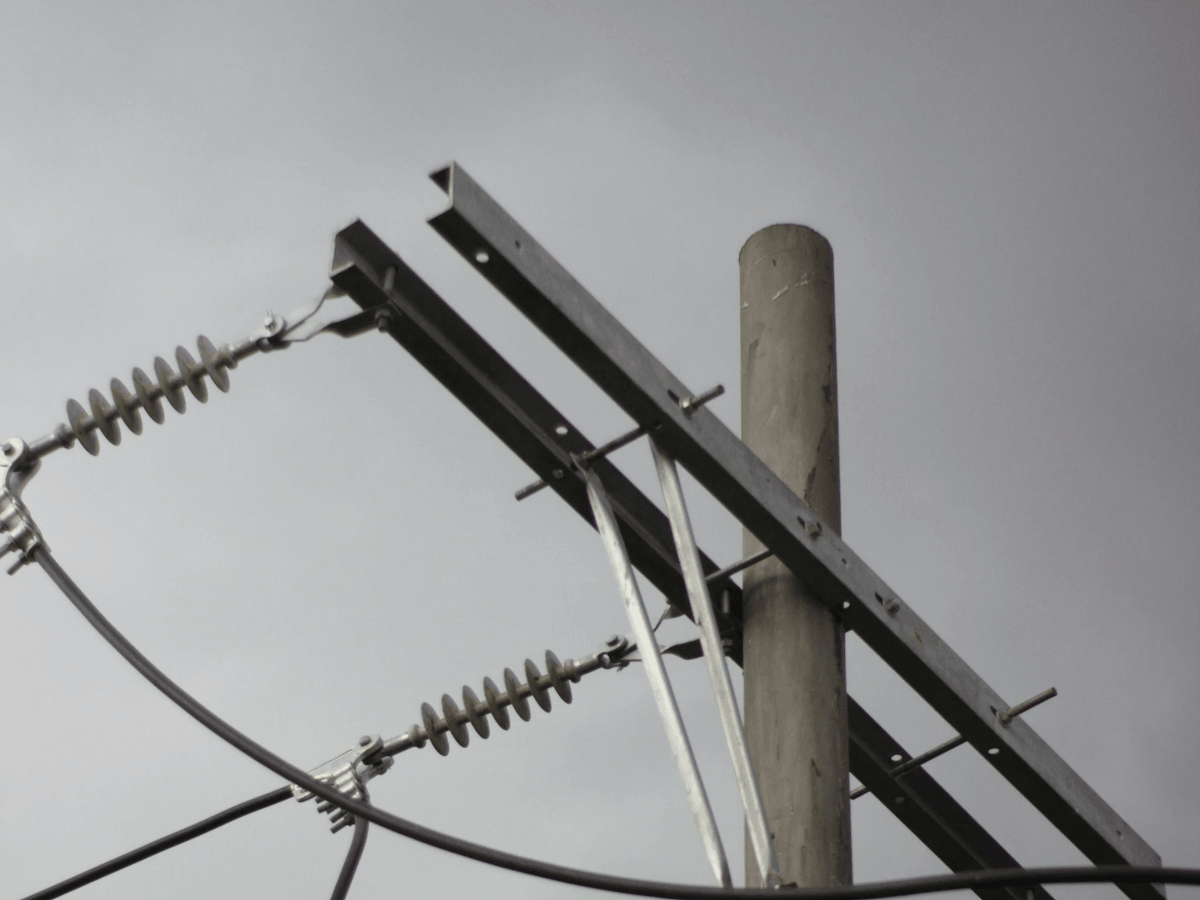
In the dynamic landscape of wire forming manufacturers, several companies stand out for their innovation, quality, and customization capabilities. These leading wire forming manufacturers not only meet industry standards but also push the boundaries of what is possible in wire forming and bending services. Understanding who these key players are can help businesses make informed decisions when seeking custom wire forming solutions.
Spark Electronic Technology Wuxi Co., Ltd.
Spark Electronic Technology Wuxi Co., Ltd. is a leading company specializing in manufacturing equipment for preformed armor rods, tension clamps, and cable accessories for ADSS and OPGW applications. Their machines are designed to help customers produce high-quality preformed products that facilitate the efficient transmission and distribution of electricity as well as electrified railways. With an impressive lineup that includes a preformed armor rods forming machine, chamfering machine, automatic glue sand blasting machine, wire tension shaping machine, hydraulic bending machine, grinding head machine, and tensile testing machine, Spark Electronic truly exemplifies excellence in custom wire forming services.
What sets Spark Electronic apart from other wire forming manufacturers is their commitment to precision engineering and customer satisfaction. The advanced technology used in their equipment ensures that every component produced meets stringent quality standards while also allowing for tailored solutions that fit specific project requirements. This dedication to customization makes them a preferred partner for businesses looking to enhance their operational efficiency through innovative wire products.
