Introduction
In the world of manufacturing and fabrication, electric wire bending machines have emerged as essential tools for producing intricate wire forms with precision and efficiency. These machines, particularly CNC wire bending machines, automate the process of shaping metal wires into various configurations, making them invaluable in industries ranging from automotive to construction. By harnessing advanced technology, these machines can handle different materials, including galvanized metal wire, ensuring versatility in applications.
Overview of Electric Wire Bending Machines
Electric wire bending machines are designed to streamline the bending process of metal wires with high levels of accuracy and speed. Among these, CNC wire bending machines stand out due to their computer-controlled operations that allow for complex designs and repeatability. With a variety of models available from numerous CNC wire bending machine manufacturers, businesses can find solutions tailored to their specific needs.
Importance of Choosing the Right Machine
Selecting the right electric wire bending machine is crucial for optimizing production efficiency and product quality. The wrong choice could lead to increased downtime or subpar output that fails to meet industry standards. By understanding the capabilities and limitations of different CNC wire formers, manufacturers can invest wisely in equipment that enhances their operational workflow.
Key Features to Consider
When evaluating electric wire bending machines, several key features should be at the forefront of your decision-making process. Speed is a critical factor; faster machines can significantly boost productivity without compromising quality. Additionally, precision is essential for creating accurate bends in galvanized metal wire or other materials—ensuring that every piece meets exact specifications while maximizing material usage.
Top Electric Wire Bending Machine Brands
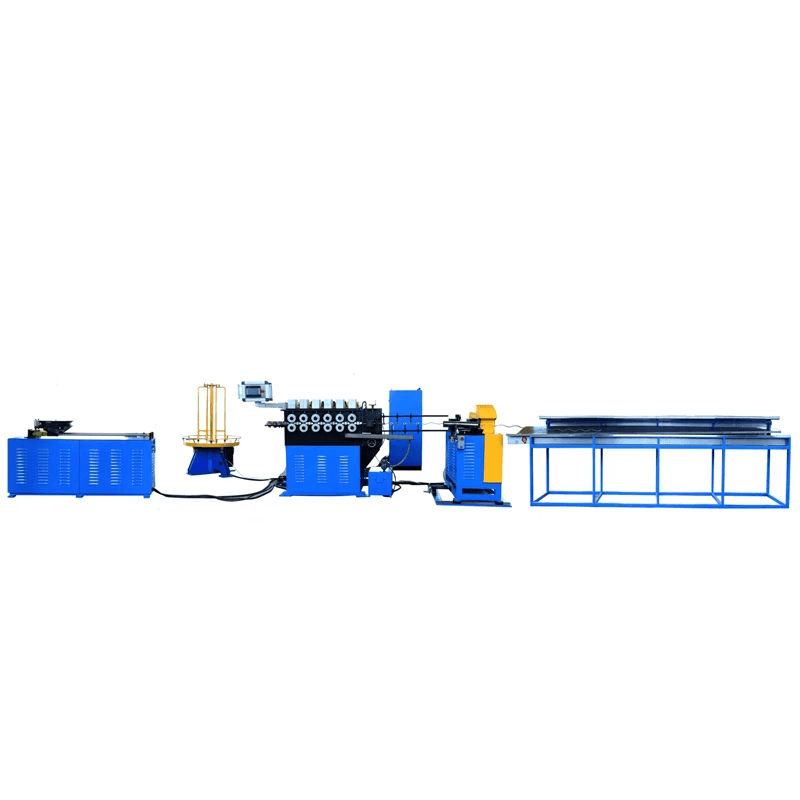
Highlighting Key Players in the Market
Several brands stand out in the electric wire bending machine industry due to their reputation for quality and innovation. Companies like TJK Machinery, KUKA Robotics, and Haco are recognized as leaders among CNC wire bending machine manufacturers. These manufacturers not only provide robust machines but also invest heavily in research and development, ensuring their products remain at the forefront of technology.
