Introduction
In the world of manufacturing, custom wire forming machines play a pivotal role in creating intricate and precise components that meet specific design requirements. These machines are essential for various applications, particularly in the automotive industry, where high-quality parts are crucial for performance and safety. Understanding the nuances of custom wire bending and forming processes can significantly impact production efficiency and product quality.
Understanding Custom Wire Forming Machines
Custom wire forming involves the manipulation of metal wire into specific shapes and configurations tailored to unique specifications. This process is facilitated by advanced wire forming machines, which utilize cutting-edge technology to ensure accuracy and repeatability in every bend and twist. From simple brackets to complex assemblies, custom wire technologies enable manufacturers to produce a wide range of products that cater to diverse industry needs.
Importance in Automotive Manufacturing
The automotive industry relies heavily on custom wire forming due to its demand for precision-engineered components that withstand rigorous conditions. Custom wire bending techniques allow manufacturers to create parts that fit seamlessly within vehicles while maintaining structural integrity under stress. As vehicles become more sophisticated, incorporating advanced features often requires innovative stainless steel wire forming solutions that enhance durability without compromising weight or performance.
Spotlight on Leading Companies
Several companies have emerged as leaders in the field of custom wire form manufacturing, setting benchmarks for quality and innovation. These manufacturers leverage state-of-the-art equipment and skilled craftsmanship to deliver exceptional products tailored to their clients' needs. By partnering with top-tier wire form manufacturers, businesses can ensure they receive reliable components that enhance their production capabilities while staying ahead in a competitive market.
The Basics of Custom Wire Forming
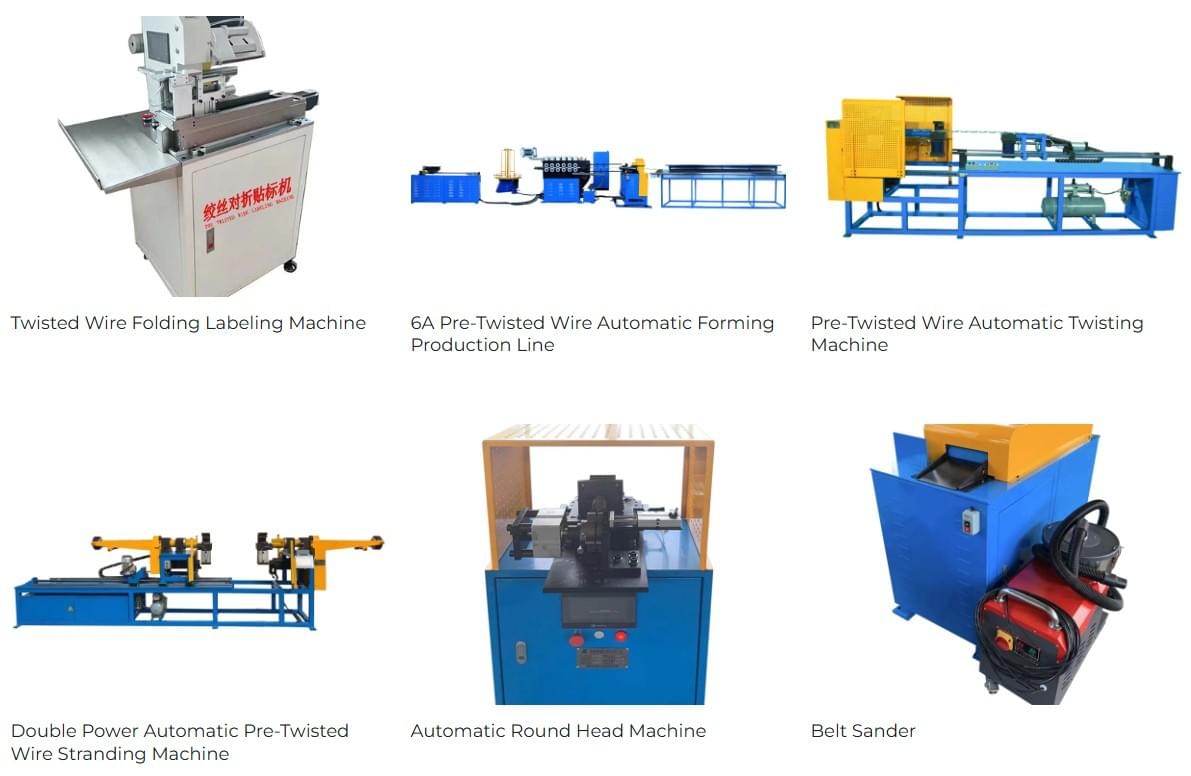
Custom wire forming is a fascinating process that allows manufacturers to create intricate shapes and components from wire materials. This method is essential for industries like automotive manufacturing, where precision and customization are key. Understanding the basics of custom wire forming can help businesses make informed decisions when selecting the right technologies and suppliers.
