Introduction
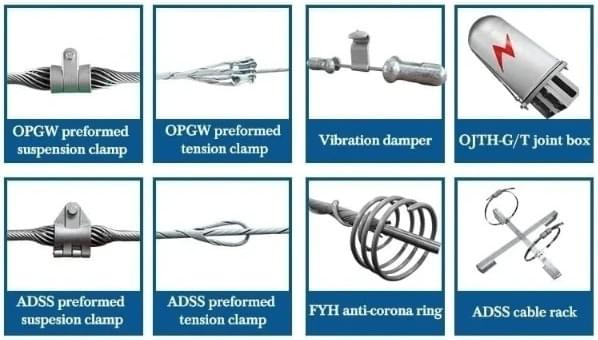
In the world of manufacturing and fabrication, wire bending machines play a crucial role in transforming raw materials into intricate shapes and designs. These machines are essential for industries ranging from automotive to construction, where precision and efficiency are paramount. With the evolution of technology, the rise of CNC wire benders has revolutionized how we approach wire forming tasks, making them faster and more accurate than ever before.
The Importance of Wire Bending Machines
Wire bending machines are indispensable tools that allow manufacturers to create complex wire forms with ease. They enable the production of a wide variety of products, from simple brackets to elaborate frames, showcasing their versatility in wire for bending applications. As industries demand higher quality standards and faster turnaround times, investing in advanced wire bending equipment becomes not just beneficial but essential for staying competitive.
Benefits of CNC Wire Benders
CNC wire benders offer numerous advantages over traditional manual methods, primarily through their ability to automate processes that once required significant labor input. These machines enhance precision in forming wire shapes while drastically reducing human error—an important factor when dealing with intricate designs. Furthermore, the speed at which a CNC wire bending machine operates means that businesses can meet tight deadlines without compromising on quality.
Overview of High-Performance Equipment
High-performance equipment in the realm of wire bending is characterized by its ability to deliver exceptional results consistently. This includes features such as advanced software integration for better control over operations and enhanced capabilities for handling various types of materials used in wire forming tasks. By utilizing cutting-edge technology found in modern wire bending equipment, manufacturers can maximize productivity while minimizing waste—a win-win scenario for any operation.
Types of Wire Bending Machines
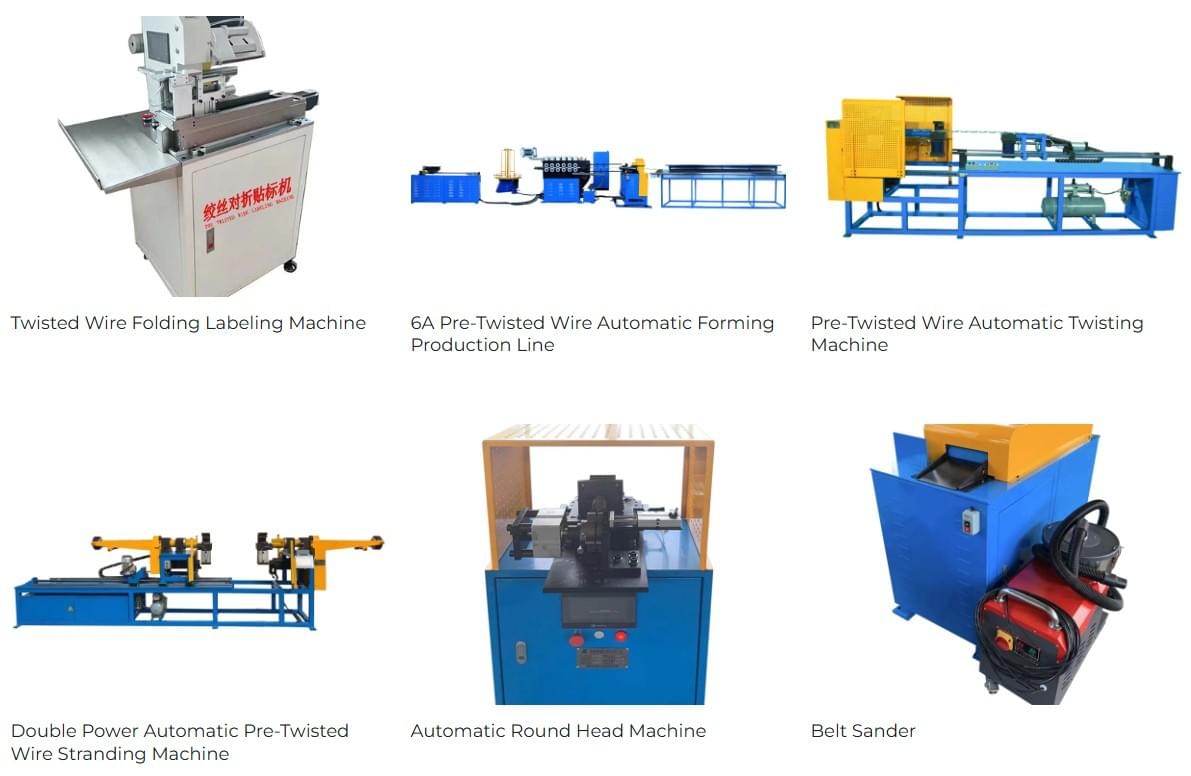
Exploring CNC Wire Benders
CNC wire benders are at the forefront of modern manufacturing, offering unparalleled precision and efficiency in the bending process. These machines utilize computer numerical control technology, allowing operators to create complex shapes and forms with ease. With a CNC wire bending machine, you can expect consistent quality in your products while significantly reducing the time spent on setup and adjustments.
