Introduction
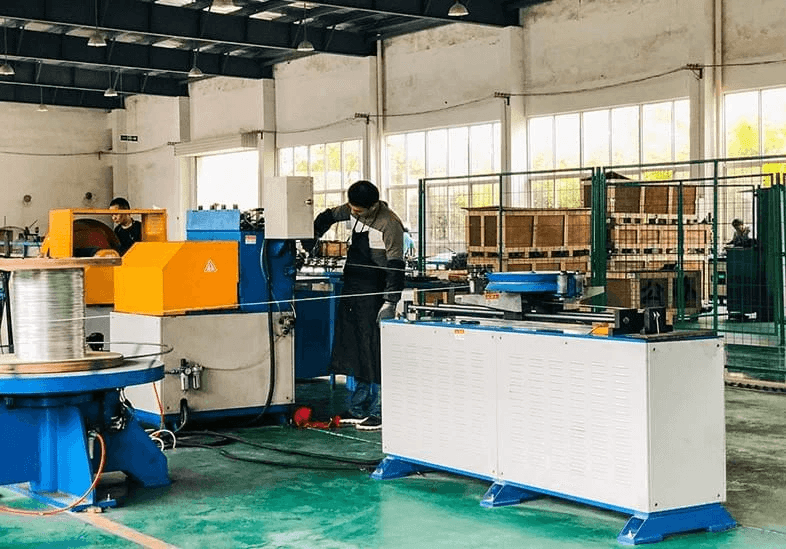
In the ever-evolving landscape of manufacturing, wire forming machines play a crucial role in shaping various metal components with precision and efficiency. These machines, particularly CNC wire forming technology, have revolutionized the way we approach metal forming processes. Understanding the intricacies of these technologies is essential for anyone looking to optimize their production capabilities.
Understanding Wire Forming Machines
Wire forming machines are specialized tools designed to manipulate wire into specific shapes and configurations, making them indispensable in numerous industries. They utilize advanced techniques to bend, twist, and shape wire into functional parts that serve various applications, from automotive components to intricate electronic devices. This versatility is what makes wire bending equipment a staple in modern manufacturing.
Importance of CNC Wire Forming
CNC (Computer Numerical Control) wire forming has taken traditional bending methods to new heights by offering unparalleled accuracy and repeatability in production runs. The automation provided by CNC wire bending machines reduces human error and enhances productivity, allowing manufacturers to meet stringent quality standards while minimizing waste. As industries demand higher precision and faster turnaround times, the importance of CNC wire forming continues to grow.
Overview of Spark Electronic Technology
Spark Electronic Technology stands at the forefront of innovation in the field of CNC wire forming machinery. With a focus on developing cutting-edge bending machines that incorporate advanced technology and user-friendly interfaces, Spark Electronic has made significant contributions to improving metal forming processes across various sectors. Their commitment to quality and performance ensures that businesses can rely on their wire bending equipment for all their manufacturing needs.
What is Wire Forming?
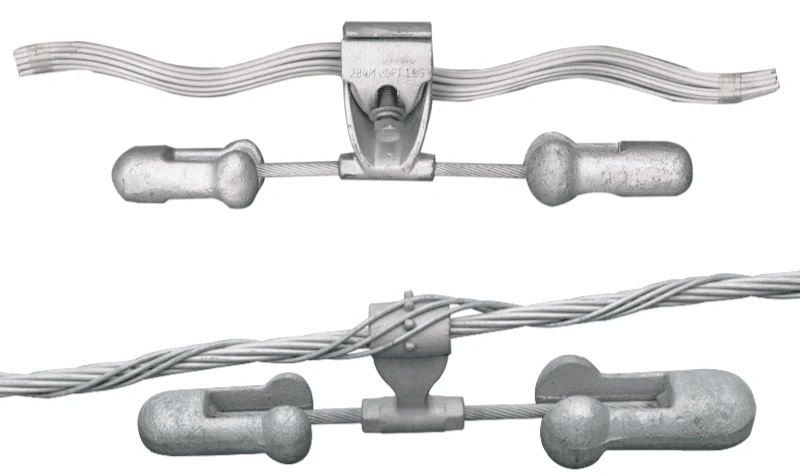
Wire forming is a crucial process in the metal forming industry, where wire is shaped into specific configurations for various applications. This technique involves bending, twisting, and cutting wire to produce components that are integral to numerous products and systems. With the advent of technology, particularly CNC (Computer Numerical Control) systems, wire forming has evolved into a highly precise and efficient operation.
