Introduction
In the bustling world of manufacturing, CNC wire bending has emerged as a pivotal technology, transforming the way we shape metal into practical and intricate designs. This evolution has not only enhanced production efficiency but also broadened the scope of applications for wire bending machines across various industries. As companies strive to meet increasing demands, understanding the nuances of these machines becomes essential for anyone looking to invest in or upgrade their fabrication capabilities.
The Evolution of CNC Wire Bending
The journey of CNC wire bending began with manual processes that required skilled labor and significant time investment. Over the years, technological advancements have led to the development of sophisticated CNC Wire Bending Machines that can bend and form wires with remarkable precision and speed. Today’s machines integrate software-driven controls and automation, allowing manufacturers to produce complex shapes with minimal human intervention while ensuring consistent quality.
What Makes a Great CNC Machine?
When evaluating CNC wire bending machine manufacturers, several key features distinguish an exceptional machine from a mediocre one. A great CNC Wire Bending Machine should offer versatility in handling various materials and thicknesses while maintaining accuracy in every bend. Additionally, user-friendly interfaces, robust construction, and efficient energy consumption are critical factors that contribute to overall performance and reliability in forming machines.
Leading Players in the Market
The market for wire bending machines is populated by several leading players who have carved out their niches through innovation and quality offerings. Companies like Spark Fittings stand out as innovators in wire forming technology, while Haco is known for its pioneering fabrication solutions that cater to diverse industrial needs. NKO has also gained recognition as masters of precision machinery, ensuring that customers receive top-notch equipment tailored to their specific requirements.
Overview of CNC Wire Bending Technology
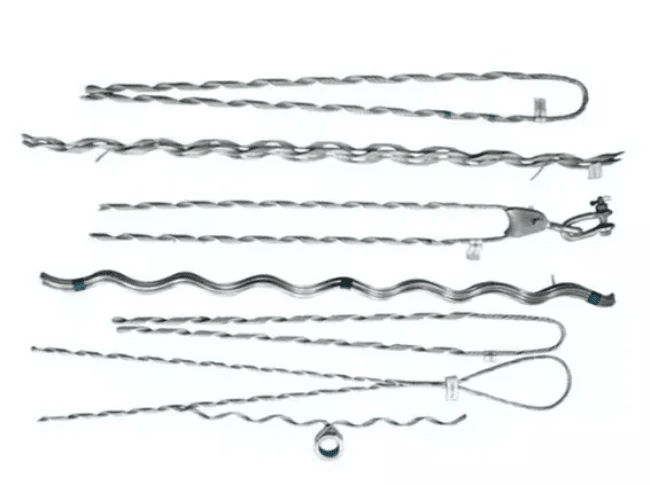
CNC wire bending technology has transformed the way manufacturers create complex wire forms and components. This advanced process utilizes computer numerical control (CNC) to accurately manipulate wire into desired shapes, allowing for high precision and repeatability. The evolution of CNC wire bending machines has led to increased efficiency, reduced waste, and the ability to produce intricate designs that were once labor-intensive or nearly impossible.
Understanding Wire Bending Processes
At its core, wire bending involves manipulating metal wires into specific shapes using various techniques. Traditional methods often relied on manual labor, but with the advent of CNC technology, these processes have become automated and streamlined. Different types of machines cater to various wire bending needs, including twisted wire folding labeling machines that specialize in creating unique labels while maintaining precision.
Understanding the nuances of these processes is crucial for selecting the right CNC wire bending machine for your needs. Each machine type offers distinct advantages based on factors like material compatibility and production volume. This knowledge can empower businesses to optimize their operations while minimizing costs associated with inefficient machinery.
Key Features of Modern CNC Machines
Modern CNC wire bending machines are equipped with a plethora of features designed to enhance performance and user experience. Among these key features are advanced software interfaces that allow operators to easily program complex bends and shapes without extensive technical knowledge. Additionally, many machines come with integrated safety systems that monitor operations in real-time to prevent accidents or malfunctions.
Another significant feature is the versatility offered by modern forming machines; they can handle a wide range of materials from soft aluminum wires to tougher stainless steel options. High-speed capabilities enable manufacturers to increase output without sacrificing quality, making these machines indispensable in competitive markets. Furthermore, connectivity options such as IoT integration allow for remote monitoring and diagnostics—an essential aspect in today's fast-paced manufacturing environments.
Applications of CNC Wire Bending
The applications for CNC wire bending technology are vast and varied across multiple industries. From automotive components like brackets and clips to medical devices requiring intricate designs, a wide array of products benefits from this technology's precision capabilities. Moreover, industries such as furniture design leverage custom bent wires for unique aesthetic elements that stand out in a crowded market.