Definition and Overview
Custom wire forming refers to the process of bending, shaping, and manipulating wire into specific configurations tailored for various applications. This technique is crucial in creating components that fit exact specifications, especially in sectors such as automotive manufacturing where performance and reliability are paramount. By utilizing custom wire technologies, manufacturers can produce everything from simple brackets to complex assemblies that enhance vehicle functionality.
Types of Custom Wire Forming Machines
There are several types of custom wire forming machines available on the market, each designed for specific applications and materials. Common types include CNC (Computer Numerical Control) machines, which offer high precision for complex shapes; automatic bending machines that streamline production; and manual machines suited for simpler tasks or small-scale operations. Each machine type has its own strengths, making it vital for manufacturers to choose based on their unique requirements in custom wire bending.
Key Features to Look For
When selecting a custom wire forming machine, there are several key features to consider that can greatly impact efficiency and output quality. Look for machines with adjustable settings that allow flexibility in design changes without significant downtime—this adaptability is crucial in today's fast-paced manufacturing environment. Additionally, consider features such as material compatibility (especially with stainless steel wire forming), user-friendly interfaces, and robust safety mechanisms to ensure smooth operation while minimizing risk.
Custom Wire Bending for Automotive Applications
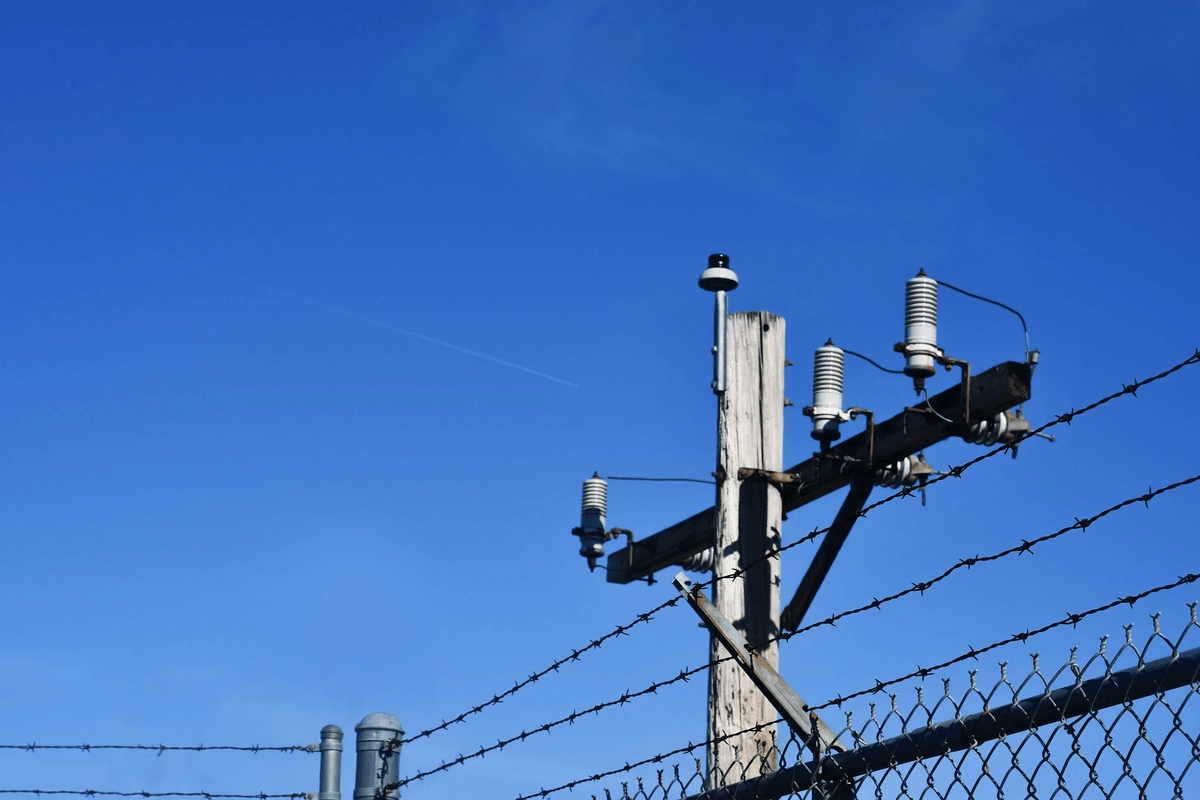
Custom wire bending is a crucial aspect of automotive manufacturing, allowing for the creation of components that meet specific design requirements and performance standards. This process leverages advanced custom wire forming techniques to produce intricate shapes with precision, ensuring that each piece fits perfectly within the larger assembly. With the right approach to custom wire technologies, manufacturers can enhance both functionality and aesthetics in their automotive designs.