Definition and Applications
At its core, wire forming refers to the manipulation of metal wire to create a desired shape or structure. This can encompass a wide range of applications including automotive parts, electronic components, and even decorative items. The versatility of wire forming makes it indispensable across industries such as construction, aerospace, and telecommunications.
Key Types of Wire Forming Machines
There are several types of machines used in the wire forming process, each designed for specific tasks within the broader category of bending equipment. CNC wire bending machines are particularly popular due to their ability to automate complex bends with high accuracy. Other key types include manual bending machines and specialized equipment tailored for unique shapes or sizes in metal forming.
Role in Metal Forming Industry
Wire forming plays an essential role in the metal forming industry by providing solutions that meet diverse manufacturing needs. It enables manufacturers to produce intricate designs that would be difficult or impossible with traditional machining methods alone. As industries continue to evolve towards more automated processes, CNC wire bending machines stand out as vital tools that enhance productivity while maintaining quality standards in production processes.
The Mechanics Behind CNC Wire Forming
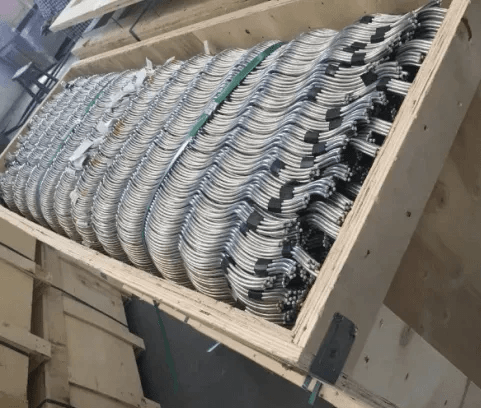
CNC wire forming is a fascinating blend of technology and artistry, where precision meets creativity in the world of metal forming. At its core, this process utilizes advanced computer numerical control (CNC) technology to automate the bending and shaping of wire into intricate designs. This innovation not only enhances productivity but also ensures that each piece meets stringent quality standards, making CNC wire bending machines essential in various industries.
CNC Technology Explained
CNC technology revolutionizes how we approach manufacturing by allowing for precise control over machinery through programmed commands. In the realm of wire forming, this means that a bending machine can be programmed to execute complex shapes with remarkable accuracy and repeatability. By using CAD (Computer-Aided Design) software, engineers can create detailed designs that are seamlessly translated into actual products by the CNC wire bending machine.
This level of automation reduces human error significantly, which is crucial when dealing with intricate components in metal forming applications. Moreover, CNC systems can store multiple programs, enabling manufacturers to switch between different projects quickly without sacrificing quality or efficiency. As a result, businesses can adapt to changing market demands while maintaining consistent output from their bending equipment.
Bending Machines and Their Functions
Bending machines come in various configurations tailored for specific tasks within the wire forming process. These machines typically utilize either rotary or linear motion to manipulate wires into desired shapes, depending on the complexity of the design being produced. For instance, some advanced models employ multiple axes of movement to achieve intricate bends that would be impossible with manual methods.
The versatility of modern bending equipment allows it to handle different materials and thicknesses without compromising performance. Additionally, many machines are equipped with features like automatic feeding systems and integrated inspection tools to streamline production further and ensure top-notch quality control during metal forming operations. This multifaceted functionality makes them indispensable for industries ranging from automotive to aerospace.
Benefits of CNC Wire Bending Machines
Investing in a CNC wire bending machine offers numerous advantages that extend beyond mere efficiency gains; it also enhances product quality and reduces waste significantly. With precise programming capabilities, these machines minimize material waste by optimizing cutting paths and reducing scrap during production runs—a win-win for both cost savings and environmental sustainability.
Moreover, the ability to produce complex shapes consistently means manufacturers can meet increasingly demanding specifications without extensive rework or delays in delivery timelines. This reliability builds trust with clients who depend on high-quality components for their own products in electrical transmission or other sectors utilizing wire forming techniques. Ultimately, embracing CNC technology empowers businesses not only to stay competitive but also to innovate continuously within their respective markets.
