Introduction
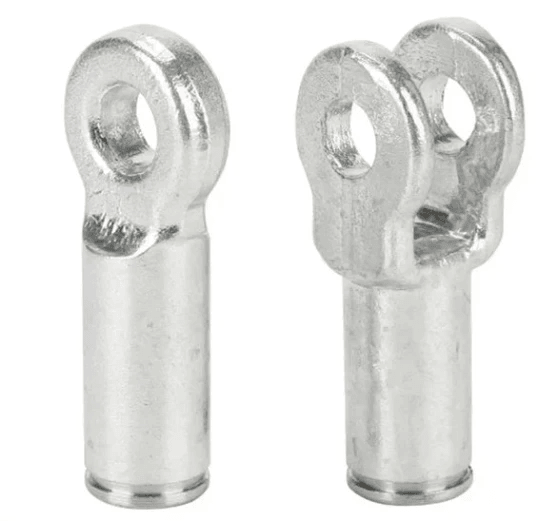
In the world of industrial cleaning, the industrial sand blasting machine stands out as a powerhouse tool that transforms surfaces with precision and efficiency. Whether you're in construction, manufacturing, or automotive industries, understanding how to harness the potential of sand blast equipment is crucial for optimal results. Choosing the right equipment not only enhances productivity but also ensures that you achieve the desired finish without compromising on safety.
Understanding Industrial Sand Blasting Machines
An industrial sand blasting machine utilizes high-pressure air to propel abrasive materials—commonly known as blasting media—against surfaces to remove contaminants and prepare them for further treatment. This powerful process is essential in various applications, from rust removal on metal structures to surface preparation for painting and coating. By grasping the functionality of these machines, users can appreciate their role in streamlining operations and achieving superior results compared to manual cleaning methods.
Importance of Choosing the Right Equipment
Selecting the appropriate industrial sand blaster is pivotal for maximizing efficiency and effectiveness in your projects. The right model not only impacts performance but also influences maintenance costs and operational safety—factors that can significantly affect your bottom line. Investing time in understanding various models and their capabilities ensures that you choose an industrial sand blasting machine tailored to your specific needs.
Overview of Key Features
When exploring options for sand blast equipment, it’s vital to consider key features such as tank capacity, pressure settings, and compatibility with different types of sand blasting media. Advanced designs may include user-friendly controls and enhanced safety features that protect operators while optimizing performance. By familiarizing yourself with these attributes, you'll be better equipped to make informed decisions about which industrial blasting solution fits best within your operational framework.
What is an Industrial Sand Blasting Machine?
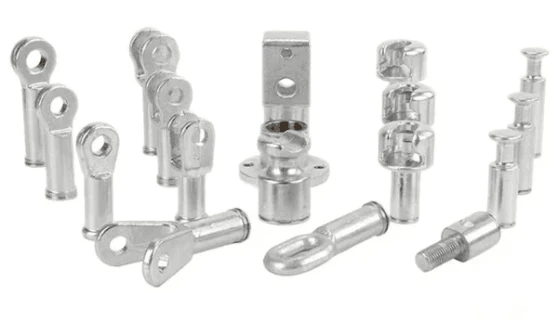
Definition and Functionality
An industrial sand blasting machine is designed for heavy-duty applications where precision and efficiency are paramount. The core functionality revolves around the use of various types of blasting media that are propelled at high speeds to abrade surfaces cleanly and uniformly. This process not only prepares surfaces for painting or coating but also enhances their overall durability by creating a textured finish that improves adhesion.
Common Applications in Various Industries
Industrial sand blasters find their niche across multiple sectors including automotive, aerospace, construction, and metal fabrication. In the automotive industry, they’re heavily utilized for stripping paint from vehicles or preparing metal parts for welding. Similarly, in construction and renovation projects, these machines play a crucial role in restoring surfaces by removing old coatings or preparing concrete for sealing.
Advantages Over Manual Cleaning Methods
The advantages of using an industrial sand blasting machine over manual cleaning methods are numerous and compelling. First off, they significantly reduce labor time; what might take hours with scrapers or chemicals can often be accomplished in mere minutes with a blaster. Additionally, the consistency achieved through automated blasting ensures that every inch of surface receives equal treatment—something that's nearly impossible with manual techniques—making it the go-to choice for professionals seeking efficiency and quality.