One of the standout features of CNC wire benders is their ability to handle various types of wire for bending, including stainless steel, aluminum, and copper. This versatility makes them ideal for industries ranging from automotive to aerospace where accuracy is paramount. As a result, investing in high-quality CNC wire bending equipment can lead to substantial long-term savings by minimizing waste and maximizing output.
Manual vs. Automated Bending Equipment
While CNC machines dominate the market with their advanced capabilities, manual bending equipment still holds its place in many workshops around the world. Manual machines offer hands-on control that some operators prefer when working with simpler designs or smaller production runs. However, they often require more skill and experience to achieve consistent results compared to automated solutions like a CNC wire bender.
On the other hand, automated bending equipment streamlines operations by reducing labor costs and increasing throughput rates. These machines are particularly beneficial for high-volume production environments where speed is critical without sacrificing quality in forming wire shapes. Ultimately, choosing between manual and automated options depends on your specific requirements—whether you value precision or prefer tactile control.
Specialty Wire Forming Solutions
In addition to standard CNC wire benders and manual equipment, specialty wire forming solutions cater to niche markets with unique needs. These machines can produce intricate designs that might not be feasible with traditional methods or general-purpose equipment. For example, some specialty machines focus on creating bespoke components like springs or brackets that require specific bends and angles.
Moreover, advancements in technology have led to innovative solutions that combine multiple functionalities into one machine—think of it as a Swiss Army knife for metalworking! These multi-purpose units not only save space but also enhance efficiency by allowing seamless transitions between different tasks within your production line. Investing in specialty wire forming solutions could give your business an edge over competitors by expanding your capabilities beyond standard offerings.
