Introduction
In the intricate world of manufacturing, wire forming machinery plays a pivotal role in shaping metal wires into functional components used across various industries. These machines are essential for producing everything from automotive parts to electrical fittings, showcasing the versatility and importance of wire forming. Among the different types of machinery available, wire bending machines stand out as particularly crucial for creating precise bends and shapes in wire products.
What is Wire Forming Machinery
Wire forming machinery encompasses a range of equipment designed to manipulate metal wires into specific shapes and configurations. This category includes various types of machines, such as automated wire bending machines and specialized devices like Whitelegg machines. Essentially, wire forming is about taking raw materials and transforming them into useful components through innovative forming systems that ensure accuracy and efficiency.
Importance of Wire Forming in Industries
The significance of wire forming cannot be overstated; it underpins numerous sectors including automotive, aerospace, construction, and telecommunications. By utilizing advanced wire bending machines, manufacturers can produce high-quality components that meet stringent industry standards while optimizing production processes. This not only enhances product reliability but also contributes to cost-effectiveness by reducing waste and improving turnaround times.
Overview of Wire Bending Machines
Wire bending machines are at the heart of many manufacturing operations where precision is key. These machines come in both manual and automated forms, allowing for flexibility based on production needs. Automated wire bending machines have gained popularity due to their ability to consistently produce complex shapes with minimal human intervention—making them a favorite among companies looking to scale their operations efficiently.
Types of Wire Forming Machinery
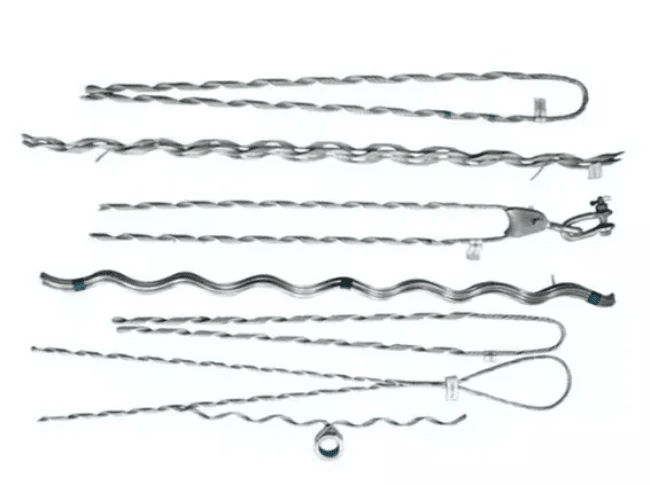
Wire forming machinery is a broad category that encompasses various machines designed to manipulate wire into specific shapes and forms. Among these, wire bending machines play a crucial role in producing components used across multiple industries. Understanding the different types of wire forming machinery, particularly wire bending machines and automated solutions, can help manufacturers choose the best equipment for their needs.
Wire Bending Machines Explained
Wire bending machines are specialized devices designed to bend wire into precise shapes according to specified dimensions. These machines utilize various forming systems that can produce intricate designs while maintaining accuracy and consistency. With advancements in technology, modern wire bending machines have become more versatile, allowing for the production of complex geometries with ease.
The core functionality of a wire bending machine involves clamping the wire securely while applying force to bend it at predetermined angles. This process is essential in industries such as automotive, aerospace, and construction, where custom-shaped metal components are often required. By employing different techniques such as rotary or linear bending, these machines ensure that manufacturers can meet diverse production demands efficiently.
Overview of Automated Wire Bending Machines
Automated wire bending machines represent the next step in manufacturing efficiency by incorporating advanced technologies like CNC (Computer Numerical Control). These automated systems enhance productivity by reducing manual labor and increasing precision in the bending process. Furthermore, they allow for rapid adjustments to design specifications without significant downtime.
One of the primary advantages of automated wire bending machines is their ability to handle large volumes of production with minimal human intervention. This not only speeds up manufacturing but also reduces errors associated with manual operation. As industries continue to seek ways to optimize processes and reduce costs, automated solutions have become increasingly popular among manufacturers looking for reliable performance.
Features of Whitelegg Machines
Whitelegg machines are well-regarded within the realm of wire forming machinery due to their robust design and innovative features tailored for high-quality output. Known for their reliability and versatility, Whitelegg offers a range of models suitable for various applications—from simple bends to complex configurations required in specialized sectors like telecommunications and power distribution.
These machines come equipped with user-friendly interfaces that allow operators to program intricate designs easily while ensuring precision throughout the manufacturing process. Additionally, Whitelegg's commitment to quality means that their equipment is built with durable materials capable of enduring heavy use without compromising performance over time. As a result, companies using Whitelegg machines can expect consistent results when producing components like those offered by Spark Fittings—specializing in preformed armor rods and tension clamps essential for electrical transmission systems.