Types of Blasting Media
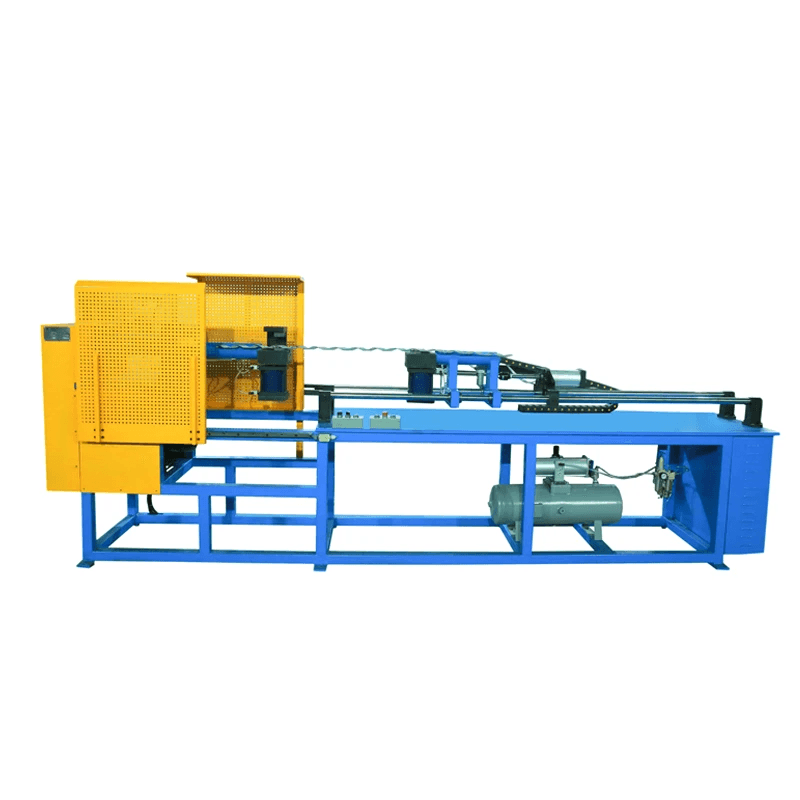
Overview of Sand Blasting Media Options
Industrial sand blasters utilize a range of blasting media that can include silica sand, garnet, glass beads, and more. Silica sand is often the go-to choice for many applications due to its effectiveness and cost-efficiency; however, it can pose health risks if inhaled. On the other hand, garnet offers a cleaner alternative with minimal dust production and better recycling capabilities.
Glass beads provide a gentler approach for delicate surfaces or when a smooth finish is desired, while aluminum oxide is favored for its durability in heavy-duty applications. Each type of blasting media has distinct characteristics that influence not only cleaning efficiency but also surface finish quality. Therefore, understanding these options helps you select the best fit for your specific industrial blasting needs.
Pros and Cons of Different Types
Every type of blasting media comes with its advantages and disadvantages that should be weighed carefully before making a decision on your industrial sand blaster setup. For instance, while silica sand is inexpensive and effective at removing rust or paint, it poses significant health risks due to silica dust exposure—definitely not ideal in an environment where safety is paramount!
Garnet may be pricier but offers superior performance with less dust generation; however, it might not be necessary for lighter cleaning tasks where cheaper alternatives could suffice. Glass beads are excellent for achieving a smooth finish but may take longer to achieve desired results compared to more aggressive media like aluminum oxide which excels in rapid removal but can damage softer surfaces if used carelessly.
Selecting the Right Blasting Media for Your Needs
Selecting the right blasting media involves evaluating your specific application requirements alongside safety considerations associated with each type of media available for your industrial sand blast equipment. Start by identifying what you're trying to achieve: Are you looking to remove heavy corrosion from metal? If so, aluminum oxide or garnet might be your best bet due to their aggressive nature.
Conversely, if you're working on delicate parts or need a polished surface finish without risking damage—glass beads could be your go-to choice! Always consider factors such as cost-effectiveness, environmental impact (like dust production), and compatibility with your existing industrial blasting setup before making that final call on which sand blasting media will serve you best.
