Introduction
In the world of manufacturing, wire forming machines play a pivotal role in shaping stainless steel into versatile components used across various industries. Understanding the intricacies of these machines is crucial for businesses aiming to optimize their production processes and meet market demands. With the right knowledge, manufacturers can leverage custom wire forming techniques to create high-quality products that stand out in a competitive landscape.
Understanding Wire Forming Machines
Wire forming machines are specialized equipment designed to manipulate stainless steel wire into specific shapes and configurations through various processes, including bending, twisting, and cutting. These machines enable manufacturers to produce intricate designs with precision and efficiency, making them essential tools in modern fabrication. The wire forming process not only enhances productivity but also ensures consistency in quality across large production runs.
Importance of Leading Manufacturers
The market for stainless steel wire forming is populated by several key players whose innovations drive industry standards forward. Leading wire forming manufacturers invest heavily in technology and research to develop advanced machinery that improves performance and reduces waste during production. By choosing reputable manufacturers, businesses can ensure they are utilizing cutting-edge solutions that enhance their operational capabilities while maintaining high-quality output.
Overview of Stainless Steel Applications
Stainless steel applications span a wide range of sectors, from automotive components to architectural fittings, thanks to its durability and resistance to corrosion. Custom wire forming techniques allow for tailored solutions that meet specific requirements across these industries, ensuring that each application benefits from the unique properties of stainless steel. As demand grows for innovative designs and sustainable practices, understanding how stainless steel wire bending fits into this landscape becomes increasingly important.
Key Players in Wire Forming Machines
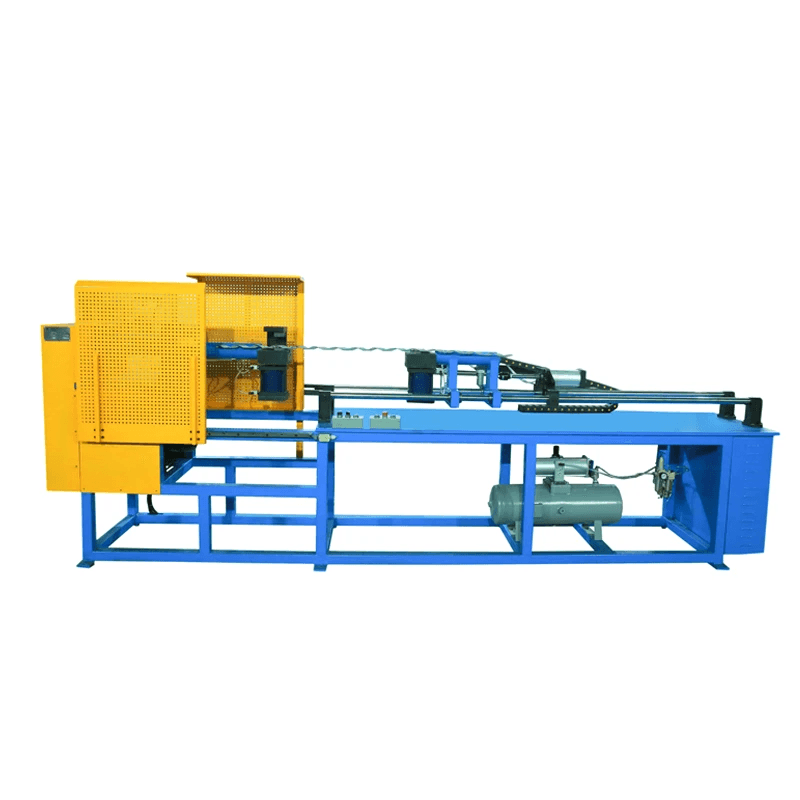
In the competitive landscape of wire forming machines, several manufacturers stand out for their innovation and expertise. These key players are not only shaping the wire forming process but also redefining the standards for stainless steel wire bending and custom wire forming. Understanding their contributions can provide valuable insights into the future of this industry.
Spark Fittings and Their Innovations
Spark Fittings has made impressive strides in stainless steel wire forming with its cutting-edge production line that includes a conveyor system paired with a high-speed integrated cutting machine. This innovative setup allows for efficient custom wire forming, enhancing productivity while maintaining precision in every bend and twist of stainless steel wire. With an emphasis on automation and speed, Spark Fittings is setting new benchmarks among leading wire forming manufacturers.
The tensioning drum within their conveyor system plays a crucial role in ensuring consistent tension during the wire forming process, which is vital for achieving high-quality results. Their commitment to innovation doesn't stop at machinery; it extends to customer service, where they actively seek feedback to refine their offerings further. By continuously evolving, Spark Fittings remains a top contender in the realm of stainless steel wire bending.