In addition to these heavyweights, newer players like Wire Bender Pro are gaining traction by offering specialized solutions tailored for specific industries. This diversity allows customers to choose from a wide range of options based on their unique needs and applications. As competition heats up among these wire forming manufacturers, customers can expect more advanced features and improved efficiency in their electric wire bending machines.
Popular Models from CNC Wire Bending Machine Manufacturers
Among the plethora of options available today, certain models have captured attention due to their outstanding performance and reliability. The TJK CNC Wire Bender is known for its precision and speed when working with galvanized metal wire, making it a favorite among automotive part manufacturers. Similarly, Haco’s WIREBEND series offers flexibility with programmable features that cater to various bending requirements.
These popular models not only enhance productivity but also reduce waste through efficient material usage—an essential factor when working with costly materials like galvanized metal wire. Moreover, many CNC wire former models come equipped with user-friendly interfaces that simplify operation for technicians of all skill levels. By choosing one of these renowned models from reputable manufacturers, businesses can ensure they’re investing in machinery that stands up to rigorous demands.
Innovations in Electric Wire Bending Technology
The landscape of electric wire bending technology is evolving rapidly as manufacturers integrate cutting-edge innovations into their machines. Automation has become a significant trend within this sector; many modern CNC wire bending machines now feature advanced robotics that streamline production processes while maintaining high levels of accuracy. This shift towards automation not only enhances efficiency but also minimizes labor costs associated with manual operations.
Another exciting development is the incorporation of smart technology into electric wire bending machines—think IoT connectivity that allows real-time monitoring and data analysis during production runs! These advancements enable manufacturers to optimize operations further by identifying potential bottlenecks or inefficiencies on-the-fly. As innovations continue to emerge within this space, businesses leveraging state-of-the-art machinery will undoubtedly gain a competitive edge.
Comparing CNC Wire Bending Machines
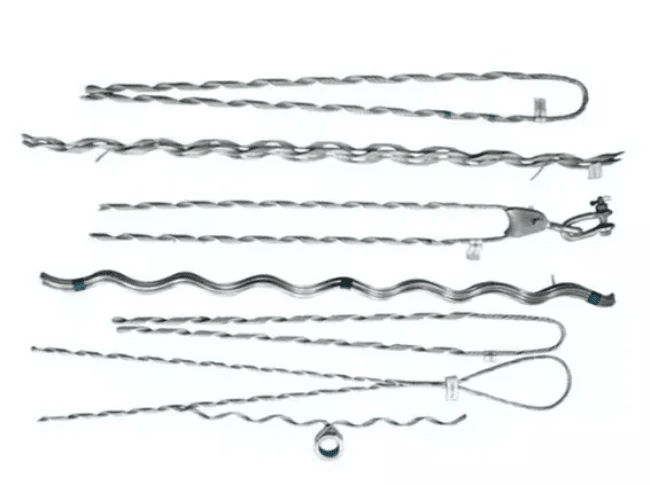
Understanding Different Types of CNC Wire Formers
CNC wire formers come in several varieties, each suited for specific applications and materials. Generally, you can find three main types: rotary benders, multi-axis benders, and 3D benders. Rotary benders typically excel at producing standard bends with high speed and accuracy, while multi-axis benders offer flexibility for more complex geometries by allowing multiple bends in one setup; 3D benders take this a step further by enabling intricate designs that require three-dimensional manipulation of galvanized metal wire.
Choosing the right type of CNC wire former largely depends on your production needs and the complexity of the designs you want to achieve. If your projects involve straightforward shapes, a rotary bender might be sufficient; however, for more elaborate designs that require precision bends at varying angles, investing in a multi-axis or 3D bending machine could be beneficial. Overall, understanding these distinctions will help streamline your decision-making process when selecting from various wire forming manufacturers.