Benefits of Custom Wire Bending
The benefits of custom wire bending are manifold, particularly in the automotive sector. First and foremost, it allows for greater design flexibility; manufacturers can create unique shapes that traditional methods might not accommodate. Additionally, custom wire forming often results in reduced material waste and improved production efficiency, as machines can be programmed to produce exactly what is needed without excess.
Another significant advantage lies in the strength and durability of bent wires made from materials like stainless steel. Stainless steel wire forming offers resistance to corrosion and wear, making it ideal for components exposed to harsh conditions in vehicles. Moreover, custom wire bending enables precise tolerances that enhance overall vehicle performance while maintaining safety standards.
Applications in the Automotive Industry
In the automotive industry, custom wire bending finds applications across various components—from suspension systems to wiring harnesses and brackets. For instance, bent wires are essential for creating robust suspension linkages that must endure significant stress while maintaining stability on uneven terrains. Similarly, custom wire forms are utilized in electrical systems where complex shapes allow for efficient routing without compromising safety or functionality.
Another application includes interior elements such as seat frames and headrest supports where aesthetic appeal meets structural integrity through clever design using custom wire technologies. The versatility of these applications underscores why many leading manufacturers rely on advanced wire forming machines to meet their specific needs effectively.
Choosing the Right Custom Wire Technologies
Selecting the right custom wire technologies is critical for achieving optimal results in automotive applications. Key considerations include assessing machine capabilities—such as bend radius limits and material compatibility—to ensure they align with project requirements. Engaging with reputable wire form manufacturers who specialize in stainless steel wire forming can also provide insights into innovative techniques that enhance production quality.
Moreover, evaluating factors like turnaround time and customization options offered by different suppliers can lead to better partnerships that foster long-term success in production runs. By focusing on these elements when choosing technologies or partners, companies can streamline their processes while enhancing product performance through superior design execution.
Stainless Steel Wire Forming Techniques

Stainless steel wire forming is a critical aspect of custom wire technologies, particularly in industries where durability and corrosion resistance are paramount. This material's unique properties make it an ideal choice for various applications, especially in the automotive sector. Understanding the advantages, methods, and comparisons with other materials can help businesses make informed decisions when selecting custom wire forming solutions.
Advantages of Stainless Steel in Wire Forming
One of the primary advantages of stainless steel in custom wire forming is its exceptional strength-to-weight ratio. This means that components made from stainless steel can withstand significant stress while remaining lightweight—an essential factor in automotive design. Additionally, stainless steel offers outstanding corrosion resistance, making it suitable for harsh environments where exposure to moisture and chemicals is common.
Another benefit is its aesthetic appeal; stainless steel provides a sleek finish that enhances the overall look of custom wire forms. This visual aspect is crucial for automotive manufacturers who strive for both functionality and style in their products. Furthermore, stainless steel's longevity ensures that components maintain their integrity over time, reducing maintenance costs and enhancing product reliability.
Lastly, stainless steel can be easily shaped into complex designs during the custom wire bending process without compromising its structural integrity. This adaptability allows manufacturers to create intricate parts tailored to specific applications while ensuring high performance standards are met consistently.
Methods of Stainless Steel Wire Forming
One common approach is CNC (Computer Numerical Control) bending, which allows for precise control over the shaping process while minimizing human error. This method ensures that each custom wire form meets exact specifications required by automotive applications.
Another popular technique involves using specialized wire forming machines designed specifically for stainless steel processing. These machines utilize advanced technology to create consistent bends and shapes across multiple units efficiently—ideal for mass production scenarios where uniformity is key. Additionally, manual bending techniques may still be employed for smaller runs or highly customized components requiring a personal touch.
Welding also plays a significant role in stainless steel wire forming; it allows different sections of formed wires to be joined securely without compromising their strength or durability. By employing various welding techniques such as TIG (Tungsten Inert Gas) or MIG (Metal Inert Gas), manufacturers can create robust assemblies tailored to specific requirements within the automotive industry.