CNC wire bending is not limited just to functional parts; it also plays a pivotal role in creating artistic installations where form meets function beautifully. Twisted wire folding labeling machines further expand applications by combining labeling functionalities directly into the manufacturing process—streamlining production while enhancing product identification efforts across sectors like retail packaging or logistics.
In summary, understanding the intricacies of CNC wire bending processes along with recognizing key features helps businesses make informed decisions when selecting machinery from reputable CNC wire bending machine manufacturers. As industries continue evolving towards automation and customization, embracing modern technologies will be crucial for staying competitive in an ever-changing market landscape.
Spotlight on Major Manufacturers

Spark Fittings: Innovators in Wire Forming
Spark Fittings has carved a niche for itself as one of the most innovative CNC wire bending machine manufacturers in the industry. Their advanced wire bending machines are designed with cutting-edge technology that enhances efficiency and precision in wire forming processes. Notably, their Twisted Wire Folding Labeling Machine exemplifies how Spark Fittings integrates automation with user-friendly design, making it easier for operators to achieve consistent results.
The company focuses on creating versatile forming machines that cater to various applications across multiple sectors. From automotive components to intricate decorative pieces, Spark Fittings ensures that their CNC Wire Bending Machines can handle diverse materials and complex designs seamlessly. With a commitment to continuous improvement and customer feedback, they remain at the forefront of technological advancements in wire bending.
Moreover, Spark Fittings emphasizes sustainability by incorporating energy-efficient features into their machines. This commitment not only benefits the environment but also helps customers reduce operational costs over time. As they continue to innovate and expand their product line, Spark Fittings solidifies its position as a leader among CNC wire bending machine manufacturers.
Analyzing the 16A Pre-Twisted Wire Automatic Forming Production Line
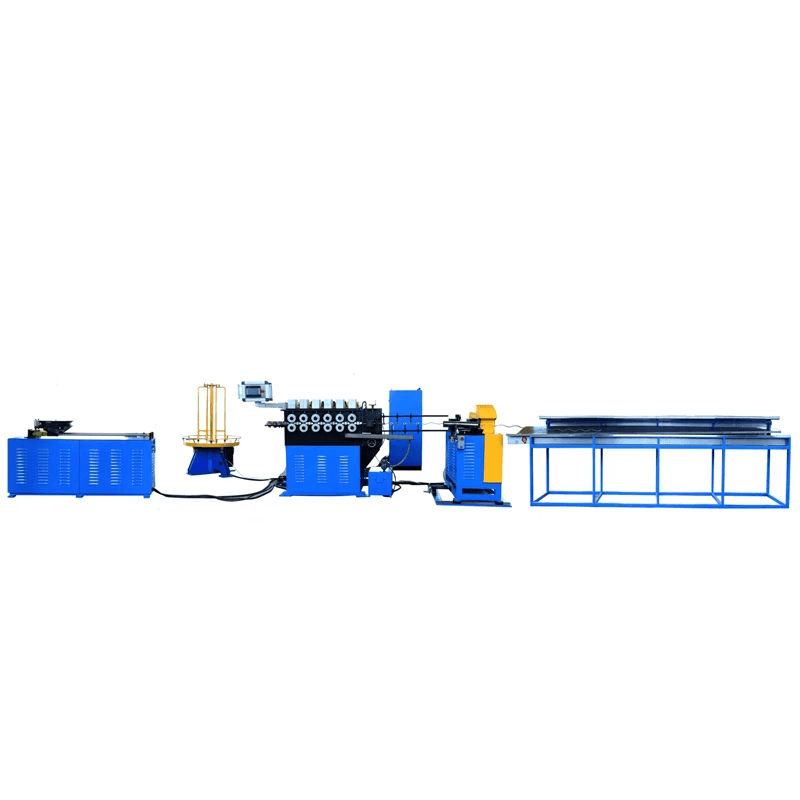
The 16A Pre-Twisted Wire Automatic Forming Production Line by Spark Fittings represents a significant leap in the world of CNC wire bending technology. This innovative solution is designed to enhance efficiency and precision in wire forming processes, catering to various industries that require intricate wire components. With its advanced features, this production line stands out among other offerings from leading CNC wire bending machine manufacturers.
Overview of Spark Fittings’ Solution
Spark Fittings has engineered the 16A Pre-Twisted Wire Automatic Forming Production Line with a focus on automation and user-friendliness. This CNC wire bending machine integrates seamlessly into existing manufacturing setups, allowing for rapid deployment without extensive downtime. The system's modular design ensures flexibility, enabling manufacturers to adapt it for different applications while maintaining high productivity levels.