Key Features of High-Performance Machines
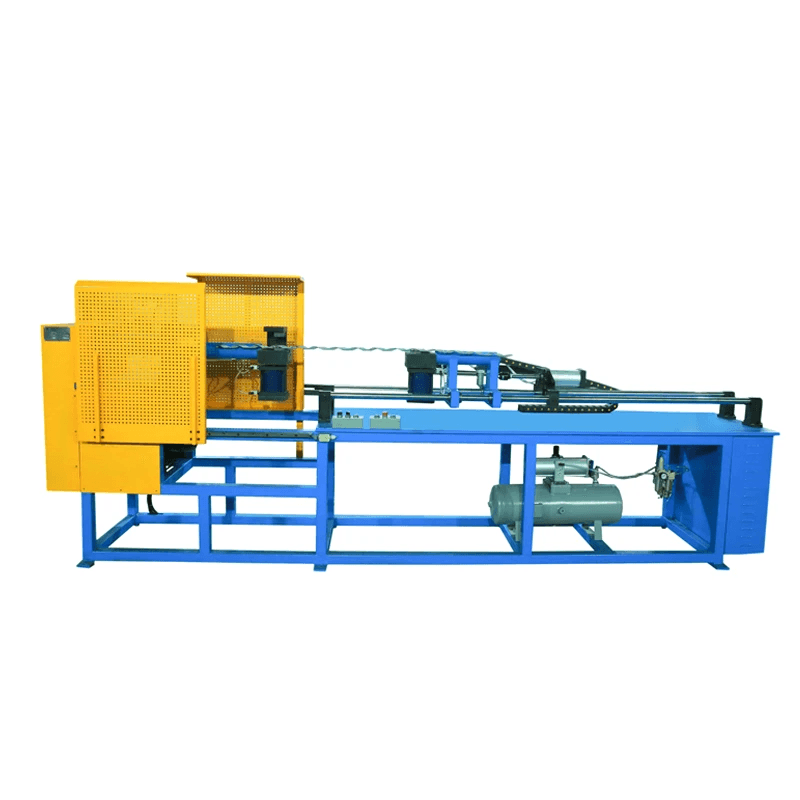
In the world of wire bending, high-performance machines stand out for their ability to deliver exceptional results. These machines are designed not just for functionality but also for precision, speed, and versatility. When considering a CNC wire bender or other bending equipment, understanding these key features can make all the difference in your production process.
Precision and Accuracy in Wire Bending
High-performance CNC wire bending machines are equipped with advanced technology that ensures every bend is executed with pinpoint accuracy. This level of precision reduces waste and enhances the overall quality of the finished product, making it essential for industries that rely on intricate designs.
Moreover, accurate wire bending machinery minimizes human error, ensuring that each piece meets stringent specifications. With state-of-the-art sensors and feedback systems integrated into these machines, manufacturers can achieve consistent results across large production runs. Investing in a reliable wire bending machine means investing in quality assurance and customer satisfaction.
Speed and Efficiency of Wire Bending Equipment
In today's fast-paced manufacturing environment, speed is a critical factor that cannot be overlooked. High-performance bending equipment significantly reduces cycle times compared to traditional methods, allowing businesses to meet tight deadlines without sacrificing quality. The efficiency of a CNC wire bender means that more products can be produced in less time, maximizing output while minimizing labor costs.
Additionally, modern CNC wire bending machines often feature automation capabilities that streamline operations further. By reducing manual intervention during the forming process, manufacturers can enhance productivity while freeing up skilled workers for more complex tasks. The result? A smooth workflow where efficiency reigns supreme.
Versatility in Forming Wire Shapes
One of the standout features of high-performance wire bending equipment is its versatility in forming various shapes from different types of wires. Whether you need simple bends or complex geometries, advanced CNC technology allows operators to create a wide range of designs effortlessly. This adaptability makes CNC wire benders ideal for industries such as automotive manufacturing or custom furniture design where unique shapes are often required.
Furthermore, modern machines come equipped with software that allows users to quickly switch between different projects without extensive reconfiguration or downtime—talk about convenient! This versatility not only saves time but also enables manufacturers to respond swiftly to changing market demands or customer preferences with ease. Investing in versatile wire forming solutions opens up endless possibilities for creative design and innovation.
Notable Brands in the Industry
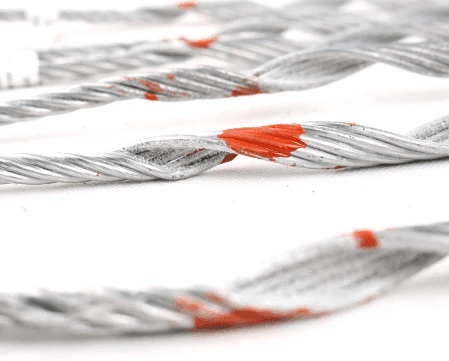
The wire bending industry is home to several notable brands that have made significant contributions to the development and innovation of bending equipment. These companies not only enhance the capabilities of wire forming but also set standards for precision and efficiency in the market. Let's delve into some of these key players and what they bring to the table.
Spark Fittings and Their Innovations
Spark Fittings has carved a niche for itself by pushing the boundaries of what's possible with their CNC wire bender technology. Known for their innovative designs, they specialize in creating custom solutions that cater to diverse industries ranging from automotive to aerospace. Their commitment to quality ensures that every piece of bending equipment produced meets stringent performance standards, making them a trusted name in wire forming.