Pros and Cons of Various Machines
Each type of electric wire bending machine has its own set of advantages and disadvantages that should be carefully weighed before making a purchase decision. For instance, rotary benders are generally faster and easier to operate but may lack precision for complex shapes compared to their multi-axis counterparts. On the other hand, while multi-axis machines offer greater versatility in design capabilities, they often come with higher costs and steeper learning curves—making them less accessible for smaller operations.
Furthermore, some CNC wire bending machines are designed specifically for high-volume production runs but may struggle with small batch jobs due to longer setup times. Conversely, machines made for low-volume applications might not deliver the speed needed for larger projects but provide excellent flexibility when it comes to custom orders involving galvanized metal wire. Evaluating these pros and cons against your operational requirements will ensure you choose a machine that aligns well with your business goals.
Feature Analysis: Speed, Precision, and Efficiency
In assessing different CNC wire bending machines from various manufacturers, three critical features stand out: speed, precision, and efficiency—each playing a pivotal role in determining overall productivity. Speed refers not only to how quickly a machine can complete bends but also how efficiently it can switch between different setups or designs without significant downtime—a vital factor if you're working with diverse product lines or custom orders.
Precision is equally important; after all, even minor inaccuracies can lead to costly errors down the line when working with galvanized metal wire or other materials that require tight tolerances. High-quality electric wire bending machines typically incorporate advanced technology such as servo motors or laser-guided systems that enhance accuracy while maintaining high speeds during operation.
Lastly—and perhaps most importantly—efficiency encompasses both energy consumption during operation as well as overall workflow optimization within your facility's layout design around these machines. Investing in an efficient CNC wire former not only reduces operational costs but also contributes positively towards sustainability efforts within manufacturing processes—a win-win situation!
The Role of Galvanized Metal Wire

Why Galvanized Metal Wire is Preferred
Galvanized metal wire is preferred by many due to its exceptional strength and flexibility, which are crucial attributes when working with CNC wire bending machines. The galvanization process involves coating steel with zinc, creating a barrier that resists environmental wear and tear. This not only extends the life of the wire but also ensures that it can withstand the rigorous demands of high-speed production lines without compromising quality.
Additionally, using galvanized metal wire in your projects means less maintenance and fewer replacements over time, translating into cost savings for businesses. The ability of this material to be easily bent and formed makes it perfect for intricate designs produced by CNC wire formers. Thus, it's no wonder that many leading CNC wire bending machine manufacturers advocate for its use in their equipment.
Applications of Galvanized Metal Wire in Bending
Galvanized metal wire finds numerous applications across various industries due to its versatility and strength when processed through electric wire bending machines. From constructing furniture frames to creating intricate fencing designs or even automotive components, this material proves invaluable in producing durable goods that require precision forming techniques. The adaptability of galvanized metal allows it to be used in both light-duty and heavy-duty applications.
In addition to structural uses, galvanized metal wire is frequently employed in crafting decorative items such as garden trellises or artistic sculptures where aesthetic appeal meets functionality. Its ability to be shaped into complex forms while maintaining structural integrity makes it an excellent choice for artists and manufacturers alike who utilize CNC wire bending machines for creative projects. This wide range of applications underscores why galvanized metal is a go-to option among various industries.
Compatibility with Electric Wire Bending Machines
Electric wire bending machines are specifically designed to handle various types of wires—including galvanized metal—making them highly versatile tools in manufacturing settings. These machines can easily accommodate the unique properties of galvanized metal due to their advanced technology and precise control systems found in modern CNC wire bending machines. This compatibility ensures smooth operation without jamming or excessive wear on the machinery itself.
Moreover, the integration between electric wire bending machines and galvanized metal allows manufacturers to optimize production efficiency while achieving high-quality results consistently. With features like adjustable speed settings and programmable controls available from leading CNC wire bending machine manufacturers, users can tailor their processes according to specific project requirements involving galvanized materials seamlessly. Consequently, this synergy between machine capability and material properties enhances productivity across diverse manufacturing sectors.