Comparative Analysis with Other Materials
When comparing stainless steel with other materials used in custom wire forming processes—such as aluminum or copper—several distinctions emerge that affect selection criteria significantly. While aluminum boasts lightweight properties beneficial for certain applications, it lacks the same level of strength and corrosion resistance offered by stainless steel wires. For industries like automotive manufacturing where performance under stress matters most, this difference becomes crucial.
Copper has excellent conductivity but falls short in terms of strength compared to stainless steel; moreover, copper tends to corrode more quickly when exposed to environmental factors unless adequately protected through coatings or treatments. Therefore, while copper may excel in electrical applications requiring high conductivity levels, it's not always suitable when durability takes precedence over electrical performance.
Ultimately, choosing between these materials hinges on specific project requirements and desired outcomes regarding cost-effectiveness versus long-term reliability—two essential factors influencing decisions among leading wire form manufacturers today! As businesses continue exploring innovative ways to enhance production efficiency through advanced technologies like automated systems integrated into their workflows—the value proposition presented by utilizing superior materials like stainless steels remains undeniable!
Selecting Reliable Wire Form Manufacturers
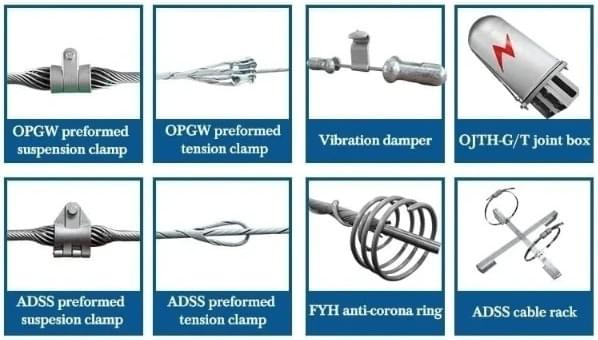
Choosing the right wire form manufacturer is crucial for ensuring quality and efficiency in your custom wire forming projects. With a plethora of options available, it’s essential to establish clear criteria to help narrow down your choices. By focusing on experience, technology, and customer support, you can find manufacturers that align with your specific needs in custom wire bending and stainless steel wire forming.
Criteria for Choosing Manufacturers
When selecting a wire form manufacturer, consider their experience in the industry as a primary criterion. An established company with a proven track record in custom wire technologies is more likely to deliver high-quality products that meet stringent automotive standards. Additionally, evaluate their technological capabilities; manufacturers that utilize advanced wire forming machines can provide precision and efficiency that newer or less equipped companies may lack.
Another critical factor is the manufacturer's ability to offer customization options tailored to your specific requirements. Whether you need complex shapes or unique stainless steel wire forming techniques, ensure they have the flexibility to accommodate your needs. Finally, don't overlook customer service; strong communication and support during the production process can make all the difference in achieving successful outcomes.
Top Wire Form Manufacturers in the Industry
The market boasts several reputable wire form manufacturers known for their excellence in custom wire forming and bending solutions. Companies like Spark Fittings stand out for their commitment to quality and innovation in stainless steel wire forming applications within the automotive sector. Others such as WireTech Solutions and Precision Wire Forms also have impressive portfolios showcasing advanced capabilities in custom wire technologies.
These top manufacturers not only provide high-quality products but also demonstrate a robust understanding of industry trends and customer needs. They often invest heavily in research and development to stay ahead of technological advancements related to wire forming machines. Partnering with these leaders can significantly enhance your production processes while ensuring reliability.
How to Build Strong Supplier Relationships
Building strong relationships with your chosen wire form manufacturers is essential for long-term success in custom wire projects. Start by fostering open lines of communication; regular check-ins can help address any issues early on while promoting transparency throughout production cycles involving custom wire bending or other specialized services.
Additionally, consider collaborating closely on design specifications; sharing insights about project goals and challenges allows both parties to work together effectively toward common objectives involving stainless steel or other material forms. Establishing trust through consistent interactions will strengthen partnerships over time, leading to improved quality control and timely deliveries.
Lastly, be proactive about providing feedback regarding product performance; this not only shows appreciation but also encourages continuous improvement from suppliers who value client input on their manufacturing processes involving various custom wires.