How Wire Forming Machinery Works
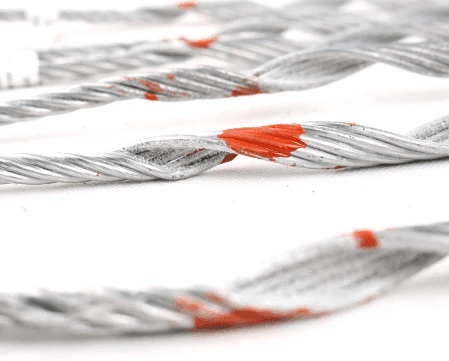
Understanding how wire forming machinery operates is crucial for industries that rely on precision and efficiency. Wire bending machines, such as those developed by Whitelegg machines, utilize various mechanisms to shape wire into desired forms. These forming systems are designed to accommodate different materials and specifications, ensuring versatility in production.
Mechanisms Behind Forming Systems
The core of any effective wire forming machinery lies in its mechanisms. Most wire bending machines employ a combination of rollers, guides, and clamps that work together to manipulate the wire accurately. These components allow for intricate designs and shapes to be achieved with minimal material waste, making them essential in production lines across various sectors.
Moreover, the mechanics involved in automated wire bending machines often include servo motors and pneumatic systems that enhance precision and speed. This automation not only streamlines the production process but also reduces human error, thereby increasing overall quality. Understanding these mechanisms provides insight into how manufacturers can optimize their operations using advanced wire forming technology.
The Role of CNC Technology
CNC (Computer Numerical Control) technology has revolutionized the way we approach wire forming machinery today. By integrating CNC systems into wire bending machines, manufacturers can achieve unparalleled accuracy while producing complex shapes effortlessly. This technology allows for easy programming of designs directly from CAD files, drastically reducing setup times compared to traditional methods.
Furthermore, CNC-enabled automated wire bending machines can handle multiple tasks simultaneously without sacrificing quality or speed. This capability is particularly beneficial for companies like Spark Fittings, which require high-quality preformed products for critical applications like electricity transmission and distribution. Ultimately, the role of CNC technology cannot be overstated; it enhances efficiency while maintaining stringent quality standards across various industries.
Typical Production Processes
The production processes involving wire forming machinery typically begin with raw material preparation followed by shaping and finishing stages. Initially, wires are cut to size before being fed into the bending machine where they undergo various manipulations based on design specifications. Automated processes ensure that each step—whether it's bending or coiling—is executed with precision.
After shaping the wires using advanced techniques found in Whitelegg machines or other automated options, finishing processes such as coating or welding may take place to enhance durability and functionality. These steps are crucial for industries requiring robust components capable of withstanding harsh conditions like electrified railways or power distribution networks handled by companies like Spark Fittings. Through these typical production processes, businesses can produce high-quality products efficiently while maximizing resource utilization.
Applications of Wire Forming Machinery
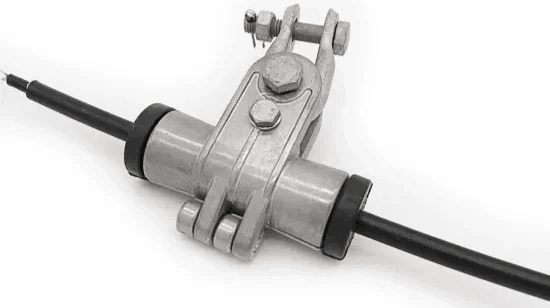
Wire forming machinery plays a vital role across various industries, providing essential components for numerous applications. From automotive to aerospace, the versatility of wire bending machines enables manufacturers to produce intricate parts that meet specific design requirements. Understanding the industries that rely on these machines highlights their significance in modern manufacturing processes.
Industries Using Wire Forming Equipment
Wire forming equipment is widely utilized in sectors such as automotive, construction, telecommunications, and electrical engineering. In the automotive industry, wire bending machines create components like brackets and clips that are crucial for vehicle assembly. Similarly, in construction and telecommunications, automated wire bending machines are employed to fabricate fixtures and supports that ensure structural integrity and reliable connectivity.
Furthermore, electrical engineering companies depend on wire forming machinery for producing connectors and fittings essential for power distribution systems. Whitelegg machines have gained popularity in this sector due to their precision and efficiency in creating complex shapes from wire materials. Ultimately, the diverse applications of wire forming machinery underscore its importance across various industrial domains.