Exploring Wire Bending Equipment
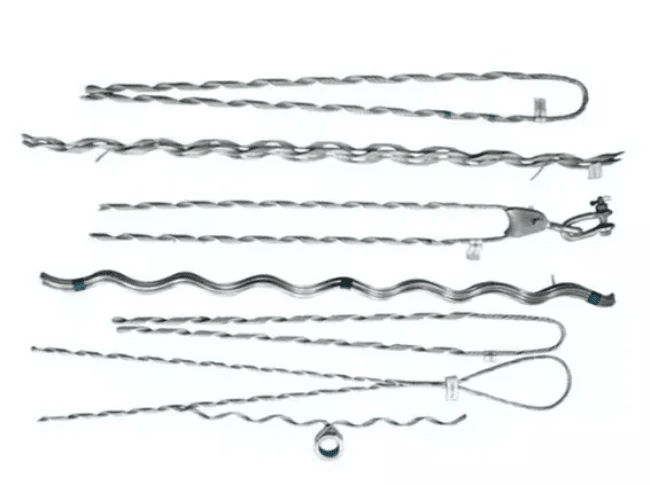
Wire bending equipment is the backbone of the wire forming industry, playing a crucial role in producing intricate shapes and components from metal wire. From simple bends to complex geometries, the right bending machine can elevate production efficiency and precision. Understanding the different types of wire bending machines available allows manufacturers to make informed decisions tailored to their specific needs.
Different Types of Wire Bending Equipment
When it comes to wire bending equipment, there are several types designed for various applications in metal forming. Manual wire benders are great for small-scale projects or prototypes where flexibility and quick adjustments are necessary. On the other hand, CNC wire bending machines offer automation and precision, making them ideal for high-volume production runs where consistency is key.
CNC wire forming technology has revolutionized how we approach complex designs, with machines capable of executing intricate bends that would be nearly impossible with manual methods. Additionally, there are hybrid models that combine both manual and CNC features, catering to businesses that require versatility without sacrificing quality. Understanding these options helps manufacturers select the best fit for their operational needs.
Features of High-Quality Machines
High-quality wire bending machines boast a variety of features designed to enhance performance and user experience in the metal forming process. Look for machines equipped with advanced software that allows for easy programming and modifications; this can significantly reduce setup time when switching between different projects or designs. Moreover, robust construction materials ensure durability while maintaining precision during operation.
Another critical feature is tooling versatility; high-quality CNC wire bending machines often come with interchangeable tools that enable them to handle different sizes and types of wires efficiently. An intuitive user interface also plays a significant role in simplifying operations—after all, no one wants to wrestle with complicated controls when they could be focusing on creativity instead! Investing in top-notch equipment ultimately leads to better product quality and increased productivity.
Comparisons of Manual vs. CNC Bending
The debate between manual versus CNC bending often boils down to efficiency versus control in the world of wire forming processes. Manual bending equipment offers greater tactile feedback and flexibility—ideal for custom jobs or small batches where each piece may require unique adjustments or techniques. However, this method can be labor-intensive and prone to human error over time.
Conversely, CNC wire bending machines shine when it comes to large-scale production runs requiring uniformity across thousands of pieces—each bend executed flawlessly according to precise specifications stored within their software systems. The initial investment may be higher than manual alternatives, but businesses often find that they recoup costs through increased speed and reduced wastage over time due to enhanced accuracy in their metal forming processes.
In conclusion, understanding both manual and CNC options empowers manufacturers choosing suitable wire bending equipment tailored specifically towards their operational goals while balancing cost-effectiveness against quality output demands.
Spark Electronic’s Innovations
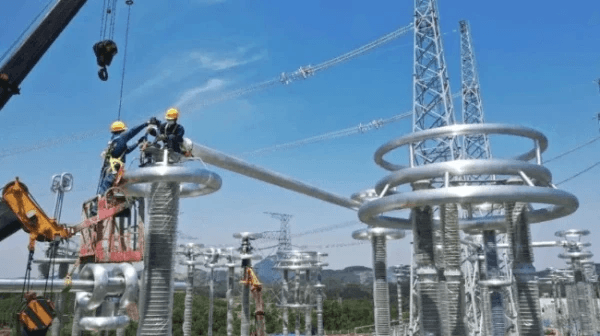
In the dynamic world of metal forming, Spark Electronic has emerged as a leader in the development of cutting-edge technology for wire forming applications. Their focus on innovation has led to significant advancements in CNC wire forming processes, allowing manufacturers to produce intricate components with remarkable precision and efficiency. By integrating state-of-the-art bending machines with robust software solutions, Spark Electronic is redefining the standards in wire bending equipment.
