Introduction
In the world of manufacturing, custom wire forming stands out as a crucial process that enhances the functionality and efficiency of various applications. Whether it’s for automotive, aerospace, or industrial use, understanding the intricacies of wire forming can lead to significant improvements in product performance and reliability. As industries evolve, so does the demand for innovative metal forming services that cater to specific needs, making custom solutions more important than ever.
Understanding the Importance of Custom Wire Forming
Custom wire forming is not just about bending metal; it's about crafting solutions tailored to meet unique specifications and challenges. This process allows manufacturers to create intricate shapes and designs that standard wire cannot achieve, ensuring a perfect fit for any application. By utilizing advanced wire bending equipment and techniques, businesses can optimize their products for better performance while reducing waste in material usage.
The Role of Wire Fasteners in Quality Assurance
Wire fasteners play a pivotal role in maintaining quality assurance across various industries by providing reliable connections that withstand stress and strain. These fasteners not only secure components but also contribute to overall structural integrity, making them indispensable in high-stakes environments where failure is not an option. By selecting the right custom fasteners from reputable wire manufacturers, companies can enhance their product durability and ensure consistent quality throughout their production processes.
Exploring the Benefits of Metal Forming Services
Metal forming services encompass a range of techniques designed to manipulate metal into desired shapes without compromising its integrity. From custom wire solutions to complex assemblies, these services offer numerous advantages such as increased design flexibility and improved production efficiency. With advancements in technology and skilled craftsmanship from experienced wire manufacturers, businesses can achieve exceptional results that align with modern manufacturing demands.
What is Custom Wire Forming?
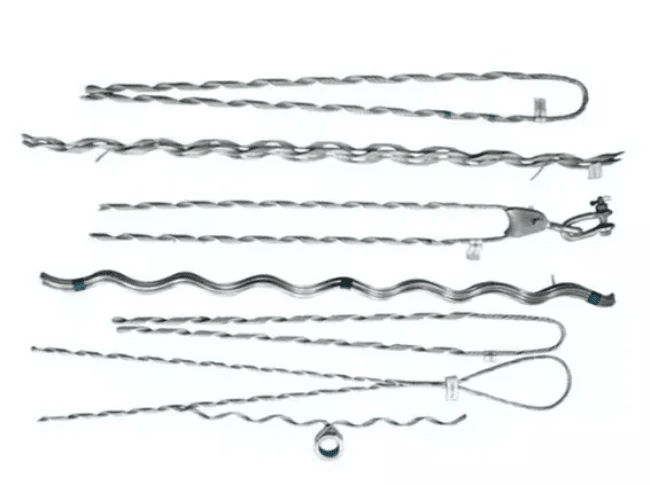
Custom wire forming is a specialized process that transforms raw wire materials into specific shapes and configurations tailored to meet diverse industrial needs. This technique is a crucial aspect of metal forming, allowing manufacturers to create components that are both functional and efficient. By employing custom forming services, businesses can ensure that their products are designed with precision, enhancing overall quality and performance.
Definition and Overview of Wire Forming
Wire forming refers to the manipulation of wire into various shapes through processes like bending, twisting, and cutting. This method is essential in producing components used in numerous applications across different industries—from automotive parts to medical devices. Understanding the intricacies of wire manufacturing helps businesses appreciate how custom wire solutions can significantly improve their product offerings.
Types of Custom Wire Applications
The versatility of custom wire applications knows no bounds; they range from industrial machinery components to intricate decorative items. In the automotive sector, for instance, custom wire forms are used for everything from brackets to clips that hold critical parts together securely. Additionally, sectors like electronics rely on precision-engineered wire fasteners that ensure reliable connections within devices.
Key Benefits of Custom Wire Solutions
Investing in custom wire solutions offers numerous advantages for businesses seeking efficiency and quality in their products. One major benefit is the ability to meet specific design requirements without compromising on functionality or aesthetics—this means fewer modifications during production runs. Moreover, working with skilled wire manufacturers ensures that the final products adhere strictly to industry standards while optimizing costs through streamlined manufacturing processes involving advanced wire bending equipment.