Their latest models incorporate advanced features such as real-time monitoring and adaptive learning algorithms, which optimize the performance of their CNC wire bending machines. This means less downtime and more efficiency on production lines, allowing companies to produce complex shapes with ease. With Spark Fittings leading the charge, businesses can expect cutting-edge solutions that redefine what a wire bending machine can do.
Future of Technology with Akyapak
Akyapak stands at the forefront of technological advancements in wire bending equipment, consistently integrating state-of-the-art features into their machines. Their focus on automation has led to revolutionary changes in how wires are formed, significantly reducing labor costs while increasing output quality. Akyapak’s CNC wire bender models are particularly popular for their user-friendly interfaces and robust software integration capabilities.
What sets Akyapak apart is their vision for future developments; they are heavily investing in research and innovation to enhance machine intelligence further. By incorporating AI-driven analytics into their systems, they aim to minimize waste during production processes involving forming wire techniques. As industries evolve, Akyapak remains committed to providing high-performance machines that adapt seamlessly to changing manufacturing needs.
The Reliability of KUKA Robotics
Their CNC wire bending machines are engineered for durability and precision, making them ideal for high-volume production environments where every second counts. KUKA’s reputation is built on delivering consistent performance through advanced robotics technology integrated into their bending equipment.
The company’s emphasis on safety and operational efficiency means that users can rely on KUKA's machinery without fear of breakdowns or malfunctions during critical operations like forming wires or cutting processes. Furthermore, KUKA Robotics continuously updates its software solutions which allow clients easy access to real-time data analytics—empowering them with insights necessary for optimizing output from their wire bending machines effectively. In an industry where precision matters most, KUKA stands out as a beacon of reliability.
The 16A Pre-Twisted Wire Automatic Forming Production Line

The 16A Pre-Twisted Wire Automatic Forming Production Line is a game changer in the realm of wire bending equipment. This innovative system optimizes efficiency and precision, making it an essential tool for manufacturers looking to streamline their wire forming processes. By integrating advanced technology with user-friendly features, this production line sets a new standard for wire bending machines.
Features of the Conveyor System
One of the standout features of the conveyor system in the 16A production line is its ability to transport wire for bending seamlessly throughout the entire operation. This ensures that each segment of wire is precisely positioned for optimal performance, enhancing overall accuracy during the bending process. Moreover, the conveyor system is designed to minimize downtime, allowing for continuous operation and maximizing productivity in any manufacturing environment.
Benefits of the High-Speed Cutting Machine
The high-speed cutting machine integrated into this production line offers numerous benefits that significantly enhance productivity and efficiency. With rapid cutting capabilities, it allows operators to produce accurate lengths of wire quickly, reducing waste and improving turnaround times on projects involving complex wire forming tasks. Additionally, this machine's precision ensures uniformity across all pieces, which is crucial when working with CNC wire benders that require exact specifications.
Integration of Forming Machine with Tensioning Drum
Integrating a forming machine with a tensioning drum elevates the functionality of this automatic production line significantly. The tensioning drum maintains consistent tension on the wire during bending operations, ensuring that each curve and angle achieved by the CNC wire bending machine meets strict quality standards without compromising material integrity. This synergy not only enhances performance but also contributes to less scrap material—making it an eco-friendly choice in modern manufacturing practices.