Essential Components of Industrial Blasters

When it comes to industrial sand blasting machines, understanding the essential components is crucial for optimal performance and efficiency. Each part plays a significant role in ensuring that the machine operates smoothly and effectively, allowing for the best results in various applications. From the pressure system to the nozzle design, every component contributes to the overall functionality of sand blast equipment.
Key Parts and Their Functions
An industrial sand blaster consists of several key parts that work together harmoniously. The pressure vessel stores the blasting media under high pressure, which is then released through a nozzle for effective cleaning or surface preparation. Additionally, components such as air compressors, hoses, and regulators ensure a steady flow of air and media, facilitating efficient operation during industrial blasting tasks.
Moreover, nozzles come in various shapes and sizes tailored for specific applications; they determine how concentrated or dispersed the blasting media will be upon impact with a surface. The choice of nozzle can dramatically affect both efficiency and finish quality when using different types of sand blasting media. Understanding these key parts not only helps in selecting the right industrial sand blasting machine but also enhances maintenance practices down the line.
Importance of Durability and Quality
The durability and quality of an industrial sand blaster are paramount to its longevity and effectiveness in demanding environments. High-quality materials ensure that components can withstand abrasive conditions without frequent breakdowns or replacements—saving both time and money on repairs or downtime. Investing in durable sand blast equipment means fewer interruptions during projects, translating to increased productivity across operations.
Furthermore, top-notch construction minimizes wear on critical parts like hoses and nozzles which are subject to constant friction from blasting media. This durability extends beyond mere function; it also enhances safety by reducing risks associated with equipment failure during operation. Ultimately, choosing robust materials leads to better overall performance from your industrial sand blasting machine.
Innovations in Industrial Sand Blaster Design
The landscape of industrial blasting technology is constantly evolving thanks to innovations aimed at improving efficiency and user experience. Modern designs now incorporate features such as automated controls that allow operators to adjust settings quickly based on specific project requirements—making it easier than ever to switch between different types of blasting media without hassle.