Jabil Inc.
Jabil Inc., another giant among leading wire forming manufacturers, offers comprehensive solutions across various industries including automotive, healthcare, and consumer electronics. Known for its cutting-edge technology and extensive manufacturing capabilities, Jabil excels at providing custom wire forming & bending services tailored to meet diverse client needs. Their approach combines advanced manufacturing techniques with a deep understanding of market demands to create innovative products that stand out in competitive environments.
One of the key strengths of Jabil lies in its ability to integrate sustainability into its manufacturing processes while maintaining high standards of quality control. By leveraging advanced materials science along with efficient production methods like the wire drawing metal forming process, they ensure that their offerings are both environmentally friendly and cost-effective. This focus on sustainable practices positions Jabil as a forward-thinking leader among wire forming manufacturers committed to making a positive impact on both clients' bottom lines and the planet.
Precision Wire Components
Precision Wire Components rounds out our list of leading wire forming manufacturers with its unwavering commitment to delivering high-quality products across various sectors such as aerospace, medical devices, and electronics. Specializing in custom solutions that cater specifically to unique client specifications enables them to stand out in an increasingly crowded market space where precision matters most. Their expertise spans multiple facets of the industry—from design engineering through production—making them a one-stop-shop for all things related to custom wire forming services.
The company's focus on advanced technologies allows it to maintain rigorous quality control throughout every stage of production—from initial concept development through final inspection processes akin to those seen in steel wire manufacturing operations like drawing techniques used during fabrication phases. This meticulous attention ensures clients receive only top-notch products while benefiting from reduced lead times associated with streamlined operations inherent within Precision Wire Components' facilities.
Custom Wire Forming Services
In today's competitive landscape, Custom Wire Forming Services have become essential for industries seeking unique and effective solutions. These services allow companies to tailor wire products to their specific needs, ensuring that they meet the exact specifications required for various applications. Leading wire forming manufacturers are increasingly focusing on customization to enhance their offerings and cater to diverse market demands.
Tailored Solutions for Various Industries
The versatility of custom wire forming enables manufacturers to serve a broad range of industries, from automotive and aerospace to telecommunications and construction. Each sector has its unique requirements; for example, the automotive industry often requires intricate wire components that can withstand high stress and temperature variations. By leveraging advanced techniques in what is wire forming?, manufacturers can deliver tailored solutions that enhance product performance while adhering to industry standards.
Moreover, leading wire forming manufacturers utilize cutting-edge technologies like CNC machining and automated bending processes to create bespoke designs efficiently. This adaptability not only streamlines production but also reduces lead times, allowing businesses to respond quickly to market changes. As a result, companies can achieve greater operational efficiency while maintaining high-quality standards in their custom wire forming & bending services.
Benefits of Customization
Customization in wire forming offers numerous advantages that extend beyond mere aesthetics or design preferences. One significant benefit is the ability to produce components that fit perfectly within existing systems or machinery, reducing the need for modifications or additional parts. This precision ultimately leads to cost savings over time as businesses avoid unnecessary downtime caused by ill-fitting components.
Furthermore, custom solutions often translate into improved functionality and performance of end products. For instance, when asking how do you manufacture steel wire? one must consider how tailored specifications can optimize strength and flexibility based on specific application needs—whether it's for suspension systems or electrical wiring harnesses. The ability of leading wire forming manufacturers to provide such targeted solutions ensures that customers receive products designed explicitly for their intended use.
Case Studies of Successful Projects
To illustrate the impact of Custom Wire Forming Services, consider the case study involving Spark Electronic Technology Wuxi Co., Ltd., a prominent player in this field. They successfully developed specialized preformed armor rods used in overhead power lines—a critical component in ensuring reliable electricity transmission across vast distances. By employing advanced machinery like hydraulic bending machines and tensile testing machines, they produced robust solutions tailored specifically for electrified railways.
Another notable example includes Jabil Inc., which partnered with an automotive manufacturer needing custom wiring harnesses designed for electric vehicles (EVs). Through innovative design processes and rigorous quality control measures typical of leading wire forming manufacturers, Jabil delivered a solution that not only met safety standards but also enhanced vehicle performance by optimizing weight distribution.
These successful projects underscore the transformative potential of custom wire forming services across various sectors—demonstrating how tailored approaches can lead directly to innovation and improvement within industries reliant on precision-engineered components.