Case Study: Spark Fittings Solutions
Spark Fittings is a leading company specializing in manufacturing equipment for preformed armor rods, tension clamps, and cable accessories tailored for ADSS (All-Dielectric Self-Supporting) and OPGW (Optical Ground Wire) applications. By utilizing advanced wire bending machines within their production lines, Spark Fittings ensures high-quality output while meeting the demands of electricity transmission and electrified railways. Their innovative use of automated wire bending machines allows them to enhance productivity while maintaining stringent quality standards.
The company’s commitment to excellence is evident in its ability to produce durable preformed products that withstand harsh environmental conditions. With a focus on customer satisfaction and efficiency, Spark Fittings showcases how effective wire forming machinery can lead to superior manufacturing outcomes across specialized industries. This case study illustrates not only the capabilities of modern forming systems but also the critical role they play in supporting infrastructure development.
Benefits of Wire Forming in Manufacturing
The benefits of using wire forming machinery are manifold; they significantly enhance production efficiency while ensuring precision in component manufacturing. Automated wire bending machines reduce labor costs by streamlining processes that would otherwise require extensive manual labor—saving both time and resources for manufacturers. Moreover, these machines improve accuracy by minimizing human error during production runs.
In addition to cost savings and improved accuracy, employing advanced forming systems enables manufacturers to achieve greater design flexibility when creating custom components tailored to specific needs or projects. This adaptability allows businesses to respond quickly to market changes or client requests without compromising quality or performance standards associated with traditional methods of production. Ultimately, investing in high-quality wire forming machinery leads not only to enhanced operational capabilities but also supports long-term growth strategies within competitive markets.
Choosing the Right Wire Bending Machine
Selecting the right wire bending machine is a pivotal decision for any manufacturing operation involving wire forming machinery. With various options available, it’s crucial to evaluate specific factors that align with your production needs and capabilities. Understanding the nuances between different machines can significantly impact efficiency, product quality, and overall operational costs.
Factors to Consider in Selection
When choosing a wire bending machine, consider the material type and thickness you will be working with, as these factors directly influence your machinery's performance. Additionally, assess the production volume required; high-volume operations may benefit from automated wire bending machines that enhance speed and precision. Don’t forget to factor in space requirements and compatibility with existing forming systems—ensuring seamless integration can save time and reduce costs in the long run.
Another key consideration is ease of use; user-friendly interfaces can minimize training time for operators and reduce errors during production runs. Maintenance requirements are also essential; selecting a machine with readily available parts can streamline repairs and keep downtime to a minimum. Finally, think about future scalability—investing in adaptable machinery ensures that your operations can grow without necessitating complete overhauls of your equipment.
Comparing Manual vs. Automated Options
When weighing manual versus automated options for wire bending machines, consider how each aligns with your production goals. Manual machines often provide greater flexibility for small-scale projects or unique designs but may require skilled operators who understand intricate techniques involved in wire forming machinery. In contrast, automated wire bending machines excel in high-volume settings where consistency and speed are paramount—think of them as the workhorses of modern manufacturing.
Automated options typically come equipped with advanced technology like CNC controls that enhance precision while reducing human error—a significant advantage when producing complex shapes or components consistently over time. However, this automation often comes at a higher initial investment compared to manual models, so it’s important to analyze your budget alongside projected output needs before making a decision on which type of wire bending machine suits you best.
Ultimately, both types have their merits; manual machines might be ideal for niche markets or bespoke projects while automated solutions cater well to large-scale production demands across various industries including those served by companies like Spark Fittings.
Top Manufacturers of Wire Forming Machinery
In the realm of wire forming machinery, several manufacturers stand out due to their innovative designs and reliable performance records. Whitelegg Machines is renowned for its robust offerings tailored specifically for diverse applications within this sector—they’ve carved out a niche by combining traditional craftsmanship with cutting-edge technology suitable for both small-scale operations and larger enterprises alike.
Other notable manufacturers include companies like KUKA Robotics known for their advanced automation solutions that integrate seamlessly into existing workflows while enhancing productivity levels significantly through state-of-the-art features found in their automated wire bending machines. Additionally, brands such as WAFIOS offer comprehensive support services alongside their equipment ensuring users get maximum value from their investments in forming systems.
Choosing from these top manufacturers provides not only quality equipment but also peace of mind knowing you're backed by industry leaders committed to innovation within the field of wire forming machinery.