Additionally, advancements in ergonomic design mean less strain on operators during prolonged use; lighter materials combined with thoughtful layouts make handling these machines more comfortable than before. Innovations also include improved dust collection systems that enhance workplace safety by minimizing airborne particles generated during blasting operations—a win-win for both health-conscious companies and regulatory compliance.
As we look toward future trends in industrial sand blasters, expect even more smart technology integration that streamlines processes while maximizing output quality through enhanced monitoring systems capable of real-time adjustments based on environmental conditions.
Safety Features to Consider
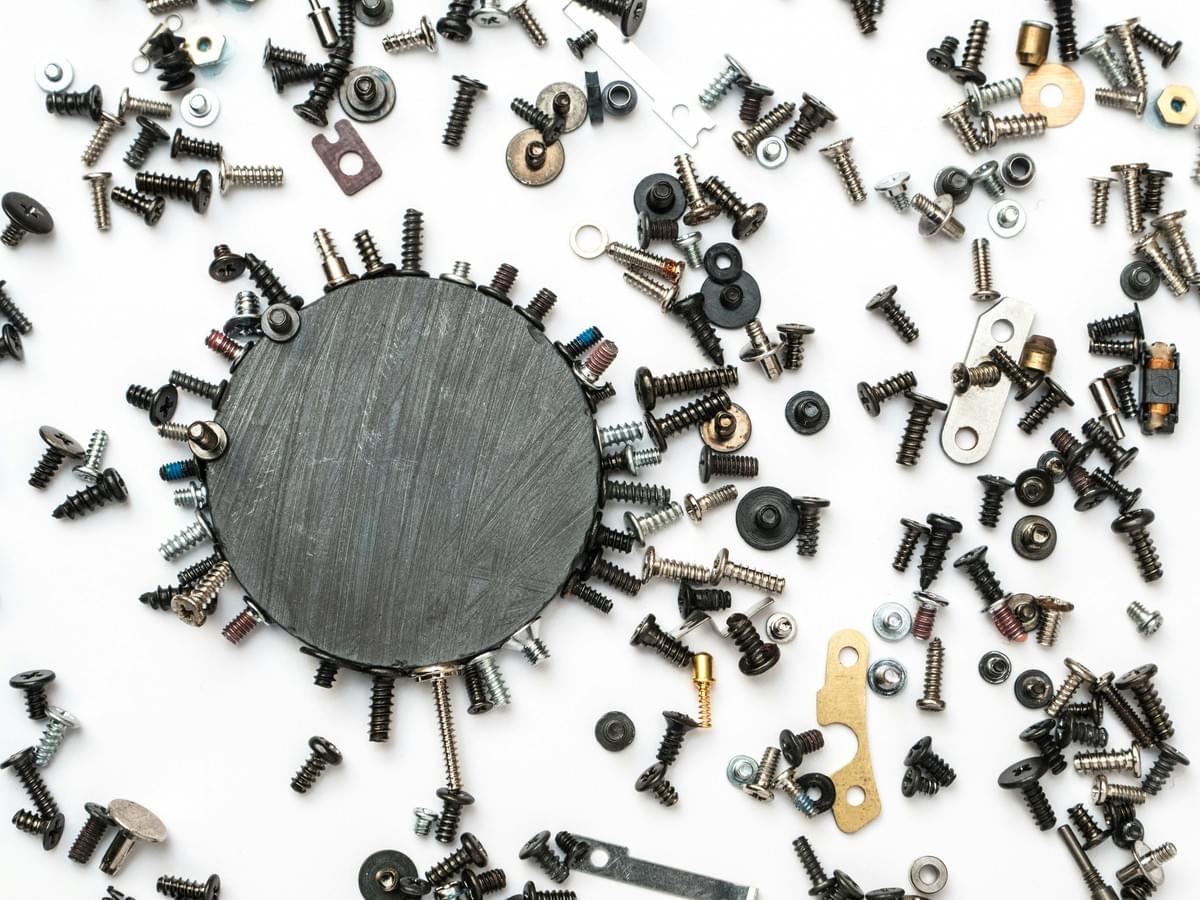
When it comes to industrial environments, safety should always be the top priority. An industrial sand blasting machine can be a powerful tool, but without proper safety measures, it can also pose significant risks. Understanding the importance of safety in these settings is crucial for protecting workers and ensuring efficient operations.
Importance of Safety in Industrial Environments
In the realm of industrial blasting, the hazards associated with using an industrial sand blasting machine cannot be overlooked. The high-pressure nature of these machines means that flying debris and harmful dust particles are common, making protective measures essential for worker safety. Moreover, a lack of proper safety protocols can lead to severe injuries or even fatalities, which is why prioritizing safety in these environments is paramount.
Essential Safety Equipment and Protocols
To effectively mitigate risks when using sand blast equipment, certain essential safety equipment must be utilized. Personal protective equipment (PPE) like respirators, goggles, gloves, and protective suits are vital for safeguarding workers from exposure to hazardous blasting media and debris. Additionally, implementing strict operational protocols—such as regular training sessions on equipment handling—ensures that all personnel understand how to operate the industrial sand blaster safely.
Regulatory Standards for Sand Blast Equipment
Adherence to regulatory standards is another critical aspect of maintaining a safe work environment when using an industrial sand blasting machine. Organizations such as OSHA (Occupational Safety and Health Administration) provide guidelines that dictate how sand blast equipment should be used and maintained to minimize risks associated with industrial blasting operations. By following these regulations rigorously, companies can not only ensure compliance but also foster a culture of safety that protects their workforce while maximizing efficiency.