Wire Manufacturing Process Explained
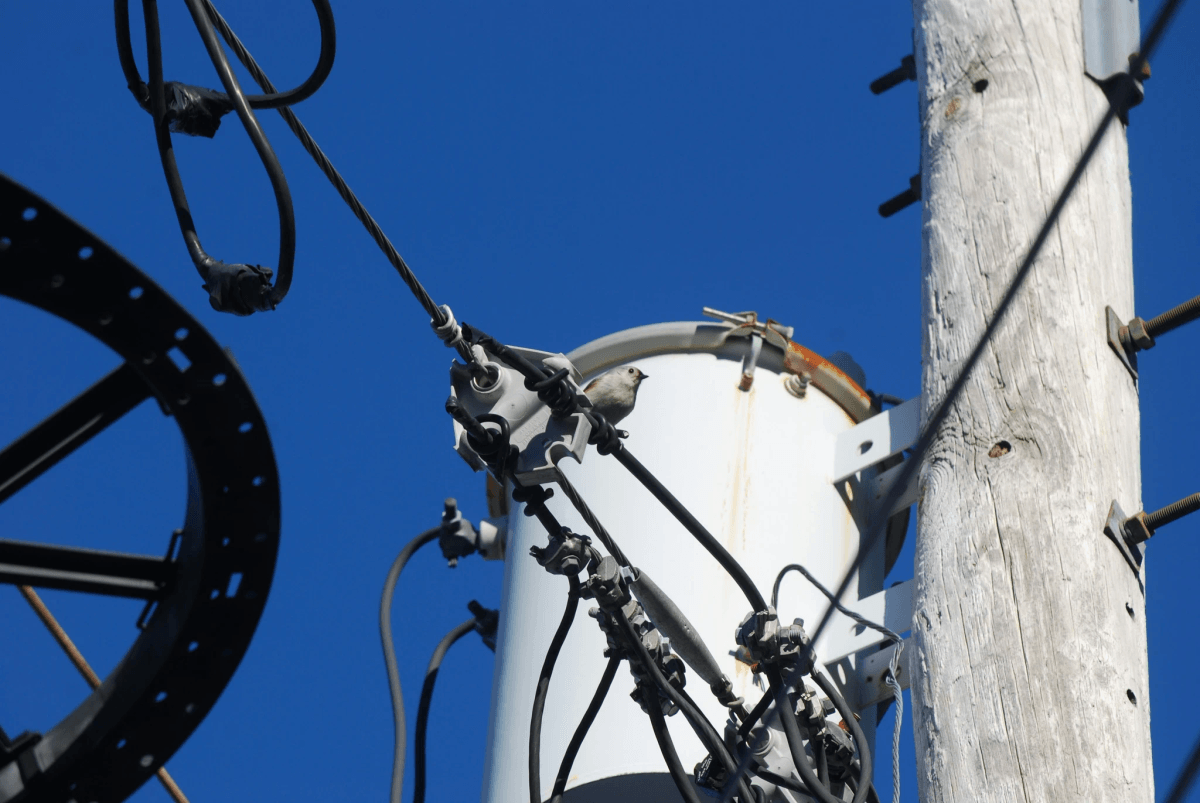
The wire manufacturing process is a fascinating blend of artistry and engineering, where raw materials are transformed into the custom wire solutions that various industries rely on. Understanding the nuances of wire forming is essential for anyone involved in metal forming services, as it ensures that the end product meets specific requirements and standards. From initial material selection to final inspection, each step plays a crucial role in delivering high-quality wire products.
Insights into Wire Production Techniques
Wire production techniques have evolved significantly over the years, incorporating advanced technology to enhance efficiency and precision. Traditional methods such as drawing and rolling are complemented by modern innovations like laser cutting and CNC machining, allowing for greater versatility in custom forming applications. As a result, wire manufacturers can produce a wide range of products tailored to specific needs while maintaining consistent quality throughout the manufacturing process.