The Role of Wire Forming Machines in Production
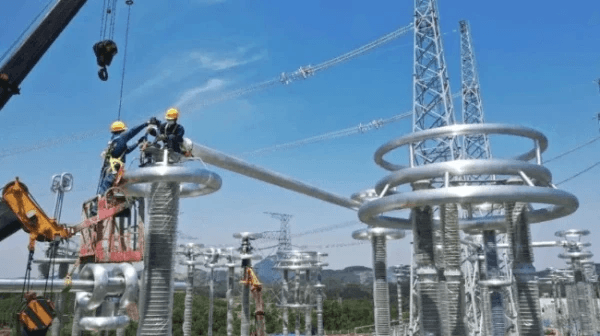
In the fast-paced world of manufacturing, wire forming machines serve as the backbone for producing high-quality custom wire forms. These machines are designed to deliver both efficiency and precision, which are crucial in meeting the stringent demands of industries such as automotive manufacturing. With advancements in technology, the ability to create intricate designs through custom wire bending has never been easier or more reliable.
Efficiency and Precision in Production
Custom wire forming machines have revolutionized production processes by enhancing efficiency and precision. By automating tasks traditionally done by hand, manufacturers can significantly reduce production time while maintaining high standards of quality. This is particularly important when dealing with stainless steel wire forming, where even minor inaccuracies can lead to costly errors and rework.
The integration of advanced software and robotics into wire forming machines has further increased their capability to produce complex shapes with minimal waste. This allows for a more streamlined workflow, enabling manufacturers to meet tight deadlines without compromising on quality. Ultimately, investing in top-notch custom wire technologies ensures that businesses remain competitive while delivering exceptional products.
Innovations in Wire Forming Machines
The landscape of wire form manufacturers is constantly evolving thanks to innovations that enhance machine capabilities. Recent developments include smart technology integration that allows for real-time monitoring and adjustments during production runs, which helps maintain consistency across batches of custom wire forms. Moreover, these innovations often lead to energy-efficient operations—an important consideration for companies focused on sustainability.
Another exciting trend is the use of advanced materials in machine components themselves, leading to increased durability and reduced maintenance costs. These enhancements not only improve machine performance but also extend their lifespan, making them a wise investment for any manufacturer looking to excel in custom wire bending applications. As these technologies continue to advance, we can expect even greater efficiencies and capabilities from future generations of wire forming machines.
Real-World Examples of Effective Use
Several industry leaders have successfully implemented cutting-edge wire forming machines into their production lines with impressive results. For instance, an automotive manufacturer recently adopted a new custom wire bending system that allowed them to reduce cycle times by 30%, all while increasing output quality through precise stainless steel wire forming techniques. This shift not only improved profitability but also enhanced customer satisfaction due to faster delivery times.
Another example involves a company specializing in electronic components that utilized innovative wiring solutions from top-tier wire form manufacturers to create intricate designs required for modern devices. By leveraging advanced custom wire technologies, they were able to streamline their production process significantly while ensuring compliance with strict industry standards. Such real-world applications showcase how embracing modern machinery can drive success across diverse sectors reliant on customized solutions.
Conclusion
In the rapidly evolving landscape of automotive manufacturing, custom wire forming plays a pivotal role in ensuring both quality and efficiency. With advancements in technology and materials, the future of custom wire bending looks promising, offering innovative solutions tailored to industry demands. As manufacturers seek to enhance production processes, understanding these trends becomes crucial for staying ahead of the competition.
Future Trends in Custom Wire Forming
The future of custom wire forming is set to witness remarkable advancements driven by automation and smart technologies. Innovations such as AI-driven design software will streamline the development process of custom wire forms, allowing for quicker prototyping and enhanced customization options. Moreover, as sustainability becomes a priority, manufacturers are increasingly exploring eco-friendly materials and processes in stainless steel wire forming to minimize their environmental impact.
Enhancing Production with Automation
Automation is revolutionizing how wire forming machines operate, leading to unprecedented levels of precision and efficiency in production lines. By integrating automated systems into custom wire technologies, manufacturers can achieve faster turnaround times while reducing human error significantly. This shift not only enhances productivity but also allows for more complex designs that were previously challenging with traditional methods of custom wire bending.
Partnering with Spark Fittings for Success
When it comes to navigating the intricate world of wire form manufacturers, partnering with a reliable company like Spark Fittings can make all the difference. Their expertise in custom wire forming ensures that clients receive high-quality products tailored to their specific needs while maintaining competitive pricing. Building strong supplier relationships with companies like Spark Fittings fosters collaboration and innovation—key ingredients for success in today’s dynamic automotive landscape.