Maintenance and Efficiency Tips
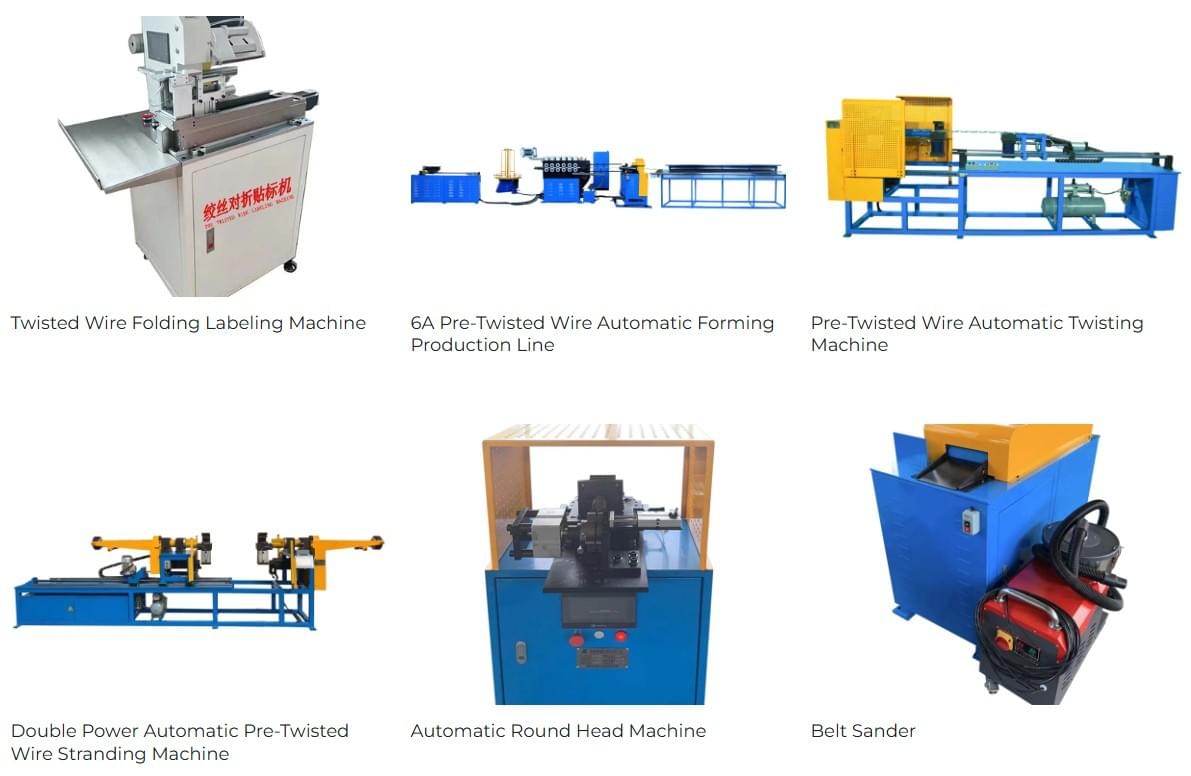
Keeping your industrial sand blasting machine in top-notch condition is crucial for maximizing its efficiency and lifespan. Regular maintenance not only ensures optimal performance but also helps prevent costly downtimes that can disrupt your operations. With the right care, your industrial blaster can continue to deliver exceptional results, whether you're using various types of blasting media or focusing on specific applications.
Routine Maintenance Practices
Routine maintenance practices for your sand blast equipment are essential to keep it running smoothly. Start by regularly checking and replacing worn-out components, such as hoses and nozzles, which can wear down due to constant exposure to abrasive blasting media. Additionally, ensure that the air filters are clean; a clogged filter can diminish performance and lead to inefficiencies in your industrial blasting process.
Another critical aspect of maintenance involves inspecting the pressure settings and ensuring they align with manufacturer recommendations. This helps maintain consistent results while preventing damage from excessive pressure on sensitive materials. Lastly, don’t forget about cleaning the exterior of your industrial sand blasting machine; a clean machine not only looks good but also allows you to spot potential issues early on.
How to Maximize Your Industrial Blaster's Lifespan
To maximize the lifespan of your industrial sand blaster, invest time in proper training for operators who will be using the equipment. Well-trained personnel will understand how to handle different types of sand blasting media correctly and operate machinery without causing unnecessary wear and tear. Moreover, adhering strictly to operational guidelines provided by manufacturers can significantly enhance durability.
It’s also wise to implement a schedule for routine inspections that includes checking all connections, seals, and valves for signs of wear or leaks. Addressing these minor issues promptly can prevent them from escalating into major problems that could sideline your operations for extended periods. Lastly, consider upgrading parts with higher-quality alternatives when replacements are needed; investing in durable components pays off in longevity down the line.
Troubleshooting Common Issues
Even with diligent maintenance practices in place, you may encounter common issues with your industrial sand blasting machine over time. One frequent problem is inconsistent pressure during operation; this could be due to blockages or leaks within the system affecting air flow or media delivery. Regularly inspect hoses and connections for any signs of damage or obstruction that might cause these fluctuations.