Enhancing Production with Advanced CNC Technology
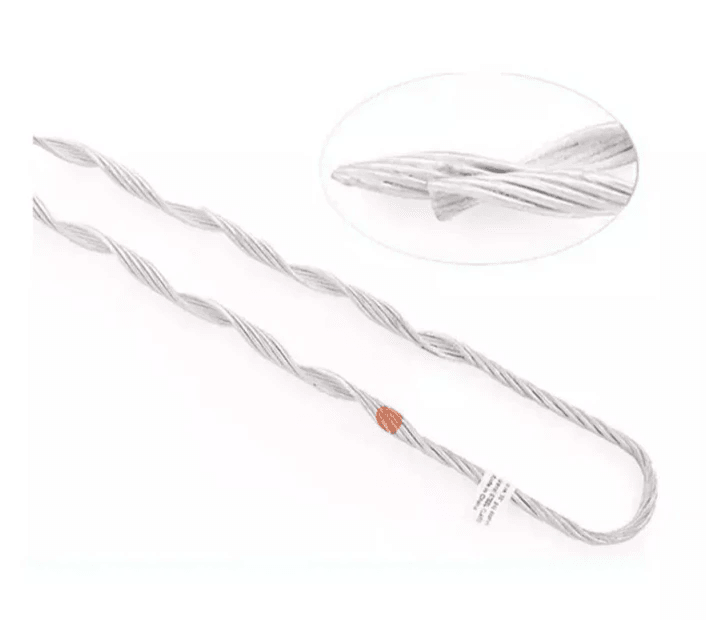
In today's fast-paced manufacturing environment, advanced CNC technology is revolutionizing the way we approach wire bending and forming wire. By integrating sophisticated software with CNC wire benders and other bending equipment, manufacturers can achieve unprecedented levels of control over their production processes. This not only streamlines operations but also enhances the overall efficiency of wire forming, making it a game changer in the industry.
Software Integration for Better Control
The integration of advanced software into CNC wire bending machines is like giving them a brain upgrade. This software allows operators to program complex designs and monitor every aspect of the bending process in real-time, ensuring precision that was previously unattainable. With enhanced control over parameters such as speed and angle, users can fine-tune their equipment to produce intricate shapes from wire for bending with minimal manual intervention.
Moreover, this software often includes features like predictive maintenance alerts, which help to prevent breakdowns before they occur. As a result, manufacturers can avoid costly downtime and ensure that their wire bending equipment operates at peak performance continuously. The ability to adapt quickly to design changes or production demands makes these machines indispensable in modern manufacturing.
Reducing Waste with Efficient Wire Forming
One of the most significant advantages of using CNC wire benders is their capacity to minimize waste during the forming process. Traditional methods often lead to excess scrap due to inaccuracies or inefficient cutting practices; however, advanced CNC technology optimizes every inch of material used in wire forming. By utilizing precise measurements and automated adjustments, these machines ensure that each piece of wire for bending is utilized effectively.
Additionally, efficient programming allows for nesting techniques that maximize material usage by arranging multiple parts within a single length of wire. This not only conserves resources but also contributes positively to a company's bottom line by reducing material costs significantly. In an era where sustainability is paramount, reducing waste through effective use of wire bending equipment aligns perfectly with eco-friendly manufacturing practices.
Real-World Applications of CNC Wire Benders
CNC wire benders are making waves across various industries thanks to their versatility and efficiency in producing complex shapes and designs from metal wires. From automotive components such as brackets and clips to aerospace applications where precision is crucial, these machines handle it all effortlessly. Their ability to create customized forms means they are essential tools for any manufacturer looking to innovate or streamline production processes.
Conclusion
As we wrap up our exploration of wire bending technology, it’s clear that the future holds exciting advancements for the industry. Innovations in CNC wire benders and other bending equipment promise to enhance precision and efficiency like never before. With a growing emphasis on automation and smart technology, manufacturers are gearing up for a new era of wire forming that will redefine production capabilities.
Future Trends in Wire Bending Technology
The landscape of wire bending technology is evolving rapidly, with trends pointing towards increased automation and integration of artificial intelligence. Future CNC wire bending machines are likely to incorporate advanced software solutions that allow for real-time adjustments, minimizing errors during the forming wire process. Moreover, sustainable practices will become crucial as manufacturers seek ways to reduce waste generated by traditional wire bending equipment.
Choosing the Right Bending Equipment
When it comes to selecting the right bending equipment, understanding your specific needs is paramount. Factors such as production volume, complexity of designs, and available budget should guide your decision-making process when investing in a CNC wire bender or any other type of wire bending machine. By thoroughly assessing these elements, you can ensure that your chosen machine enhances productivity while meeting your operational requirements.
Maximizing Efficiency with High-Performance Machines
To truly maximize efficiency with high-performance machines, integrating cutting-edge technology is essential. Utilizing CNC wire benders can streamline operations by reducing setup times and increasing output without compromising quality in forming wire shapes. Additionally, regular maintenance and training on advanced features will empower operators to get the most out of their wire bending equipment.