Manufacturing Steel Wire
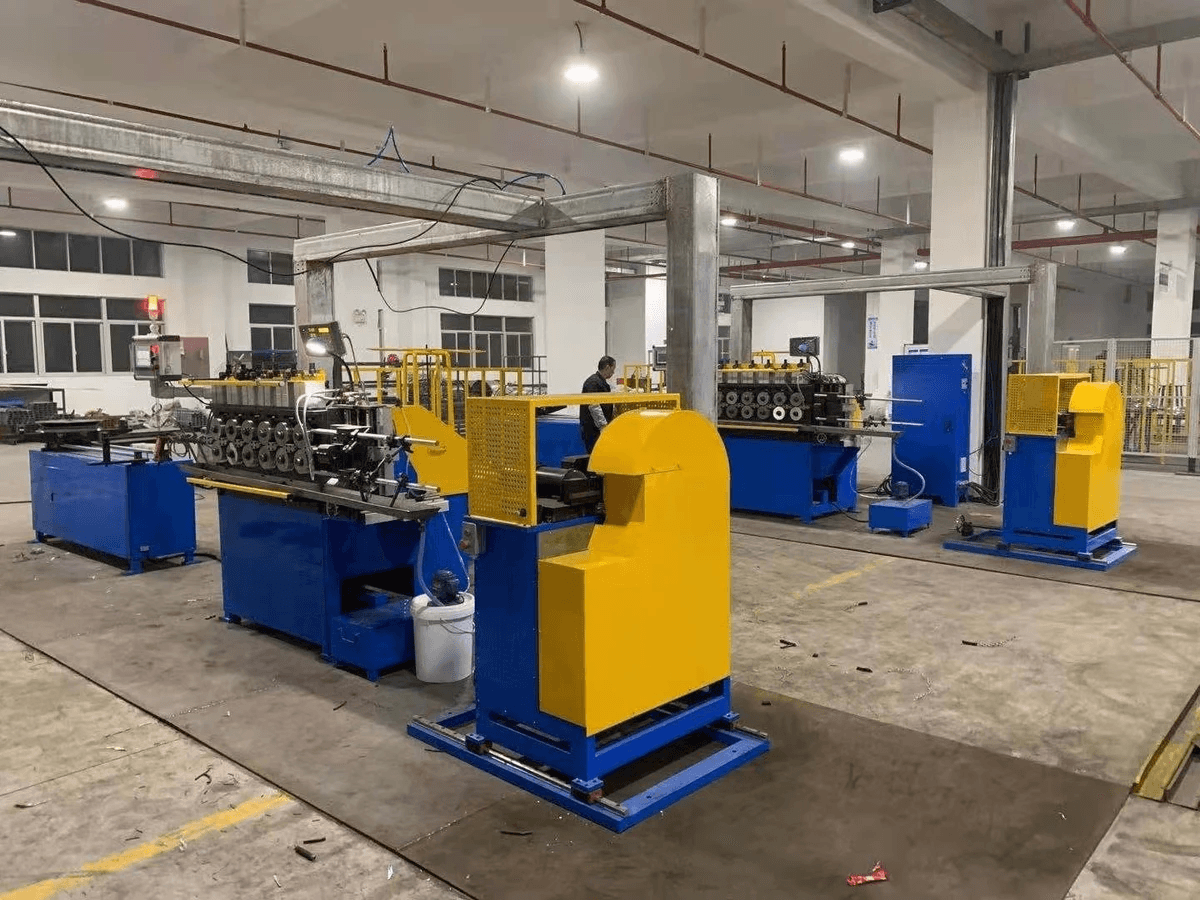
The manufacturing of steel wire is a crucial process in the wire forming industry, with various techniques employed to ensure high-quality output. Understanding how do you manufacture steel wire? involves delving into multiple stages, from raw material selection to the final product. Leading wire forming manufacturers utilize advanced technologies to enhance efficiency and precision throughout this process.
Overview of Steel Wire Manufacturing Process
The steel wire manufacturing process begins with selecting high-quality raw materials, usually in the form of steel rods or coils. These materials undergo several stages of processing, including heating, drawing, and finishing, which transform them into the desired wire specifications. The entire procedure is designed to maintain consistency and meet the rigorous standards required by industries relying on custom wire forming services.
Leading wire forming manufacturers often employ automated systems that streamline production while ensuring that each step adheres to quality standards. This automation not only reduces labor costs but also minimizes human error, making it easier to achieve precision in every piece produced. By focusing on efficiency and quality control, these manufacturers can deliver reliable products that meet their clients' diverse needs.
Techniques for Wire Drawing
Wire drawing is a pivotal technique in manufacturing steel wire and is essential for achieving the desired diameter and mechanical properties of the final product. The process involves pulling a metal rod through a series of dies that progressively reduce its diameter while increasing its length—this is what we refer to when discussing what is wire drawing metal forming process? Each die contributes to shaping the wire while maintaining its integrity.
There are different methods for conducting this operation, such as single-pass drawing or multi-pass drawing techniques depending on the material’s properties and required specifications. Manufacturers often utilize specialized equipment like hydraulic presses and draw benches designed specifically for various types of wires—whether they are used in construction or automotive applications—and these machines can be found among leading wire forming manufacturers’ offerings.