The Wire Forming Process Explained

The wire forming process is a meticulous journey that transforms raw stainless steel into precision-engineered components. Understanding this process is crucial for anyone looking to delve into custom wire forming, as it involves various stages that ensure the final product meets industry standards and client specifications. Leading wire forming manufacturers have honed these steps to maximize efficiency and quality, setting the stage for innovative applications.
Steps in Custom Wire Forming
Custom wire forming begins with selecting the appropriate stainless steel material, which is vital for achieving durability and performance. The next step involves cutting the wire to precise lengths before it's fed into specialized wire forming machines designed to shape it according to specific requirements. Once the initial shaping is complete, further processes like bending and twisting may be employed, ensuring that each piece meets its intended design while maintaining structural integrity.
Techniques in Stainless Steel Wire Bending
Stainless steel wire bending employs several techniques tailored to different applications and specifications. Common methods include rotary bending, where a rotating tool shapes the wire around a fixed point, and coiling, which creates loops or spirals in the material. These techniques are essential for producing complex geometries that are often required in custom wire forming projects, allowing manufacturers to meet diverse client needs with precision.
The Role of Technology in Production
Technology plays a pivotal role in streamlining the stainless steel wire forming process by enhancing accuracy and reducing production time. Advanced machines equipped with automation capabilities allow for high-speed operations without compromising on quality; this is particularly evident in systems like those used by Spark Fittings, which integrate conveyor systems with high-speed cutting machines for seamless production flows. As leading wire forming manufacturers continue to adopt innovative technologies, we can expect even greater advancements that will redefine efficiency standards across industries.
Spotlight on Spark Fittings
Spark Fittings has made significant strides in the world of stainless steel wire forming, particularly with their innovative 16A Pre-Twisted Wire Automatic Forming Production Line. This advanced system streamlines the wire forming process, ensuring precision and efficiency in every twist and bend. By leveraging state-of-the-art technology, Spark Fittings stands out among leading wire forming manufacturers.
16A Pre-Twisted Wire Automatic Forming Production Line
The 16A Pre-Twisted Wire Automatic Forming Production Line is a game-changer in custom wire forming applications. This production line integrates a conveyor system with a tensioning drum that ensures consistent material flow while minimizing downtime. Coupled with a high-speed integrated cutting machine, it enhances the overall efficiency of stainless steel wire bending operations by reducing cycle times and improving product quality.
This sophisticated setup allows for seamless transitions between different stages of the wire forming process, catering to diverse customer needs. The automation involved means less manual intervention, which not only speeds up production but also reduces the likelihood of human error. As a result, Spark Fittings can deliver high-quality products that meet stringent industry standards while maintaining competitive pricing.
Conveyor Systems and Their Advantages
Conveyor systems play an essential role in enhancing the efficiency of stainless steel wire forming processes at Spark Fittings. With features like adjustable speed controls and automated tension management, these systems ensure that materials are handled smoothly throughout production stages. This reduces wear and tear on equipment while optimizing workflow for custom wire forming tasks.
Moreover, conveyor systems minimize bottlenecks commonly associated with manual handling or outdated machinery. By allowing for continuous movement of materials from one point to another, they facilitate quick adjustments to production schedules based on demand fluctuations. Consequently, leading wire forming manufacturers like Spark Fittings can adapt swiftly to changing market conditions without sacrificing quality or output.
High-Speed Integrated Cutting Machine Benefits
The high-speed integrated cutting machine is another standout feature of Spark Fittings' production line that significantly enhances stainless steel wire bending capabilities. Designed for precision cutting at remarkable speeds, this machine ensures clean cuts that reduce waste material and improve overall product yield during the custom wire forming process.
Additionally, its integration into the existing conveyor system allows for real-time adjustments based on operational requirements—an invaluable asset when dealing with complex designs or varying lengths of materials. The combination of speed and accuracy positions Spark Fittings as a frontrunner among wire forming manufacturers striving for excellence in their offerings.
With these innovations at play, it's clear that Spark Fittings is committed to pushing the boundaries of what’s possible in stainless steel wire forming technology.
Comparison of Leading Wire Forming Manufacturers
In the competitive landscape of wire forming, understanding the offerings and capabilities of leading manufacturers is crucial. This section delves into how these companies differentiate themselves through their product lines, quality assurance practices, and customer satisfaction metrics. By examining these factors, businesses can make informed decisions when selecting a partner for their stainless steel wire forming needs.
Product Offerings and Versatility
Leading wire forming manufacturers showcase an impressive array of products tailored to various industries. From specialized stainless steel wire bending equipment to custom wire forming solutions, each manufacturer presents unique features that cater to specific applications. For instance, Spark Fittings stands out with its innovative production line that integrates conveyor systems with high-speed cutting machines, enhancing efficiency in the wire forming process.