16A Pre-Twisted Wire Automatic Forming Production Line
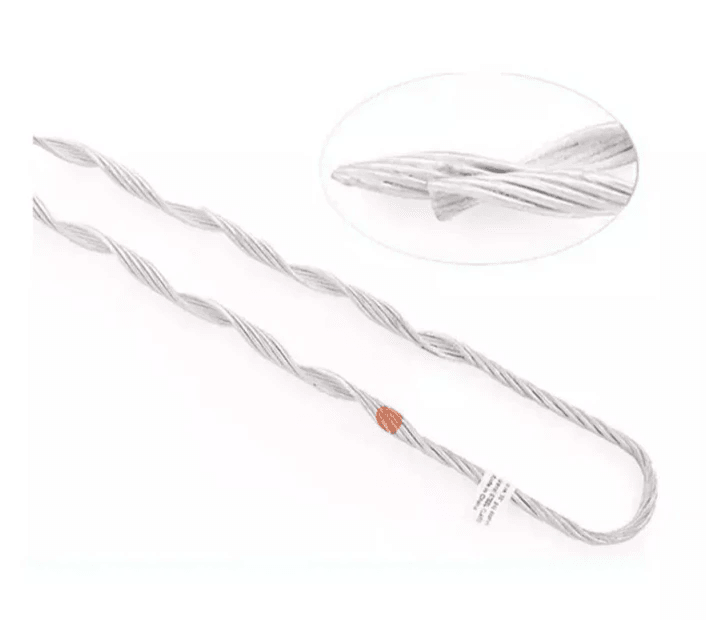
When it comes to efficiency and precision in wire forming, the 16A Pre-Twisted Wire Automatic Forming Production Line by Spark Fittings stands out as a remarkable example. This advanced electric wire bending machine is designed specifically for the fast-paced demands of modern manufacturing environments. By integrating state-of-the-art technology, this production line ensures that galvanized metal wire is manipulated with utmost accuracy and speed.
Overview of Spark Fittings’ Production Line
Spark Fittings’ production line is engineered to streamline the process of creating pre-twisted wires, making it a go-to solution for many industries. It combines multiple functions into one cohesive unit, allowing for seamless transitions between different stages of wire forming. This innovative setup not only enhances productivity but also minimizes waste, ensuring that manufacturers get the most out of their galvanized metal wire resources.
Benefits of the Conveyor and Forming Machine Configuration
One of the standout features of this production line is its conveyor and forming machine configuration, which optimizes workflow like never before. This setup allows for continuous operation, significantly reducing downtime typically associated with manual handling or traditional machines. As a result, CNC wire bending machines can operate at higher speeds while maintaining precision—a win-win situation for any wire forming manufacturer looking to boost output without sacrificing quality.
High-Speed Integrated Cutting Machine Features
The high-speed integrated cutting machine included in Spark Fittings’ production line further elevates its capabilities by offering rapid and precise cutting solutions tailored for various applications. With advanced sensors and automation technology, this cutting machine ensures that each piece meets stringent specifications without delays or errors common in older models. Consequently, manufacturers can rely on this electric wire bending machine to deliver consistent results while keeping pace with their production demands.
Selecting the Right Wire Forming Manufacturers
Choosing the right wire forming manufacturers is crucial for ensuring you get a quality electric wire bending machine that meets your needs. With numerous CNC wire bending machines available, it's essential to evaluate manufacturers based on their reputation, product offerings, and customer feedback. A thorough assessment will help you identify reliable partners who can provide high-quality equipment and support.
How to Evaluate Wire Forming Manufacturers
When evaluating wire forming manufacturers, start by researching their experience in the industry. Look for CNC wire bending machine manufacturers with a proven track record of producing reliable machines that can handle galvanized metal wire effectively. Additionally, consider their certifications and compliance with industry standards as indicators of quality and reliability.
Another key factor is the range of products offered by the manufacturer. A good manufacturer should have various CNC wire formers tailored to different applications and materials, including electric wire bending machines designed specifically for galvanized metal wire. Finally, customer reviews and testimonials can provide valuable insights into the performance and durability of their machines.