Moreover, custom wire forming & bending services may also incorporate these techniques to create intricate shapes or designs tailored for specific applications. The versatility offered by these processes allows manufacturers to cater to a wide range of industries effectively.
Quality Control in Wire Production
Quality control plays a vital role in ensuring that manufactured steel wires meet industry standards and client expectations consistently. Leading wire forming manufacturers implement stringent quality assurance protocols at every stage—from raw material inspection through final product testing—to guarantee reliability and performance under various conditions.
Techniques such as tensile testing are commonly employed during production; this assesses how much force a piece can withstand before breaking—an essential factor when considering durability for end users. Additionally, visual inspections help identify any surface defects early on before they become costly issues down the line.
By prioritizing quality control throughout their processes, manufacturers not only enhance their reputation but also foster long-term relationships with clients who rely on custom solutions tailored specifically for their needs—ultimately contributing positively to overall business success within the competitive landscape of the industry.
Understanding Wire Drawing Metal Forming Process
Wire drawing is a crucial metal forming process that transforms raw materials into usable wire products. This technique is essential for various applications, including construction, automotive, and electronics. To truly grasp the significance of wire drawing in the wire forming industry, we must delve into its step-by-step breakdown, the equipment involved, and how it compares to other metal forming techniques.
Step-by-Step Breakdown
The wire drawing process begins with selecting a suitable rod of metal, typically steel or copper. The rod is then pulled through a series of progressively smaller dies to reduce its diameter while increasing its length—this is where the magic happens! As leading wire forming manufacturers know well, precision during this stage is vital; even minor deviations can lead to significant inconsistencies in the final product.
Once the desired diameter is achieved, the drawn wire may undergo additional processes such as annealing or coating for improved properties or aesthetics. Afterward, quality control measures are implemented to ensure that the finished product meets industry standards and customer specifications. In summary, understanding how do you manufacture steel wire through this meticulous process highlights the importance of custom wire forming services tailored to specific needs.
Equipment Used in Wire Drawing
The equipment used in wire drawing varies depending on the scale of production and specific requirements of different applications. At Spark Electronic Technology Wuxi Co., Ltd., cutting-edge machines like preformed armor rods forming machines and hydraulic bending machines play a pivotal role in producing high-quality products efficiently. Other essential equipment includes tensile testing machines to ensure that each batch meets stringent quality standards.
Additionally, automatic glue sand blasting machines help enhance surface finish while chamfering machines prepare edges for better handling during subsequent operations. This diverse array of machinery illustrates why leading wire forming manufacturers invest heavily in advanced technology to maintain competitive advantages and deliver top-notch custom wire forming & bending services.
Comparison with Other Metal Forming Techniques
When comparing wire drawing with other metal forming techniques such as forging or stamping, it's essential to consider their unique advantages and limitations. While forging involves shaping metals by applying compressive forces at elevated temperatures—ideal for producing strong components—wire drawing excels at creating long lengths of uniform cross-sections with excellent tensile strength.
Stamping can be efficient for producing flat parts quickly but lacks versatility regarding shape complexity compared to drawn wires that can be customized extensively for various applications. Ultimately, understanding what is wire forming? leads us back to recognizing how integral these processes are within industries reliant on precise metal components manufactured by leading companies in this field.
Conclusion
In the ever-evolving landscape of the wire forming industry, understanding the nuances of custom solutions and the capabilities of leading wire forming manufacturers is crucial. As we look to the future, advancements in technology and manufacturing processes will continue to shape how we approach wire forming. This conclusion serves as a springboard to explore future trends, guide manufacturers' selection, and emphasize the benefits of custom wire forming & bending services.
Future Trends in Wire Forming
The future of wire forming is poised for exciting developments, particularly with innovations in automation and material science. Manufacturers are increasingly adopting smart technologies that enhance precision and efficiency in processes such as wire drawing metal forming process. Additionally, sustainability is becoming a focal point; more companies are exploring eco-friendly materials and practices that minimize waste while maintaining high standards for quality.
Choosing the Right Manufacturer
Look for leading wire forming manufacturers with proven track records in quality assurance and customer satisfaction. It's essential to assess their capabilities—such as Spark Electronic Technology Wuxi Co., Ltd.—which specializes in machinery for preformed armor rods and other cable accessories vital for modern infrastructure.
Benefits of Custom Wire Forming & Bending Services
Engaging with custom wire forming & bending services offers numerous advantages tailored specifically to your project needs. These services allow you to achieve precise specifications that standard products may not fulfill, ensuring that your applications perform optimally under various conditions. Furthermore, working closely with experienced manufacturers provides insights into innovative techniques like how do you manufacture steel wire? This collaboration can lead to enhanced performance and durability in your final products.