Versatility is a hallmark of successful manufacturers; they often provide machines capable of handling diverse materials beyond stainless steel. This adaptability allows businesses to pivot quickly in response to market demands while ensuring high-quality output in custom wire forming projects. Moreover, the ability to accommodate different sizes and shapes enhances their appeal across numerous sectors.
Quality Assurance Measures
Quality assurance is paramount in the world of wire forming machines; it directly impacts product reliability and customer trust. Leading manufacturers implement rigorous testing protocols throughout the manufacturing process to ensure that every piece of equipment meets industry standards for performance and safety. For example, companies like KUKA Robotics emphasize precision engineering in their stainless steel wire bending technologies, which are subjected to extensive quality checks before reaching customers.
Additionally, many manufacturers adopt ISO certification processes that further reinforce their commitment to quality assurance measures. These certifications not only enhance operational efficiency but also provide customers with confidence in the durability and effectiveness of the machinery they invest in for custom wire forming applications. By prioritizing quality at every stage—from design through production—manufacturers can significantly reduce defects and improve overall customer satisfaction.
Customer Feedback and Satisfaction
Customer feedback serves as a vital indicator of a manufacturer's performance and reliability within the industry. Leading wire forming manufacturers actively seek input from clients regarding their experiences with products like stainless steel wire forming machines or custom solutions tailored for specific projects. This ongoing dialogue helps companies refine their offerings while addressing any concerns promptly.
Positive testimonials often highlight key aspects such as machine efficiency during the wire forming process or exceptional support services provided post-purchase. Manufacturers who prioritize customer satisfaction tend to cultivate long-term relationships with clients by consistently delivering on promises regarding product versatility and quality assurance measures. As a result, satisfied customers often become repeat buyers who advocate for these brands within their networks.
Future Trends in Wire Forming Technology
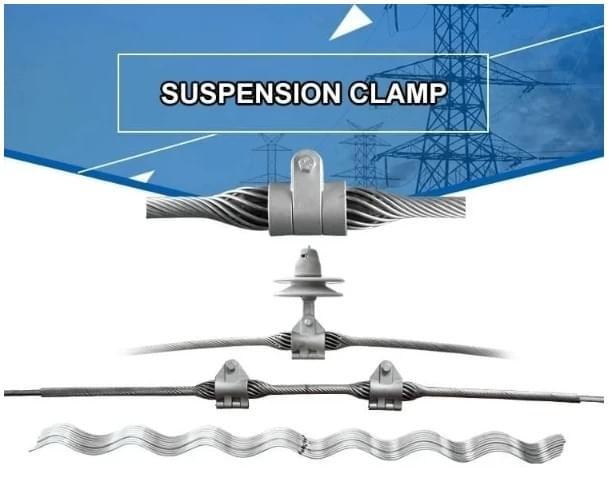
The wire forming industry is on the brink of transformation, driven by advancements in technology and changing market needs. As manufacturers look to enhance efficiency and reduce costs, automation in wire forming machines is becoming a focal point. This shift not only streamlines the stainless steel wire forming process but also elevates the quality and precision of products.
Automation in Wire Forming Machines
Automation is revolutionizing the way wire forming manufacturers operate, introducing high-speed production capabilities that were previously unimaginable. By integrating automated systems into stainless steel wire bending processes, companies can significantly increase output while minimizing human error. This technological leap allows for custom wire forming solutions that cater to diverse client needs without compromising on quality.
Leading wire forming manufacturers are investing heavily in automation technologies, which include advanced robotics and intelligent software systems. These innovations enable real-time monitoring and adjustments during the wire forming process, ensuring optimal performance at all stages of production. As a result, businesses can achieve higher efficiency levels while producing intricate designs with remarkable consistency.
Sustainability in Stainless Steel Wire Production
Sustainability has become a crucial concern across industries, and stainless steel wire production is no exception. Wire forming manufacturers are increasingly adopting eco-friendly practices to minimize their environmental footprint while meeting customer demands for responsible sourcing and manufacturing methods. This trend includes utilizing recyclable materials and implementing energy-efficient technologies within the wire forming machine operations.
Moreover, sustainable practices extend beyond material selection; they also encompass waste reduction strategies throughout the entire stainless steel wire bending process. By optimizing resource usage and recycling scrap material generated during custom wire forming projects, manufacturers contribute to a circular economy model that benefits both business and environment alike. The commitment to sustainability not only enhances brand reputation but also attracts environmentally conscious consumers.
Customization and Market Demands
In an era where personalization reigns supreme, customization has emerged as a key driver for growth among leading wire forming manufacturers. Clients increasingly seek tailored solutions that meet specific requirements for their projects—whether it’s unique designs or specialized dimensions in stainless steel wire products. This demand for customization necessitates advanced technology capable of adapting quickly to various design specifications within the wire forming process.