Moreover, understanding these techniques is vital for anyone looking to leverage metal forming services effectively. The choice of technique often depends on factors such as material type, desired dimensions, and end-use applications. By staying informed about the latest advancements in wire manufacturing processes, businesses can make smarter decisions when selecting their custom wire solutions.
Importance of Precision in Wire Manufacturing
Precision is paramount in wire manufacturing; even minor discrepancies can lead to significant issues down the line. In industries where safety and reliability are critical—like aerospace or automotive—custom wire must meet stringent specifications to ensure optimal performance. This emphasis on precision not only enhances product quality but also builds trust with clients who depend on these components for their operations.
To achieve this level of accuracy, manufacturers must invest in high-quality equipment and skilled personnel who understand the intricacies of wire forming processes. Regular calibration and maintenance of machinery are essential practices that help maintain precision throughout production runs. Ultimately, prioritizing precision in wire manufacturing leads to improved overall quality and customer satisfaction.
Role of Wire Bending Equipment
Wire bending equipment plays a pivotal role in shaping custom wires into functional forms that meet diverse application needs. This specialized machinery allows manufacturers to create intricate designs with tight tolerances—something that's increasingly demanded across various sectors today. With advancements like programmable bending machines, achieving complex geometries has never been easier or more efficient.
Incorporating state-of-the-art bending equipment not only streamlines production but also enhances the customization options available for clients seeking unique solutions from their wire manufacturers. These machines enable rapid prototyping and adjustments during production runs without compromising quality or increasing lead times significantly. As industries continue to evolve towards more tailored offerings, investing in sophisticated wire bending equipment will be crucial for staying competitive in the market.
The Wire Fastening Landscape
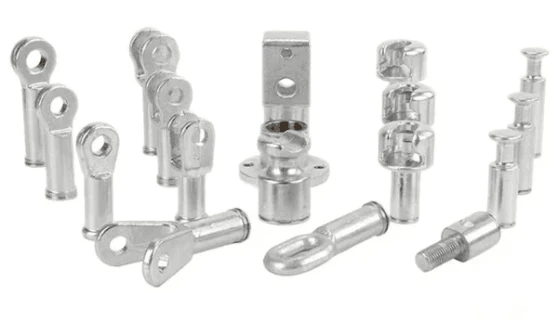
Different Types of Wire Fasteners
Wire fasteners come in various shapes and sizes, each tailored for unique applications within the realm of custom forming. Common types include clips, clamps, ties, and hooks, all engineered to hold components together securely. Additionally, specialized fasteners like spring clips or retaining rings are often used in more complex assemblies where durability and precision are paramount.
The choice of wire fastener largely depends on the intended application and the materials involved. For instance, metal forming processes may require heavy-duty steel fasteners that can withstand high stress and environmental factors. On the other hand, lighter applications might benefit from plastic or aluminum options that offer flexibility without compromising strength.
Ultimately, understanding these different types will empower you to select the best fit for your projects while optimizing performance and safety standards through effective wire manufacturing techniques.
Factors Influencing Fastener Selection
Choosing the right wire fastener isn't just about picking something off the shelf; several factors come into play that can significantly impact your project’s success. First and foremost is load capacity—how much weight or force will your fastener need to endure? This consideration directly influences both material selection and design when engaging with custom wire solutions.
Another critical factor is environmental conditions such as temperature fluctuations or exposure to moisture and chemicals. In these cases, selecting corrosion-resistant materials becomes essential to ensure longevity in harsh environments—something that good wire manufacturers will always keep at the forefront during their production processes.
Lastly, ease of installation should not be overlooked; some designs require specialized tools or equipment for proper fitting while others allow for quick assembly with minimal effort using standard wire bending equipment. Balancing these factors ensures you choose a reliable fastening solution tailored specifically for your unique needs.
Customization Options in Wire Fasteners
One size does not fit all when it comes to wire fastening solutions; that's where customization shines! Many manufacturers offer bespoke options that allow you to tailor dimensions, shapes, finishes, and even materials according to your project's requirements—making custom forming an attractive choice for businesses seeking precision-engineered components.