Maintenance Tips for Wire Forming Equipment
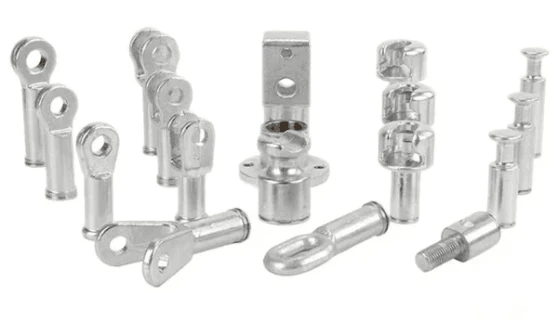
Maintaining wire forming machinery is not just about keeping the machines running; it’s essential for ensuring efficiency, safety, and longevity. Regular maintenance of wire bending machines can prevent costly breakdowns and improve the quality of the products being formed. By establishing a routine maintenance schedule, operators can address minor issues before they escalate into major problems.
Importance of Regular Maintenance
Regular maintenance is crucial for any piece of equipment, especially when it comes to complex systems like automated wire bending machines. These machines are integral to various manufacturing processes and play a significant role in production efficiency. Neglecting maintenance can lead to unexpected downtime, which not only affects productivity but also increases operational costs.
Moreover, well-maintained wire forming machinery ensures that products meet quality standards consistently. This is particularly important in industries where precision is key, such as in the production of components for Spark Fittings' preformed armor rods and tension clamps. Keeping your wire bending machine in top shape means fewer defects and higher customer satisfaction.
Common Issues and Fixes
Wire forming machinery can encounter several common issues that may hinder performance if not addressed promptly. One frequent problem with wire bending machines includes misalignment or wear on the forming systems, which can lead to inaccuracies in product dimensions. Regularly checking alignment settings and replacing worn parts can help mitigate these issues before they affect output quality.
Another common issue is electrical failures within automated wire bending machines due to dust accumulation or loose connections. Keeping electrical components clean and secure will minimize downtime caused by electrical malfunctions. Additionally, lubrication of moving parts is essential; neglecting this task may result in increased friction and premature wear on critical components.
Enhancing Lifespan of Wire Bending Machines
To enhance the lifespan of your wire bending machine, consider implementing a proactive approach to maintenance rather than a reactive one. This includes regular inspections that focus on both mechanical and electronic components—both are vital for optimal operation within forming systems like those found in Whitelegg machines. By catching potential issues early through routine checks, you’ll save time and money while extending the life of your equipment.
Investing in high-quality lubricants specific to your machinery type will also contribute significantly to longevity; proper lubrication reduces friction between moving parts that could otherwise lead to breakdowns over time. Furthermore, training staff on best practices for operating these sophisticated tools ensures they understand how their actions impact machine health—this knowledge pays dividends down the line.
In conclusion, maintaining your wire forming machinery through regular upkeep not only prevents breakdowns but also enhances overall productivity while ensuring high-quality outputs like those produced by Spark Fittings' innovative solutions.
Conclusion
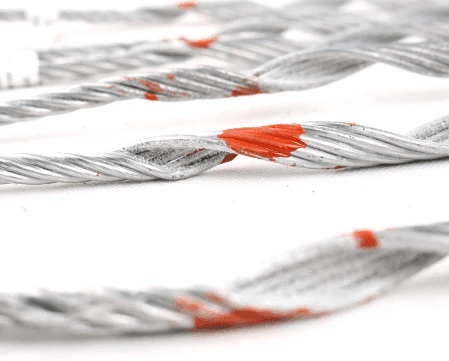
In wrapping up our exploration of wire forming machinery, it’s evident that this technology plays a pivotal role in modern manufacturing. The evolution of wire bending machines has not only enhanced production efficiency but also improved the precision and quality of wire products. As industries continue to demand more sophisticated solutions, the advancements in automated wire bending machines will undoubtedly shape the future landscape of manufacturing.
Future Trends in Wire Forming Technology
The future of wire forming technology is poised for exciting developments as industries embrace automation and smart manufacturing practices. Innovations such as AI-driven forming systems will likely enhance the capabilities of wire bending machines, allowing for real-time adjustments and increased productivity. Additionally, sustainability will play a crucial role; manufacturers are expected to focus on eco-friendly materials and energy-efficient processes in their wire forming machinery.
Innovations in Wire Bending Machines
Recent innovations have transformed traditional wire bending machines into highly efficient automated systems that can handle complex designs with ease. For instance, Whitelegg machines are at the forefront, integrating advanced CNC technology that enables precise control over every bend and twist in the wire. These innovations not only improve accuracy but also reduce production time significantly, making them indispensable tools for manufacturers seeking to stay competitive.
Final Thoughts on Wire Forming Machinery
Wire forming machinery has become an integral part of numerous industries, from automotive to telecommunications. The versatility and adaptability of these machines ensure they can meet diverse manufacturing needs while maintaining high standards of quality and efficiency. As we look ahead, it’s clear that ongoing advancements—particularly in automated wire bending machines—will continue to redefine what is possible in the realm of metal fabrication.