As market demands evolve rapidly, companies must remain agile and responsive to customer needs through innovative approaches to custom wire forming techniques. Incorporating flexible manufacturing systems allows businesses to pivot easily between different product lines without sacrificing quality or speed during production runs of stainless steel wires or components. Ultimately, meeting these expectations positions manufacturers competitively within an ever-changing landscape.
Conclusion
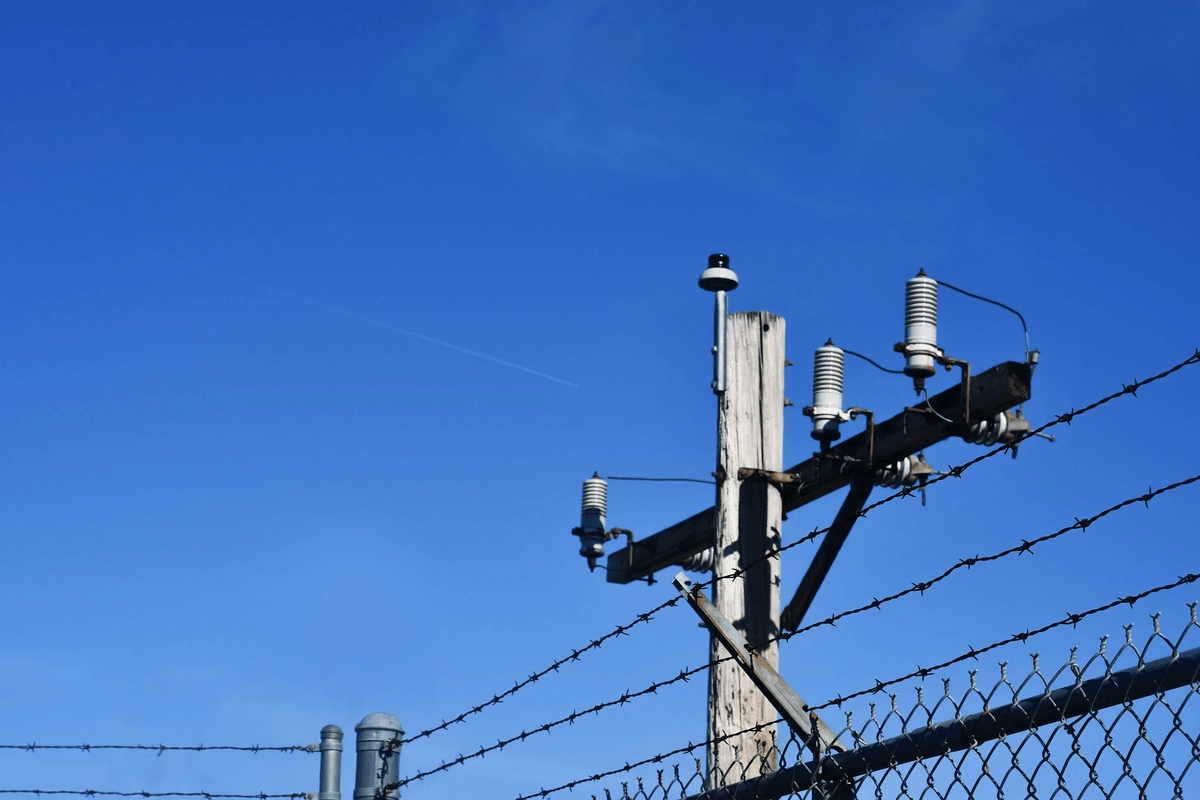
In the realm of stainless steel wire forming, technology plays an indispensable role in enhancing efficiency and precision. From the initial stages of the wire forming process to the final product, advanced machinery and automation have revolutionized how manufacturers approach custom wire forming. This evolution not only boosts productivity but also ensures that high-quality standards are consistently met.
The Role of Technology in Wire Forming
The integration of cutting-edge technology into stainless steel wire bending processes has transformed traditional methods into streamlined operations. Modern wire forming machines utilize sophisticated software and robotics, allowing for intricate designs that were once deemed impossible. This technological advancement not only reduces production time but also minimizes waste, making it a win-win for manufacturers and the environment alike.
Choosing the Right Manufacturer Matters
When it comes to selecting among leading wire forming manufacturers, several factors should be considered to ensure optimal outcomes for your projects. Quality assurance measures, customer feedback, and versatility in product offerings can significantly impact your choice in a manufacturer specializing in stainless steel wire forming. A reliable partner will not only understand your unique needs but will also provide innovative solutions that align with market demands.
Innovations Shaping the Future of Wire Forming
The future of custom wire forming is poised for remarkable innovations driven by automation and sustainability initiatives within the industry. As more companies adopt eco-friendly practices in stainless steel wire production, we can expect a shift towards materials and processes that prioritize environmental responsibility without sacrificing quality or performance. Moreover, customization will continue to be at the forefront as market demands evolve, pushing manufacturers to innovate continuously.