Customization extends beyond mere aesthetics; it includes considerations around functionality as well. For instance, adjustable tension features can be integrated into certain types of fasteners which allows them to perform optimally under varying loads—a game changer when working with dynamic systems requiring flexibility over time.
Furthermore, collaborating closely with skilled wire manufacturers can yield innovative designs that enhance overall product performance while reducing manufacturing costs through efficient use of resources—proving once again that investing time into selecting customized solutions pays off handsomely down the line!
Spotlight on Spark Fittings

Overview of Spark Fittings' Expertise
Spark Fittings specializes in various aspects of wire forming, from design to production, making them a one-stop shop for all your custom forming requirements. Their team consists of skilled professionals who understand the intricacies of wire bending equipment and the nuances involved in different metal forming techniques. This expertise allows them to tackle complex projects that require tailored solutions and high-quality outcomes.
How Spark Fittings Enhances Wire Forming
One way Spark Fittings enhances wire forming is through their state-of-the-art technology and advanced wire bending equipment that optimizes production efficiency. By utilizing cutting-edge machinery, they can produce intricate designs with remarkable accuracy while minimizing waste during the manufacturing process. This not only improves the quality of custom wire products but also helps clients save on costs associated with material waste.
Moreover, their focus on customer collaboration ensures that every project aligns perfectly with client specifications, leading to enhanced satisfaction and superior results. They take pride in providing comprehensive support throughout the project lifecycle—offering insights into material selection, design tweaks, and final adjustments based on real-time feedback from clients. This level of service sets them apart from other wire manufacturers who may not offer such personalized attention.
Case Studies Demonstrating Quality Improvements
Real-world examples showcase how Spark Fittings has successfully improved quality through their innovative approaches to custom wire solutions. In one notable case study involving a major automotive supplier, they were able to enhance the durability and performance of critical components by implementing advanced metal forming techniques tailored specifically for high-stress applications. The result was a significant reduction in product failures and an overall increase in customer satisfaction ratings.
Another case highlighted how Spark Fittings collaborated with an electronics manufacturer struggling with inconsistent product dimensions due to outdated processes. By integrating modern wire manufacturing practices combined with precise customization options for their fasteners, they achieved tighter tolerances across all components—leading to improved assembly efficiency and reduced operational costs for the client.
These case studies illustrate not just the capabilities of Spark Fittings but also emphasize their commitment to continuous improvement within the realm of wire forming services—ensuring clients receive nothing short of excellence every time.
Choosing the Right Wire Manufacturers
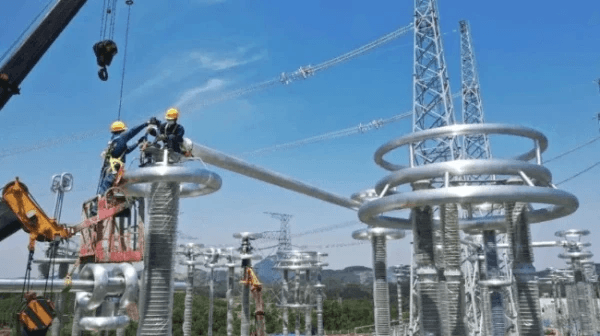
Key Qualities to Look For in Manufacturers
First and foremost, look for manufacturers who have extensive experience in wire manufacturing and custom forming. A seasoned provider will likely have mastered various techniques and technologies, including advanced wire bending equipment that enhances precision and efficiency. Additionally, strong customer service is essential; a responsive manufacturer can adapt to your project requirements and address any concerns promptly.
Another critical quality is the manufacturer's ability to offer a diverse range of forming services tailored to different applications. This flexibility ensures that you can find the right custom wire solutions for unique projects without compromising on quality or lead times. Lastly, don't forget about innovation; manufacturers who invest in research and development are more likely to stay ahead of industry trends and deliver cutting-edge products.