Conveyor and Forming Machine Synergy
One of the standout aspects of this production line is its conveyor and forming machine synergy, which optimizes workflow efficiency. The conveyor system is meticulously designed to transport materials smoothly between stations, reducing bottlenecks and enhancing overall throughput. By synchronizing the movements of the twisted wire folding labeling machine with the forming machines, Spark Fittings ensures that each component is processed quickly and accurately, minimizing waste and maximizing output.
Benefits of High-Speed Integrated Cutting
High-speed integrated cutting is another hallmark feature of Spark Fittings' 16A production line that sets it apart from competitors in the market. This technology allows for precise cuts at remarkable speeds, enabling manufacturers to produce high volumes without sacrificing quality or accuracy. The combination of advanced cutting techniques with robust CNC wire bending machines results in a streamlined process that not only saves time but also reduces operational costs over time.
Comparative Review of Wire Bending Machines
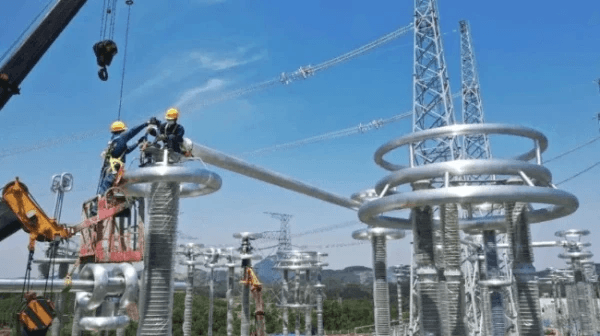
Performance Metrics to Consider
Performance metrics are essential when comparing wire bending machines from various CNC wire bending machine manufacturers. Key indicators include bending radius, cycle time, and repeatability; these determine how well a machine can perform under different conditions. Additionally, features like user-friendly interfaces and programmable settings enhance operational efficiency and ease of use for operators.
Another vital aspect is the machine's ability to handle different wire materials and sizes without compromising on quality or speed. A versatile CNC Wire Bending Machine that can adapt to various tasks will save both time and resources in the long run. Ultimately, investing in a machine with superior performance metrics translates into higher productivity levels for any manufacturing operation.
Cost-Effectiveness of Various Models
Cost-effectiveness is often a decisive factor when selecting a wire bending machine for your production line. While some high-end models boast advanced features and impressive specifications, their price tags may not always align with budget constraints or project requirements. Thus, it's essential to assess both initial investment costs and long-term operational expenses associated with maintenance and energy consumption.
Comparing models across different CNC wire bending machine manufacturers reveals that mid-range options often deliver solid performance at more manageable prices. These machines may lack some cutting-edge features but still provide reliable functionality for most applications without breaking the bank. By focusing on cost-effective solutions like forming machines tailored to specific needs, businesses can optimize their investments while maintaining quality outputs.
Customer Testimonials and Case Studies
Customer testimonials serve as invaluable resources for assessing the real-world performance of various wire bending machines available in the market today. Many users highlight their experiences with specific CNC Wire Bending Machines from reputable manufacturers; this feedback provides insights into reliability, ease of use, and overall satisfaction levels among operators. Case studies further illustrate how companies have successfully integrated these machines into their workflows to enhance productivity.
For instance, one case study showcases a manufacturer that adopted a Twisted Wire Folding Labeling Machine from a leading brand; they reported significant improvements in processing times while reducing labor costs considerably. Such success stories underline the importance of selecting reputable CNC wire bending machine manufacturers that prioritize innovation alongside customer service support post-purchase. Ultimately, positive testimonials help potential buyers make informed decisions based on real-world applications rather than mere marketing claims.
Trends Shaping the Future of Wire Bending
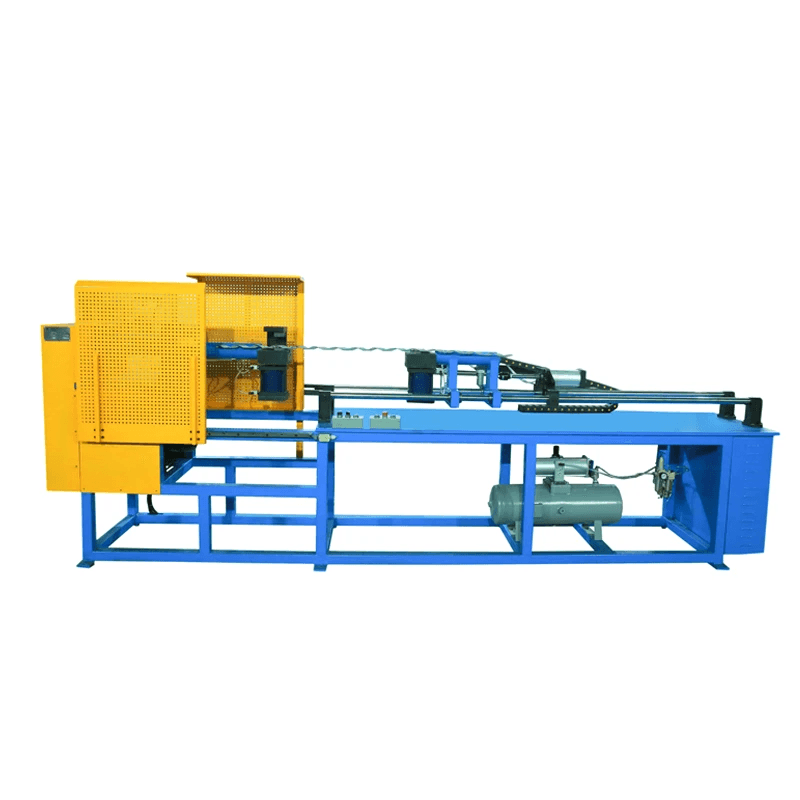
The landscape of wire bending is undergoing a radical transformation driven by technological advancements and market demands. CNC wire bending machine manufacturers are increasingly focusing on automation and smart manufacturing to enhance efficiency and precision. This shift not only optimizes production processes but also allows for more complex designs that were once thought impossible.