Another issue operators often face is poor surface finish results after blasting—this could stem from using inappropriate types of blasting media or incorrect settings on the machine itself. It’s essential to match your chosen sand blast equipment settings with the specific requirements of both material type and desired finish quality for optimal outcomes. If problems persist despite troubleshooting efforts, consulting with a professional familiar with industrial blasting technology may provide valuable insights into more complex issues.
Conclusion
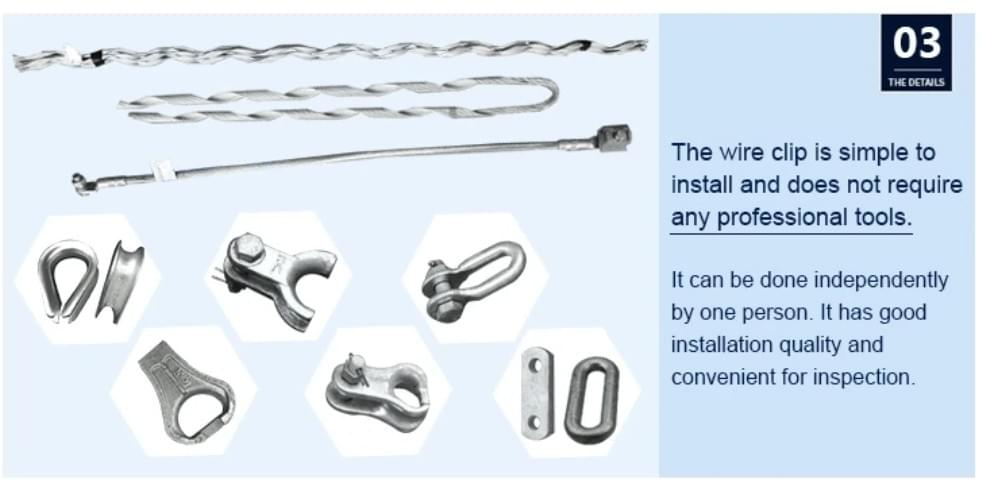
In the world of industrial cleaning, choosing the right industrial sand blasting machine is paramount for efficiency and effectiveness. A well-selected sand blast equipment can significantly enhance productivity while ensuring superior results across various applications. As you navigate your options, consider factors like blasting media compatibility, safety features, and maintenance requirements to make an informed decision.
Choosing the Right Industrial Sand Blasting Machine
When selecting an industrial sand blasting machine, it’s essential to assess your specific needs and operational demands. Not all sand blasting media are created equal; some are better suited for delicate surfaces while others tackle heavy-duty tasks with ease. Evaluating the types of materials you'll be working with will guide you toward the most appropriate industrial blaster that aligns with your requirements.
Moreover, understanding the different types of sand blast equipment available—such as portable units versus stationary models—can influence your choice significantly. Each type has its unique advantages depending on space constraints and mobility needs in your workspace. Ultimately, investing time in research will pay off by ensuring you select a machine that maximizes efficiency and minimizes downtime.
The Role of Spark Fittings in Blasting Efficiency
Spark fittings play a crucial role in enhancing the performance of industrial sand blasting machines by optimizing airflow and media flow during operation. These fittings help maintain consistent pressure levels within the system, allowing for smoother operation and more effective cleaning results. By ensuring that the right amount of blasting media is delivered precisely where it's needed, spark fittings contribute significantly to overall blasting efficiency.
Additionally, high-quality spark fittings can prevent premature wear on machinery components by reducing friction and heat buildup during use. This not only prolongs the lifespan of your industrial sand blaster but also minimizes maintenance costs over time. In essence, investing in superior spark fittings is a smart move for any business looking to enhance their industrial blasting capabilities.
Future Trends in Industrial Blasting Technology
The landscape of industrial blasting technology is continually evolving, with innovations aimed at improving efficiency and sustainability becoming more prevalent each year. One notable trend is the increased adoption of eco-friendly blasting media that reduces environmental impact without sacrificing performance—an important consideration for modern businesses committed to sustainability practices.
Moreover, advancements in automation are making their way into sand blast equipment design, enabling smarter systems that require less manual intervention while delivering consistent results every time they’re used. As technology continues to advance, we can expect even greater improvements in safety features and operational efficiencies within industrial sand blasters.
In conclusion, staying informed about these trends will empower businesses to adopt cutting-edge solutions that enhance productivity while also being mindful of environmental responsibilities.