Overview of Spark Electronic Technology
Spark Electronic’s technology is at the forefront of revolutionizing how industries approach wire forming and bending tasks. Their CNC wire bending machines are designed for versatility, capable of handling various materials and shapes while ensuring high-quality output. This commitment to excellence not only enhances productivity but also significantly reduces waste, making it a sustainable choice for manufacturers engaged in metal forming.
Key Machines for Wire Forming
Among the standout offerings from Spark Electronic are their advanced wire bending machines that cater to diverse industrial needs. These machines incorporate sophisticated CNC technology that allows operators to execute complex designs effortlessly, enhancing both speed and accuracy in production processes. With features such as programmable controls and automated setups, these pieces of bending equipment ensure that every project meets stringent quality standards while maximizing operational efficiency.
Impact on Cable Accessories Manufacturing
The innovations brought forth by Spark Electronic have had a profound impact on cable accessories manufacturing, particularly through their specialized CNC wire forming solutions. By streamlining production processes with high-performance wire bending equipment, manufacturers can achieve greater consistency and reliability in their products. This not only boosts overall productivity but also elevates the quality assurance measures within electrical transmission applications, reinforcing confidence among end-users.
Applications in Electrical Transmission
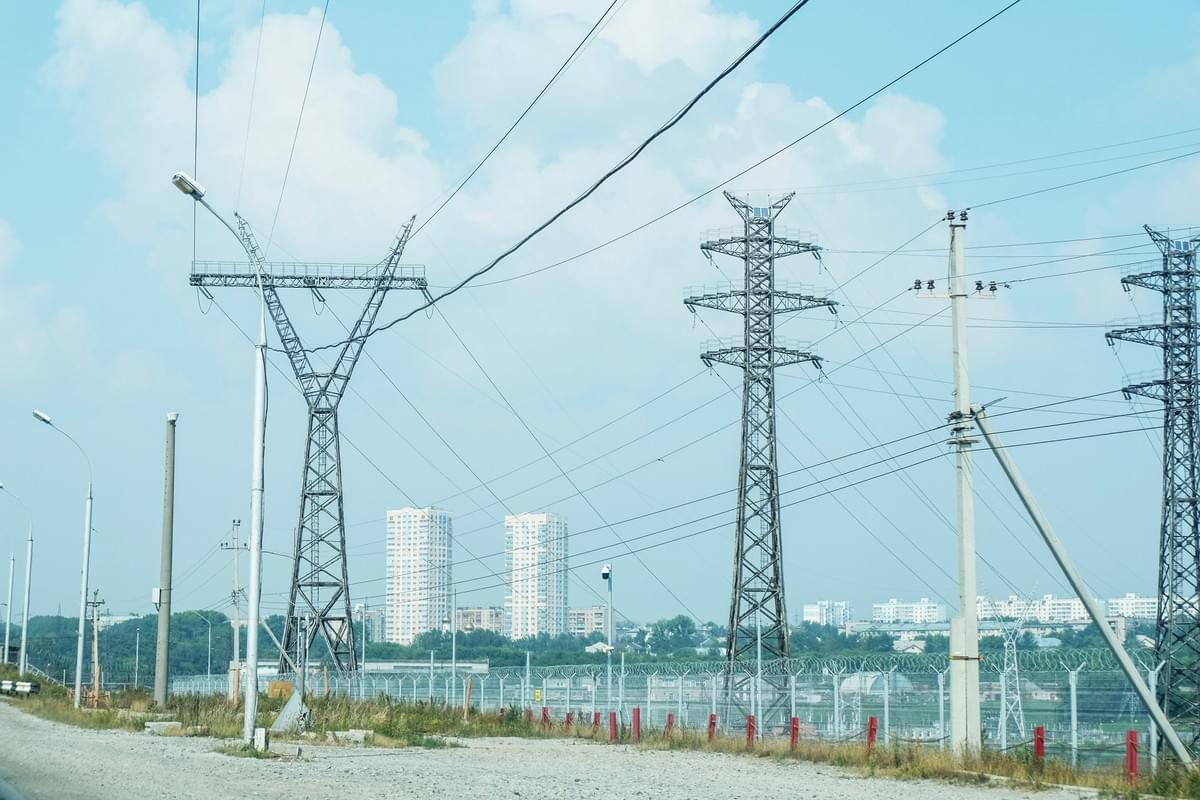
The applications of wire forming in electrical transmission are vast and vital, particularly in modern infrastructure. The use of CNC wire forming technology has revolutionized how components are produced for essential systems like ADSS (All-Dielectric Self-Supporting) cables and OPGW (Optical Ground Wire). These advanced wire bending machines ensure precision and reliability, which are crucial for maintaining the integrity of electrical transmission networks.