Automation and Smart Manufacturing
Automation is revolutionizing the way we think about CNC wire bending machines. With advancements in robotics and artificial intelligence, these machines can now perform intricate tasks with minimal human intervention, significantly reducing the risk of errors. Smart manufacturing technologies also enable real-time monitoring and data analysis, allowing manufacturers to make informed decisions that improve productivity and reduce downtime.
Moreover, the integration of IoT (Internet of Things) in forming machines has paved the way for predictive maintenance, ensuring that equipment remains operational longer while minimizing unexpected breakdowns. As a result, CNC wire bending machine manufacturers are producing machines that not only bend wires but also adapt to changing production needs seamlessly. The future looks bright with automation leading the charge in enhancing operational efficiencies across various industries.
Evolving Designs and Customization
In an era where personalization is king, evolving designs in wire bending are taking center stage. Modern CNC wire bending machines offer unparalleled customization options that cater to unique client specifications—from intricate shapes to specific material requirements. Manufacturers can now produce twisted wire folding labeling machines tailored precisely to customer needs, making it easier than ever for businesses to stand out in competitive markets.
This trend towards customization extends beyond just product design; it encompasses entire production lines as well. Many companies are investing in flexible forming machines capable of switching between different tasks without extensive reconfiguration or downtime. Such adaptability allows businesses to respond swiftly to market changes while maintaining high-quality standards.
Sustainability in CNC Manufacturing
Sustainability is no longer just a buzzword; it’s a necessity that’s reshaping how CNC wire bending machine manufacturers operate. As environmental concerns rise globally, companies are seeking ways to minimize waste and energy consumption throughout their manufacturing processes. By adopting eco-friendly materials and practices, they’re not only complying with regulations but also appealing to a growing base of environmentally conscious consumers.
Furthermore, innovative approaches such as recycling scrap metal from production processes into new products demonstrate how sustainability can be integrated into every aspect of manufacturing—especially within forming machines designed for efficiency and minimal waste generation. The focus on sustainability ensures that future generations will have access to both advanced technology and a healthier planet.
Conclusion
As we draw the curtain on our exploration of CNC wire bending technology, it's clear that selecting the right manufacturer is crucial for success in this intricate industry. With a plethora of CNC wire bending machine manufacturers out there, businesses must carefully assess their options based on performance, reliability, and support services. Investing in a quality CNC Wire Bending Machine can significantly enhance production efficiency and product quality, making it imperative to choose wisely.
Choosing the Right Manufacturer for You
When it comes to choosing a manufacturer for your wire bending needs, consider factors like reputation and technological innovation. Leading CNC wire bending machine manufacturers often provide tailored solutions that align with specific business requirements. Additionally, customer service and technical support should not be overlooked; after all, you want a partner who can help troubleshoot any issues that may arise with your Wire Bending Machine.
The Impact of Technology on Wire Forming
The influence of technology on wire forming cannot be overstated; it's revolutionizing how we approach manufacturing processes. Modern Forming Machines are equipped with advanced features such as automation and real-time monitoring, which streamline operations and reduce waste. As CNC machines continue to evolve, they offer unprecedented levels of precision and efficiency that were unimaginable just a few years ago.
Future Considerations in CNC Machinery
Looking ahead, several trends are poised to shape the future landscape of CNC machinery in the wire bending sector. The rise of smart manufacturing will likely lead to more interconnected systems where machines communicate seamlessly with each other—think Twisted Wire Folding Labeling Machines working in harmony with other equipment! Sustainability will also play a pivotal role as manufacturers seek greener solutions without compromising performance or quality.