Questions to Ask CNC Wire Bending Machine Manufacturers
Before making a purchase decision, it’s essential to ask potential CNC wire bending machine manufacturers specific questions that reveal critical information about their products and services. Start by inquiring about the specifications of their electric wire bending machines—understanding speed, precision, and capabilities will help you assess whether they meet your production needs.
Don't hesitate to ask about warranty terms and after-sales support as well; this can significantly impact your satisfaction with the machine over time. Additionally, inquire about customization options for your CNC wire former—manufacturers who offer flexibility in design may better cater to unique requirements involving galvanized metal wires or other specific applications.
Importance of Customer Support and Service
Customer support is often an overlooked aspect when selecting a manufacturer but plays a vital role in your overall experience with an electric wire bending machine. Reliable service ensures that any issues are addressed promptly—this is especially important if you're using complex CNC wire bending machines where downtime could lead to significant losses in productivity.
A manufacturer that offers comprehensive training on their equipment can also enhance your operational efficiency; understanding how to maximize features specific to your chosen CNC wire former will ensure optimal performance over time. Furthermore, ongoing maintenance support from reputable wire forming manufacturers guarantees long-term functionality of your investment in an electric wire bending machine.
Conclusion
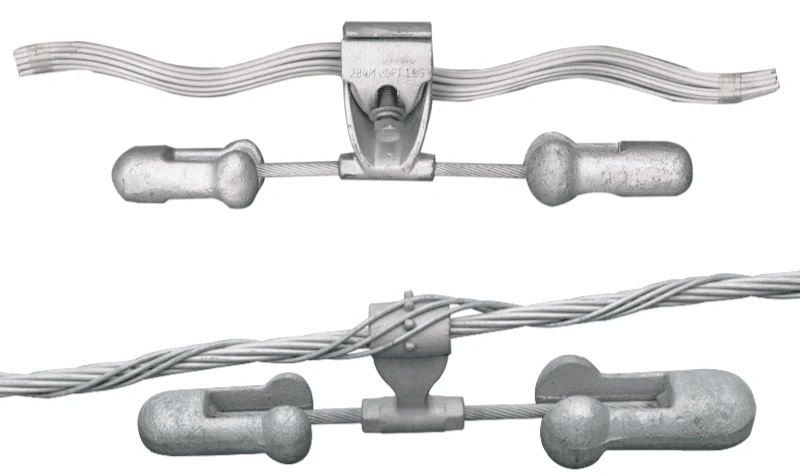
In the rapidly evolving world of manufacturing, electric wire bending machines stand at the forefront of innovation and efficiency. As industries continue to demand precision and speed, CNC wire bending machines are becoming increasingly sophisticated, integrating advanced technologies that enhance their functionality. The future promises even more improvements, including smarter automation and greater compatibility with various materials like galvanized metal wire.
The Future of Electric Wire Bending Machines
The future of electric wire bending machines looks promising, with technology advancing at a breakneck pace. Emerging trends suggest that CNC wire bending machines will incorporate artificial intelligence to optimize production processes and minimize waste. As manufacturers continue to innovate, we can expect even more specialized solutions tailored for specific applications involving galvanized metal wire.
Key Takeaways for Your Purchase Decision
When contemplating the purchase of a CNC wire former, it’s crucial to evaluate several factors that can influence your decision-making process. Consider the machine's speed, precision, and efficiency—these features are vital in determining how well it meets your production needs. Additionally, researching reputable wire forming manufacturers can provide insights into reliability and customer support options available after your investment.
Final Thoughts on Best Options Available
In conclusion, selecting the right electric wire bending machine requires careful consideration of your specific requirements and available models in the market. With numerous CNC wire bending machine manufacturers offering an array of products designed for various applications—including those using galvanized metal wire—there’s no shortage of options tailored to fit your needs. Ultimately, investing in a high-quality machine from a trusted manufacturer will ensure that you remain competitive in an ever-evolving industry landscape.