Use of Wire Forming in ADSS and OPGW
In the world of telecommunications and power distribution, ADSS and OPGW cables require specialized components that can withstand harsh environmental conditions while providing reliable performance. CNC wire bending machines play a pivotal role in creating these components with high accuracy, reducing the risk of failure during operation. The ability to form wires into complex shapes using advanced bending equipment allows manufacturers to produce parts that meet stringent industry standards.
Moreover, the flexibility offered by modern wire forming techniques enables engineers to customize solutions tailored to specific project requirements. By utilizing cutting-edge CNC technology, companies can efficiently produce large volumes of components without compromising quality or precision. This adaptability is essential for meeting the dynamic needs of the electrical transmission sector.
Importance in Electrified Railways
Electrified railways rely heavily on robust infrastructure that ensures safe and efficient operations. Here, wire forming is indispensable; it creates various components such as brackets, connectors, and support structures essential for overhead lines. The use of CNC wire bending machines allows manufacturers to produce these parts with unmatched accuracy, ensuring they can withstand high loads and environmental stresses.
Additionally, employing high-quality bending equipment enhances safety features within electrified rail systems by ensuring all components fit perfectly together. This precision reduces wear over time and minimizes maintenance costs associated with faulty parts or connections. Therefore, investing in advanced metal forming technologies not only improves operational efficiency but also contributes significantly to overall safety standards within railway systems.
Quality Assurance in Production Processes
Utilizing CNC wire forming ensures that each part meets rigorous specifications through automated processes that reduce human error significantly compared to manual methods. This level of quality control is critical when producing items such as connectors or supports used in sensitive applications like electrified railways or telecommunications.
Furthermore, regular inspections combined with state-of-the-art testing methods help maintain high standards throughout production runs involving bending equipment like CNC wire bending machines. Manufacturers who prioritize quality assurance not only protect their reputation but also enhance their competitiveness by delivering reliable products consistently across various industries involved in electrical transmission projects. Ultimately, investing in robust quality practices ensures that every piece produced contributes positively toward operational success.
Conclusion
In the world of metal forming, wire forming techniques stand out as essential processes that drive innovation and efficiency. The evolution of CNC wire forming has revolutionized how we approach bending equipment, allowing for precision and consistency that manual methods simply cannot match. As industries continue to demand higher quality and faster production, understanding these techniques becomes increasingly crucial.
Recap of Wire Forming Techniques
Wire forming encompasses a variety of methods used to shape metal into specific forms, with applications ranging from automotive parts to intricate electronic components. The introduction of CNC technology into wire bending has made it possible to achieve complex shapes with remarkable accuracy, enhancing the capabilities of traditional bending machines. By employing advanced CNC wire bending machines, manufacturers can streamline their processes while ensuring high-quality output that meets rigorous standards.
Future Trends in CNC Wire Bending
Looking ahead, the future of CNC wire bending is poised for exciting advancements driven by automation and smart technology integration. As manufacturers increasingly adopt AI-driven systems and IoT connectivity, we can expect more efficient operations and improved machine performance in the realm of wire bending equipment. Additionally, sustainability will play a vital role in shaping new innovations in metal forming practices as industries strive to reduce waste and energy consumption.
Why Choose Spark Electronic for Your Needs
When it comes to investing in reliable wire bending machines, Spark Electronic stands out as a leading choice for businesses seeking cutting-edge technology and exceptional support. Their commitment to developing high-quality CNC wire forming solutions ensures that clients receive equipment tailored to their specific needs while benefiting from years of industry expertise. By choosing Spark Electronic, you not only gain access to top-tier products but also partner with a company dedicated to pushing the boundaries of what’s possible in metal forming.