Importance of Certifications and Standards
Certifications play a vital role in ensuring that your chosen wire manufacturers adhere to industry standards for quality and safety. Look for certifications such as ISO 9001, which indicates a commitment to continuous improvement in processes related to metal forming and custom forming services. These standards not only enhance product reliability but also provide peace of mind that you're working with reputable companies.
Moreover, adherence to standards ensures consistency across production runs, which is crucial when you're relying on specific dimensions or tolerances in your wire forming projects. A manufacturer’s commitment to following established guidelines demonstrates their dedication to producing high-quality custom wire products while minimizing defects or errors during production runs. So when evaluating potential partners, prioritize those who proudly display their certifications.
Comparing Costs vs. Quality in Wire Manufacturing
While it's tempting to choose the lowest-cost option when selecting wire manufacturers, remember that price often reflects quality—especially in specialized fields like metal forming and custom wiring solutions. Prioritizing cost over quality may lead you down a path filled with subpar materials or unsatisfactory workmanship that could jeopardize your project's success down the line. Instead, seek out manufacturers who strike a balance between competitive pricing while maintaining high standards of craftsmanship.
When comparing costs versus quality, consider factors such as material sourcing practices and manufacturing processes employed by each company; these elements can significantly influence both price points and end product performance. Request samples from prospective partners so you can assess their work firsthand before making any commitments—this way you'll be able to gauge whether their offerings align with your expectations for durability and functionality within your projects.
In conclusion, choosing the right wire manufacturer requires careful consideration of several key factors including experience level, certifications held by potential partners as well as an honest assessment of costs versus quality offered throughout various stages of production—from design through delivery!
Conclusion
In the ever-evolving landscape of manufacturing, custom wire solutions stand out as a pivotal element in enhancing product quality and performance. By leveraging advanced wire forming and metal forming techniques, businesses can ensure that their components meet specific requirements while maximizing efficiency. The integration of custom forming services not only improves functionality but also contributes to overall operational excellence.
Enhancing Quality with Custom Wire Solutions
The significance of custom wire solutions cannot be overstated when it comes to enhancing quality. With tailored designs and precision engineering, these solutions allow manufacturers to create components that fit perfectly within their intended applications. By utilizing specialized wire bending equipment, companies can achieve intricate shapes and configurations that standard products simply cannot offer.
Custom wire also plays a critical role in ensuring durability and reliability across various industries. Whether it's automotive, aerospace, or electronics, the right custom forming approach can lead to significant improvements in performance metrics. As businesses increasingly prioritize quality assurance, investing in reputable wire manufacturers becomes essential for achieving superior results.
Future Trends in Wire Forming and Fastening
Looking ahead, the future of wire forming and fastening is poised for exciting developments driven by technological advancements. Innovations in automation and robotics are set to revolutionize the wire manufacturing process, allowing for greater precision and efficiency than ever before. Additionally, sustainable practices are gaining traction as manufacturers seek eco-friendly materials and processes that minimize waste.
The rise of smart manufacturing will also influence how custom wire solutions are produced and utilized. With real-time data analytics integrated into production lines, companies will be able to optimize their operations dynamically based on demand fluctuations or design changes. This adaptability will further enhance the capabilities of metal forming services while ensuring high-quality outcomes.
Making Informed Choices for Your Projects
When it comes time to select the right partners for your projects involving custom wire solutions, informed decision-making is crucial. Start by evaluating potential wire manufacturers based on their experience with specific applications relevant to your needs; this ensures you receive expert guidance tailored to your industry challenges. Don't forget to consider certifications and standards—these indicators reflect a commitment to quality that can significantly impact your project's success.
Cost is always a factor; however, it's essential not just to chase the lowest price but rather find a balance between cost-effectiveness and quality assurance in your chosen suppliers’ offerings. Engaging with manufacturers who demonstrate transparency about their processes—including details on their wire bending equipment—can provide valuable insights into expected outcomes for your project’s timeline and budget constraints. Ultimately, making informed choices will empower you to harness the full potential of custom wire solutions while elevating your product's marketability.